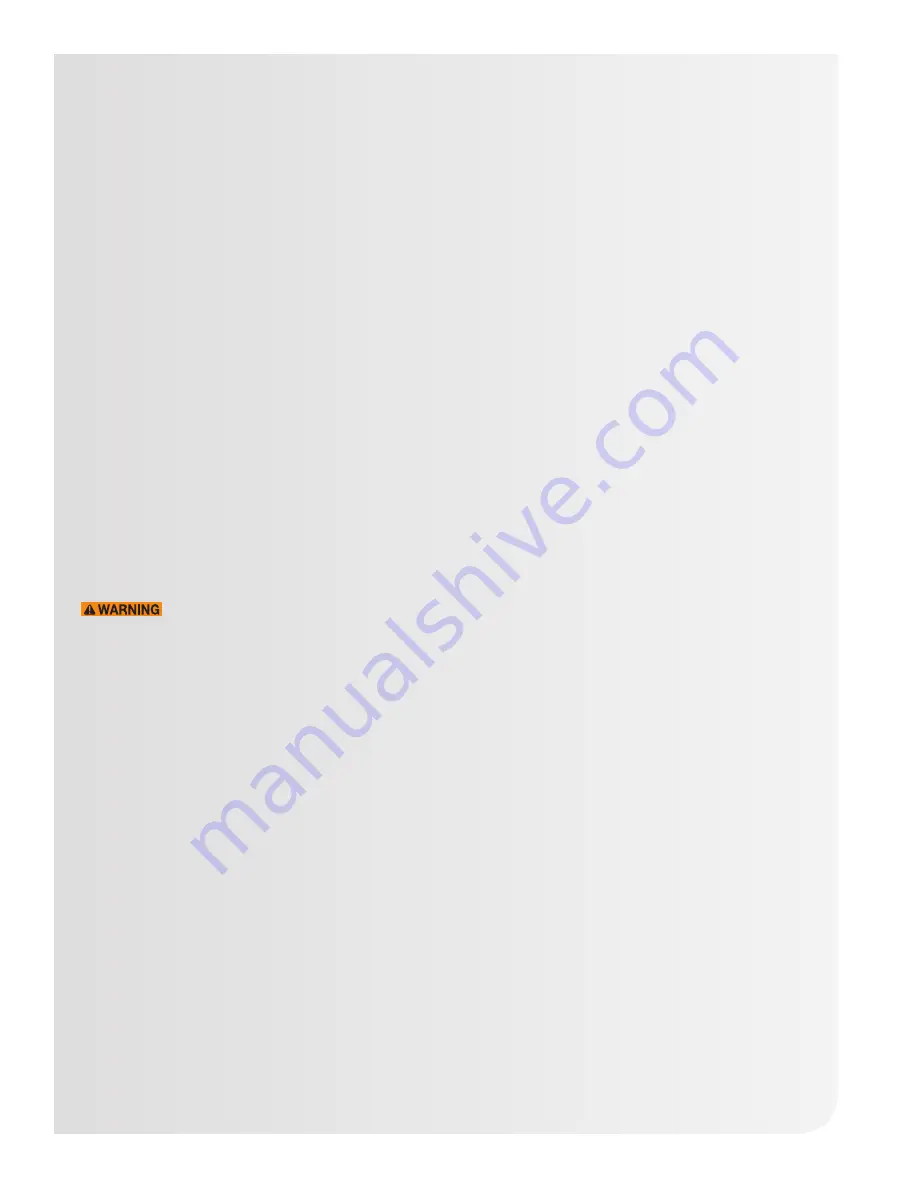
26
Maintenance
General
Each unit on a project will
have its own unique operating
environment and conditions
which dictate a maintenance
schedule for that unit that
may be different from other
equipment on the project. A
formal regular maintenance
schedule and an individual
unit log should be established
and maintained. Following this
schedule will help maximize the
performance and service life of
each unit on the project.
The safety considerations listed
in the front of this manual should
be followed during any service
and maintenance operations.
For more detailed service
information consult your Sales
Representative or the factory.
Disconnect power supply from
the unit before servicing.
Filter
Since the Vertical Hi-Stack
Fan Coil is a draw-through coil
type, filter must be changed
or cleaned a minimum of four
times a year. Under certain
operating conditions, it may be
necessary to change or clean the
filters more frequently to obtain
maximum unit performance.
Coil
Coils may be cleaned by
removing the motor/blower
assembly and air filter, providing
access to the air entry side of
the coil. Brush the entire finned
surface with a soft bristled
brush, brushing parallel to the
fins, taking care not to damage
the fins. Brushing should be
followed by cleaning with a
vacuum cleaner. Compressed air can
also be used by blowing air through
the coil fins from the leaving air side,
again followed by vacuuming. If fins
are damaged during the cleaning
process, a 12 fins per inch fin comb
can be used to straighten the fins.
For a deeper cleaning, spray the
finned surface with a neutral cleaning
solution and rinse thoroughly.
Zehnder Rittling recommends using
neutral pH cleaners. Avoid the use
of strong acids and strong base
cleaners. Thus, cleaners with pH
range from 5 to 11 are suitable for coil
cleaning. This range includes such
over-the-counter cleaners as Simple
Green
®
All Purpose Cleaner, or HVAC
coil cleaners like Nu-Calgon Evap
Pow'r
®.
Strong acidic cleaners (pH of
5 or less) that contain hydrochloric,
sulfuric, nitric or acetic acid are
not recommended for use on
copper-tube, aluminum fin coils.
Presence of these acids will result
in rapid corrosion of the metals.
Strong alkali (base) cleaners (pH
of 11 or more) containing sodium,
potassium or ammonium hydroxide
are not recommended as they will
aggressively corrode aluminum
tubes and fins. Strong ammonium
hydroxide cleaners will also cause
stress corrosion cracking of copper
tubes. Zehnder Rittling recommends
completely rinsing all cleaners from
the coil, including cleaners identified
as no-rinse cleaners. Residual
cleaners may decompose over time
producing low molecular weight,
organic acids that lead to formicary
corrosion.
Failure to maintain a clean coil
surface will result in reduced airflow,
reduced performance and increased
power consumption. Clean the coil at
every inspection. Units provided with
the proper type of air filters, replaced
regularly, will require less frequent
coil cleaning. Before performing
service at or near any heating coil,
piping or valve, disconnect all
power, close all isolation valves
and allow the equipment to cool.
Drain
Once yearly, preferably at the
start of the cooling season, the
drain pan should be checked and
cleaned if necessary. A flexible
probe for 3/4-inch pipe may be
used to clear any obstruction
from the line, or the drain tube
may be removed through the
lower area of the return-air
opening, should more thorough
cleaning be needed.
Motor/blower assembly
The type of fan operation is
determined by the control
components and their method of
wiring. This may vary from unit to
unit. Refer to the wiring diagram
located in a zip-lock plastic bag
on the air block-off plate of each
unit for that unit’s individual
operating characteristics.
All motors have permanently
lubricated bearings so no further
field lubrication is ever required.
The unit motor/blower is direct-
drive assembly. Remove the air
block-off plate to gain access to
the motor/blower assembly. The
entire motor/blower assembly
can be removed from its track
through the return-air grille
for field servicing by removing
a single screw and quick
connect. Disconnect all remote
electric power supplies before
servicing as motors can start
automatically.
Dirt and dust should not be
allowed to accumulate on the
blower wheel or housing. Failure
to keep this clean may result in
an unbalanced wheel condition
which can lead to a damaged
blower wheel or motor. The wheel
and housing may be cleaned