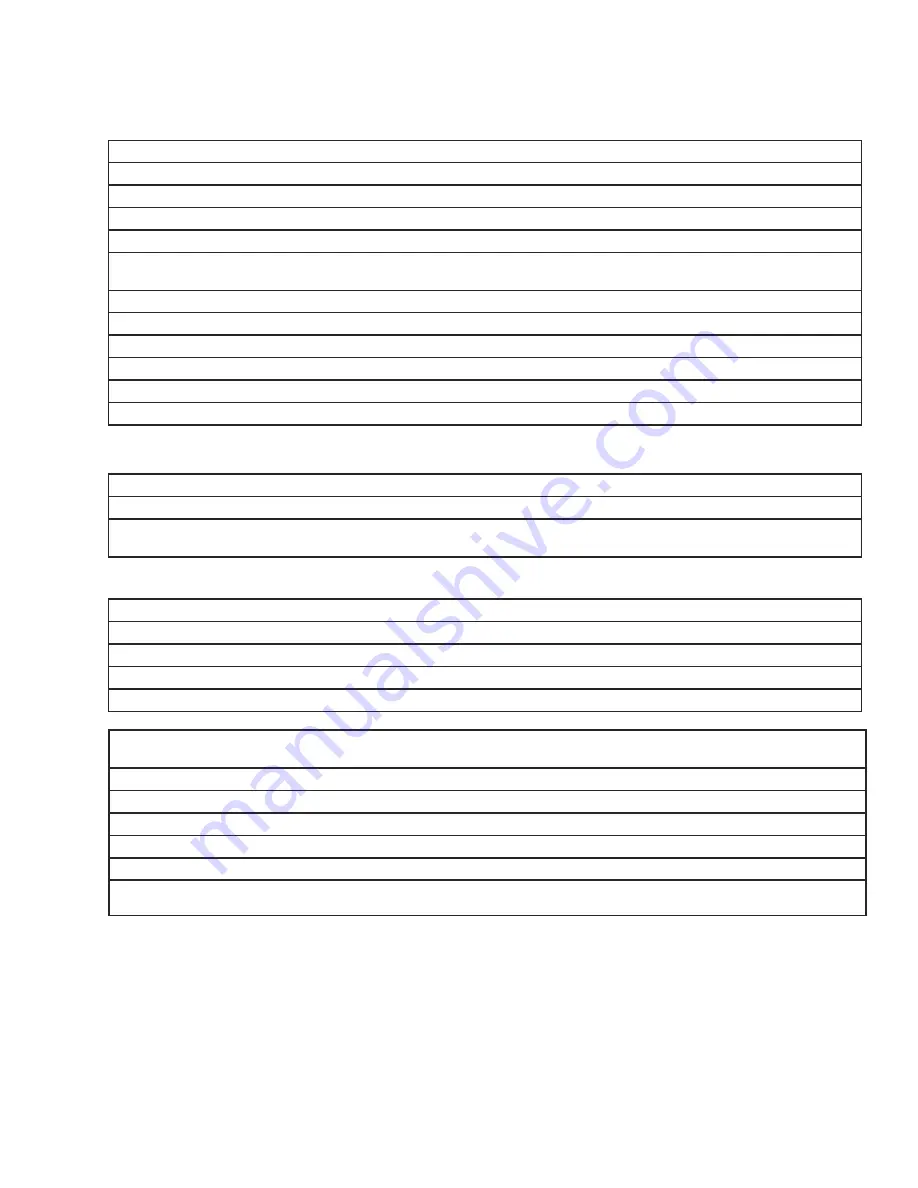
YORK INTERNATIONAL
6
FORM 115.20-NOM4 (105)
INSTALLATION
7
YORK INTERNATIONAL
FORM 115.20-NOM4 (105)
FAN COILS START-UP CHECKLIST
Fan INSPECTION -
The fan should be inspected and cleaned, in conjunction with maintenance of the motor and bearings. It is
important to keep the wheel clean in order to avoid imbalance and vibration.
Check tightness of fan bearing locking collar.
With power off, check blower wheel set screws for tightness and ensure that the blower wheel(s) rotate freely and quietly.
Check tightness of all motor base and mounting bolts.
Check motor connections to ensure that they are secure and made in accordance with the wiring diagram
Rotate all moving components manually. Adjust as required.
NOTE: If the motor and fan have not been operated in the last (4) four weeks or more, lubricate all the bearings and rotate the motor and fan
monthly to prevent moisture from accumulating in the bearings. (See Form 50.20-NM3, Long Term Storage)
Installer has cleaned out interior.
Ensure
drain pan free from foreign material.
Ensure
air filters are clean, installed properly and secured. Use the directional arrows or other information on the filter to
determine the proper flow direction.
INSTALL CHECKLIST
Equipment received as ordered.
Unit checked for damage interior and exterior.
Make sure all ductwork is complete and available for full air flow.
Unit installed level to ensure proper drainage and operation.
Unit installed with proper clearances.
Ensure condensate water will drain toward the drain connection. An overflow drain may be required as a back up to a clogged
primary drain.
Check that coil(s), valves and piping have been leak checked and insulated as required.
Main coil drain pan must be properly trapped and charged with water before units are started.
Ensure that all air has been vented from the system.
Return valves to their proper operating positions prior to start-up.
Repair any solder joint leaks and gently tighten any leaking valve packing nuts and piping accessories as required.
Install all panels.
CLEANING CHECKLIST
CONTROLS CHECKLIST
Check that supply voltage matches nameplate data.
Ensure that the unit is properly grounded.
Controls installation complete
Check all electrical connections for tightness.
Review electrical print for correct wiring.