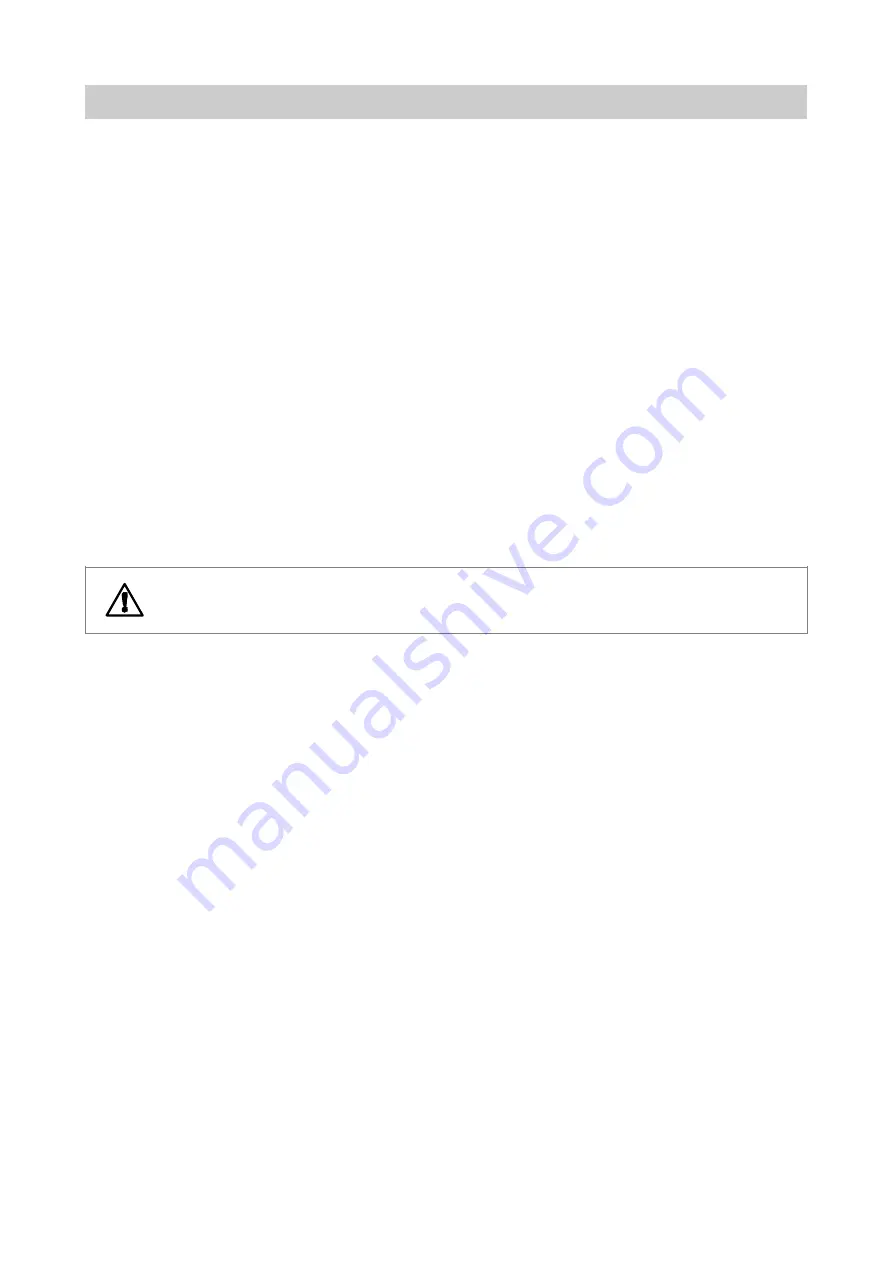
Preparations before Operating this Machine
1) The excavator should be operated by the trained driver, who must comply with the specific
requirements of the local area before operating independently.
2) Unless the drivers have been read carefully the manual, the operation is strictly prohibited.
3) Drivers must wear tight-fitting clothing and appropriate adaptation of the safety items such as
helmets, shoes, gloves, protective glasses, safety belt light before the operation.
4) Every day, before starting, the machine should be carefully checked according to the requirements.
5) Check if the working equipments, the tanks and the hoses are damaged.
6) Remove the dust and dirty around the engine, radiator and the battery.
7) Check if the hydraulic equipment, mailboxes, pipes, joints leak oil. (By the method of inspecting if
there are significant traces of oil).
8) Check if the frame parts (tracks, driving wheels idles, etc) are broken, if the bolts are loose, and if
the connection between the frame and the platform is loose.
9) Check the equipment, and the monitoring device should not be damaged.
10) Clear and check the mirrors, and adjust the angle to the correct vision.
11) Check if the seat belts are broken.
12) Make sure that the machine has been maintained according to the requirements.
Warning: Before the operation, you should make sure that you have understood
and remember the contents related to the safe operation of the “safety regulations”
in the manual.
4-2
Summary of Contents for YC310LC-8
Page 5: ...1 Foreword 1 1...
Page 10: ...1 6...
Page 13: ...1 9...
Page 17: ...2 Safety Regulations 2 1...
Page 28: ...31 Toolbox sign 30 Sign of escaping direction 2 12...
Page 35: ...2 19...
Page 41: ...12 Do not dig towards the machine body 2 25...
Page 47: ...23 Do not use the excavator to drag other devices or objects 2 31...
Page 56: ...2 40...
Page 59: ...3 Components Description 3 1...
Page 61: ...Monitor 3 3...
Page 68: ...reset 2 Throttle knob 3 Igniter 3 10...
Page 77: ...3 19...
Page 84: ...4 Operating Guide 4 1...
Page 94: ...1 Turning when the machine is stopped 4 11...
Page 116: ...4 33...
Page 123: ...5 Maintenance 5 1...
Page 134: ...Checking the fastening of the cylinder cover Checking the fastening of the engine support 5 12...
Page 136: ...5 14...
Page 139: ...5 17...
Page 144: ...5 22...
Page 154: ...5 32...
Page 158: ...5 36...
Page 174: ...6 Accessory Guide 6 1...