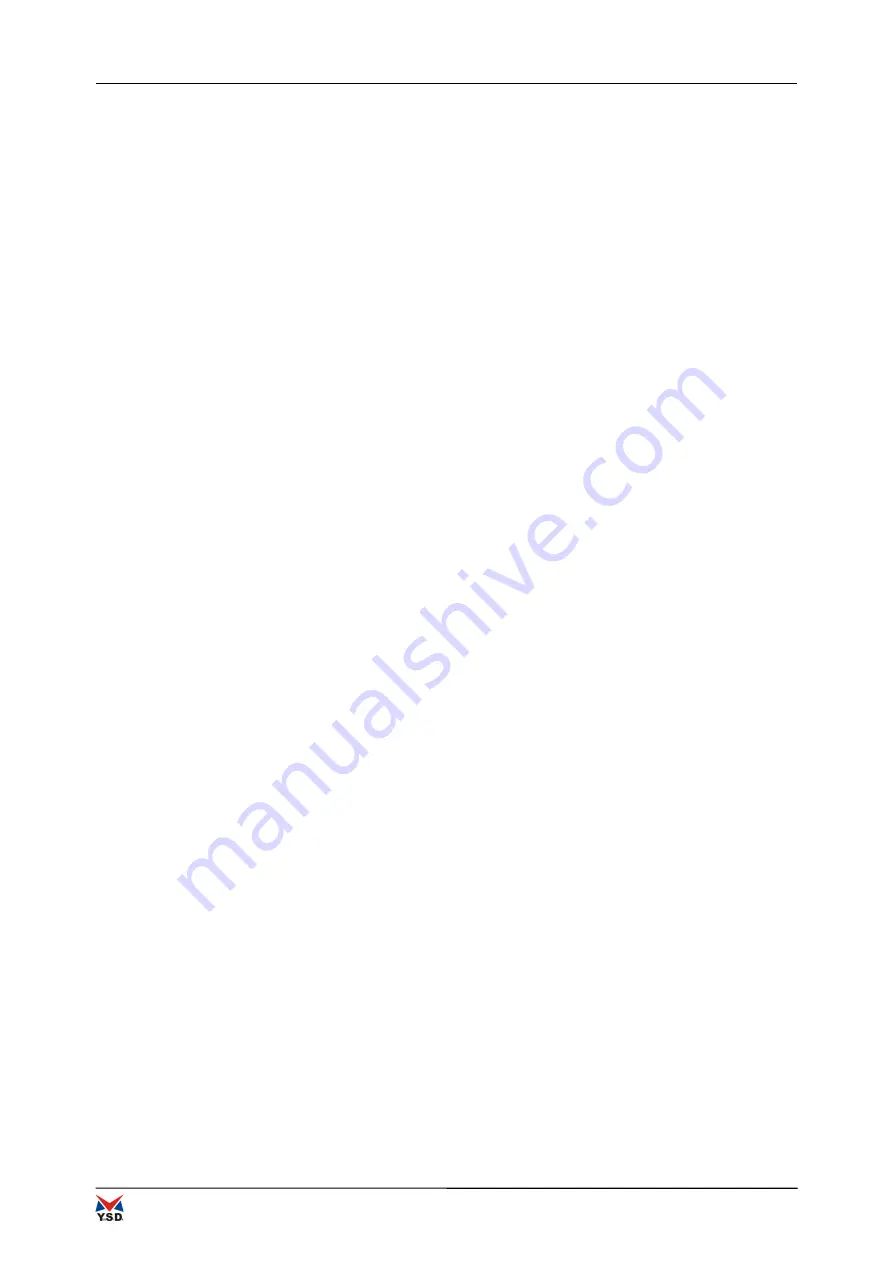
OT2115
Driver
6
Span (SPAN) and offset (OFFSET) adjustments are related. Need to be repeated to
achieve the desired rotation angle range.
Three.Bandwidth potentiometer (ACT.BANDWIDTH): 1 turn potentiometer to adjusts the actuator
controller (2 Hz bandwidth to 9 Hz) signal changes in response speed.
2.2 Actuator
The angle range of the actuator design is 75 degrees (DEG), which controls the
fuel supply mechanism of the engine in the range. Actuator capable of bidirectional
(forward and reverse) output torque. Torque is proportional to the current provided
by the driver.
The actuator uses a sealed bearing and therefore is not maintained. Actuator position sensor
is installed at the end of the rotor, with the drive current loop and the body electrical
isolation.
An inertia wheel is installed on the output shaft of the actuator. The rotation
of the rotating wheel motor has a stable function and should not be removed.
2.3 Angular position sensor
Rotation angle position sensor and actuator rotor coaxial mounting. The sensor
is a linear HALL position sensor. Its power supply voltage is 5VDC. Feedback voltage
is about: 0 degree angle, 2VDC; 75 degree angle, 3VDC (refer to 0V voltage
measurement).
3.Main technical index
3.1 Driver
Operating temperature range:
-40℃~+70℃
Storage temperature range:
-55℃~+105℃
Humidity:
38℃,95%
Attack:
GJB150.16-1986 Environmental test methods for military equipment (impact test)
Vibration: GJB150.16-1986 Environmental test methods for military equipment
(impact test)
Power Supply:
20 VDC~32 VDC(24 VDC 标称)
Output current:
10A Continued;20APeak value,Sustainable 2 seconds