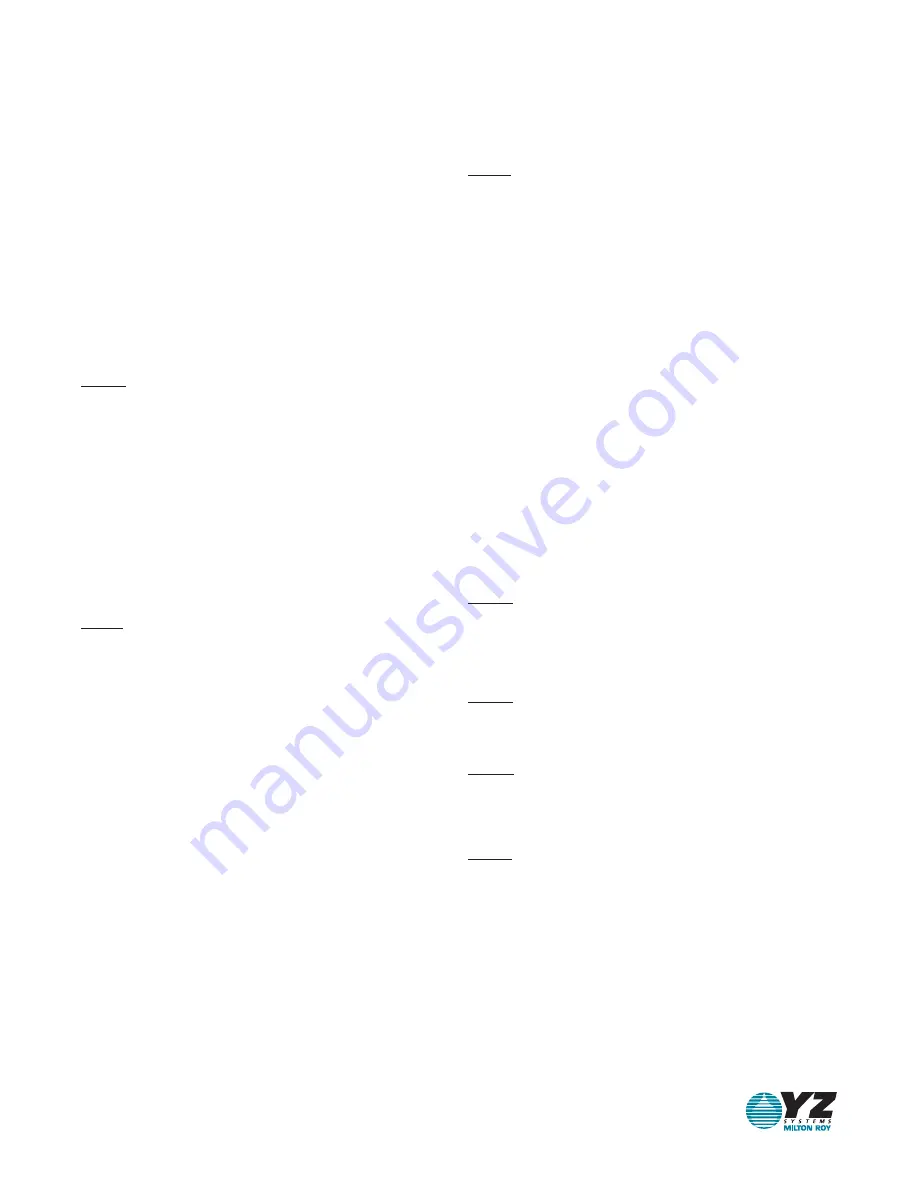
DP-2010L Version 04032001 ATEX Rev.
YZ Systems, Inc. • 3101 Pollok Drive • Conroe, Texas • USA • 77303 • P: 936.788.5793 • F: 936.788.5720
31
Diagram #9: DuraSite Portable Sample Vessel Instructions
Purpose: The DuraSite Portable Sample Vessel permits the
user to remove a liquid or gas hydrocarbon sample from a
pipeline or a sampling device. This is accomplished without
changing the pressure of the product or exposing it to a
contaminant fluid. If properly used and maintained the Dur-
aSite will provide many years of safe, accurate and clean
sampling.
Use: The DuraSite is a very safe device to use. As with any
equipment dealing with flammable products, it is mandatory
that a good, thorough operator training procedure be estab-
lished prior to use.
