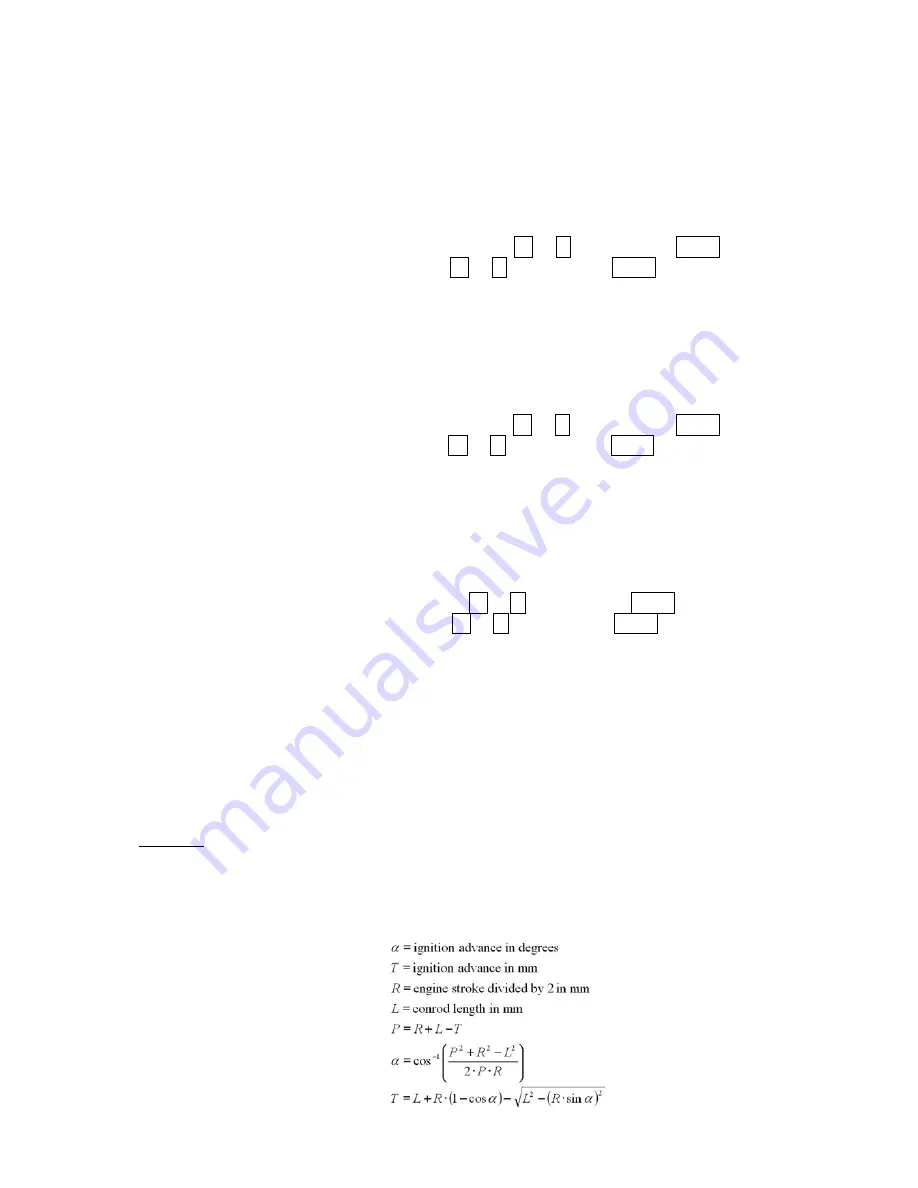
- 7 -
Deviation means how accurate valve is moved to calculated position. If deviation is too low
then servo motor won't be stabile – it will always search for calculated position in small
movements. Default setting is +-5% and should meet in most cases.
19. Max
Close
Position
Enter menu and move to
Close Position
with pressing + or - and then press enter .
Now you can set close position with pressing + or - and then press enter .
Max close position is when curve is set to 0%. This close position can be moved to any
desired position. For RZ350 default close position is 240. Max close position can be moved to
deeply closed or less closed position.
20.
Max Open Position
Enter menu and move to
Open Position
with pressing + or - and then press enter .
Now you can set open position with pressing + or - and then press enter .
Max open position is when curve is set to 100%. This open position can be moved to any
desired position. For RZ350 default open position is 512. Max open position can be moved to
more open or less open position.
21. PV
Test
Enter menu and move to
PV Test
with pressing + or - and then press enter .
Now you can set valve position with pressing + or - and then press enter .
PV test can be used for testing or measuring valve position. Valve can be moved to any
position from 0% to 100%, without engine running.
22.
MECHANICAL SETTINGS (Static Angle)
Static Angle
is ignition advance angle, set with stator (generator).
Measure this angle with dial gauge. This measured
Static Angle
is your maximum advance
angle you can set with
PCDI
.
Example:
Measured Static Angle = 39.2deg (this angle you must enter in PCDI)
Calculating mm to deg or vice versa: