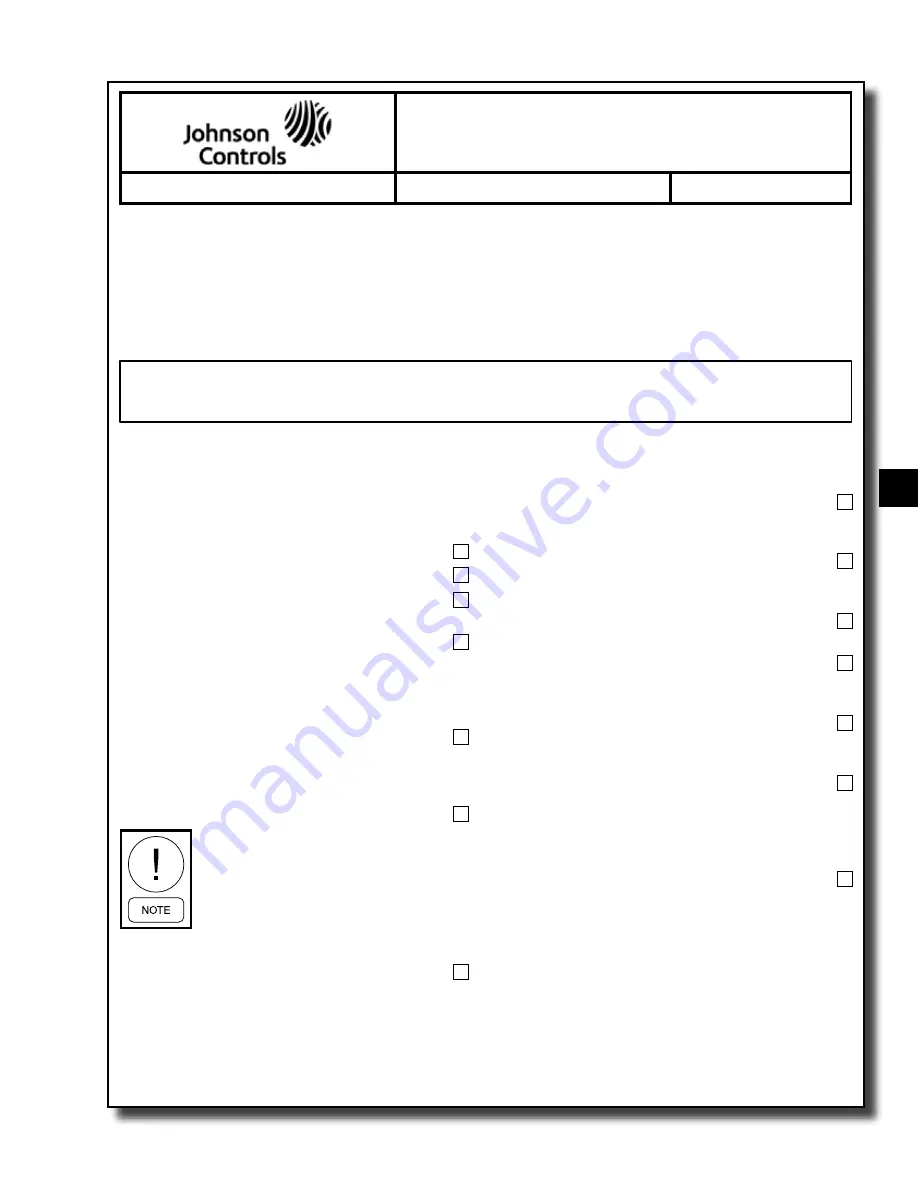
SECTION 6 – COMMISSIONING
FORM 201.26-NM1
ISSUE DATE: 1/19/2018
JOHNSON CONTROLS
111
6
JOHNSON CONTROLS
1
8. Visually inspect wiring (power and control). Wiring
MUST meet N.E.C. and local codes. .......................
9. Check tightness of power wiring inside the power
panel on both sides of the motor contactors and
overloads. ...............................................................
10. Check for proper size fuses in main and control cir-
cuits, and verify overload setting corresponds with
RLA and FLA values in electrical tables. ..................
11. Assure 120VAC Control Power to TB1 has 15 amp
minimum capacity. ...................................................
12. Be certain all water temp sensors are inserted com-
pletely in their respective wells and are coated with
heat conductive compound. ....................................
13. Assure that evaporator TXV bulbs are strapped
onto the suction lines at 4 or 8 o'clock positions or
suction temps. sensors if EEVs are installed. .........
B. COMPRESSOR HEATERS
(POWER ON - 24 HOURS PRIOR TO START)
Apply 120VAC and verify its value between terminals 5 and
2 of CTB2. The voltage should be /- 10%. ....
Power must be applied 24 hours prior to start-up
Each heater should draw approximately 0.5-1A.
A. CHECKING THE SYSTEM PRIOR TO INITIAL
START (NO POWER)
Unit Checks
1. Inspect the unit for shipping or installation damage
2. Assure that all piping has been completed .............
3. Visually check for refrigerant piping leaks ...............
4. Open suction line ball valve, discharge line ball
valve, and liquid line valve for each system. ...........
5. The compressor oil level should be main-
tained so that an oil level is visible or splash-
ing in sight glass when fully loaded. At shut-
down, the oil level should be between the
bottom and middle of the oil equalizing sight glass.
6. Assure water pumps are "ON". Check and adjust
water pump flow rate and pressure drop across
the cooler (see "Operational Limitations" in IOM).
Verify flow switch operation. ....................................
Excessive flow may cause catastrophic
damage to the heat exchanger (evapora-
tor).
7. Check the control panel to ensure it is free of for-
eign material (wires, metal chips, etc.). ....................
STARTUP CHECKLIST
YCWL0056 - 0198 STYLE A 60HZ,
YCWL0200 - 0611 STYLE A 50 HZ,
STARTUP CHECKLIST
Supersedes 201.26-CL1 (409)
Form 201.26-CL1 (313)
STARTUP CHECKLIST
The following work must be completed in accordance with installation instructions:
CUSTOMER: ____________________________________
ADDRESS: _____________________________________
PHONE: ________________________________________
JCI TEL NO: _____________________
JCI ORDER NO: __________________ JCI CONTRACT NO: ______________
JOB NAME: ____________________________________
LOCATION: ____________________________________
CUSTOMER ORDER NO: _________________________
CHILLER MODEL NO
: ____________________________
The work (as checked below) is in process and will be completed by: _____________ / ____________ /
___________
UNIT SERIAL NO
: _______________________________
Month
Day
Year
Summary of Contents for YCWL0056SE
Page 4: ...FORM 201 26 NM1 ISSUE DATE 1 19 2018 JOHNSON CONTROLS 4 THIS PAGE INTENTIONALLY LEFT BLANK...
Page 30: ...FORM 201 26 NM1 ISSUE DATE 1 19 2018 JOHNSON CONTROLS 30 THIS PAGE INTENTIONALLY LEFT BLANK...
Page 146: ...FORM 201 26 NM1 ISSUE DATE 1 19 2018 JOHNSON CONTROLS 146 THIS PAGE INTENTIONALLY LEFT BLANK...
Page 154: ...FORM 201 26 NM1 ISSUE DATE 1 19 2018 JOHNSON CONTROLS 154 THIS PAGE INTENTIONALLY LEFT BLANK...
Page 168: ...FORM 201 26 NM1 ISSUE DATE 1 19 2018 JOHNSON CONTROLS 168 THIS PAGE INTENTIONALLY LEFT BLANK...
Page 186: ...FORM 201 26 NM1 ISSUE DATE 1 19 2018 JOHNSON CONTROLS 186 NOTES...