Typical use of the cylinder would be as follows:
Step 1: (In The Lab) Connect a regulated inert gas supply to
the pre-charge valve. The product valve should be open. By
carefully controlling the pre-charge valve and the regulator, the
cylinder can be slowly charged with pre-charge gas (NOTE:
This should be done slowly to prevent slamming the piston
down to the opposite end). The pressure on the pre-charge
pressure gauge should be brought to a reading of 10-50 psi
above the expected pressure of the product in the field . Close
the pre-charge valve and disconnect the gas supply. Check the
pre-charge valve, relief device, and the pre-charge pressure
gauge for leaks. Any leaks should be stopped before continu-
ing. The vessel should be placed in a padded carrying case and
made ready for field use.
Proceed to
EITHER Step 2, or Step 3 as
required for your application.
STEP 2: FOR COLLECTION OF SAMPLE VIA SPOT SAMPLE OR
FROM COMPOSITE ACCUMULATOR VESSEL.
2a: Connect the product end of the pre-charged sample vessel
to the product supply.
(Sampler product removal valve, or Pipeline sample probe)
NOTE: the pre-charge pressure gauge reading should be
greater than the product supply pressure reading. If not,
repeat Step 1 above.
2b: Once the vessel is connected to the product supply, it is
necessary to vent a small amount of product prior to filling the
vessel. This assures fresh product and removes any air or gas
when dealing with liquids. This can be done by loosening the
product purge valve a very small amount until the product is
purged. After thorough purging, the product purge valve should
be tightened.
2c: The product pressure gauge reading should be 10-50 psi
below the pre-charge pressure gauge reading. By carefully
opening the pre-charge valve, the pressure becomes equal-
ized, then begins to drop below the product pressure. The pre-
charge valve should be carefully controlled so as to not vent the
pre-charge gas too fast.
2d: When the cylinder becomes a maximum of 80% full (see
volume indicator), all valves should be closed. The product
connection is slowly broken in order to vent any trapped product.
After vessel removal, all connections should be checked for
leaks and the pre-charge and product valve ports capped to
prevent leakage.
2e: Pack the DuraSite in appropriate carrying case to meet
D.O.T. guideline, with D.O.T.
paperwork and transport to lab for analysis.
STEP 3: FOR DIRECT CONNECTION TO
SAMPLER.
3a: Connect the sampler discharge port to the product inlet port
to the DuraSite using 1/8" stainless steel tubing.
3b: (Gas sampling) Connect the pre-charge port to the
DuraSite to the pipeline for pre-charge pressure (Proceed to
step 3d), or configured like the liquid sample application below.
(Step 3c)
3c: (Light sampling) Pre-charge the DuraSite as indicated in
Step 1, then install a pressure relief valve to the pre-charge port
and open the pre-charge valve on the DuraSite. (The pressure
relief valve should have a relief pressure setting of approxi-
mately 100 psi above line pressure.)
3d: Open the product inlet valve of the DuraSite and the purge
valve on the sampler. Next open the purge valve on the product
end of the DuraSite and allow product to purge all lines and
connections out.
3e: Close purge valves and begin sample cycle.
3f: At the end of sample cycle, close product inlet valve on the
DuraSite and remove the DuraSite. Pack the DuraSite in
appropriate carrying case to meet D.O.T. guideline, with D.O.T.
paperwork and transport to lab for analysis.
Step 4: (In The Lab) Prior to analysis, the product should be
mixed. This is accomplished simply and efficiently by inverting
the cylinder end-over-end, causing the mixing ball to fall
through the product. Approximately 10-12 trips of the mixing ball
through the product assures a homogenous solution.
Step 5: The regulated pre-charge gas should be reconnected
to the pre-charge side of the cylinder. The pre-charge gas
supply should remain open during analysis.
Step 6: Purging a small amount of product from the vessel
removes unmixed product from the tee, relief device, gauge,
etc. The unit can now be connected to a chromatograph and
the product analyzed.
Step 7: After analyzing, the remainder of the product should be
dumped and the vessel properly cleaned. Normal cleaning can
be accomplished by rinsing the product end with a petroleum
solvent and flushing with acetone. If a more thorough cleaning
is required, the vessel should be disassembled.
WARNING: A portable sample vessel should never be filled
to more than 80%. This allows a 20% pre-charge cushion to
absorb thermal expansion of the product.
Shipping: Extreme care should be taken when preparing a
vessel for shipment. Both valves should be capped to prevent
possible leakage. The vessel should be placed in a
snug-fitting, well-padded and durable case. All applicable DOT
regulations should be adhered to.