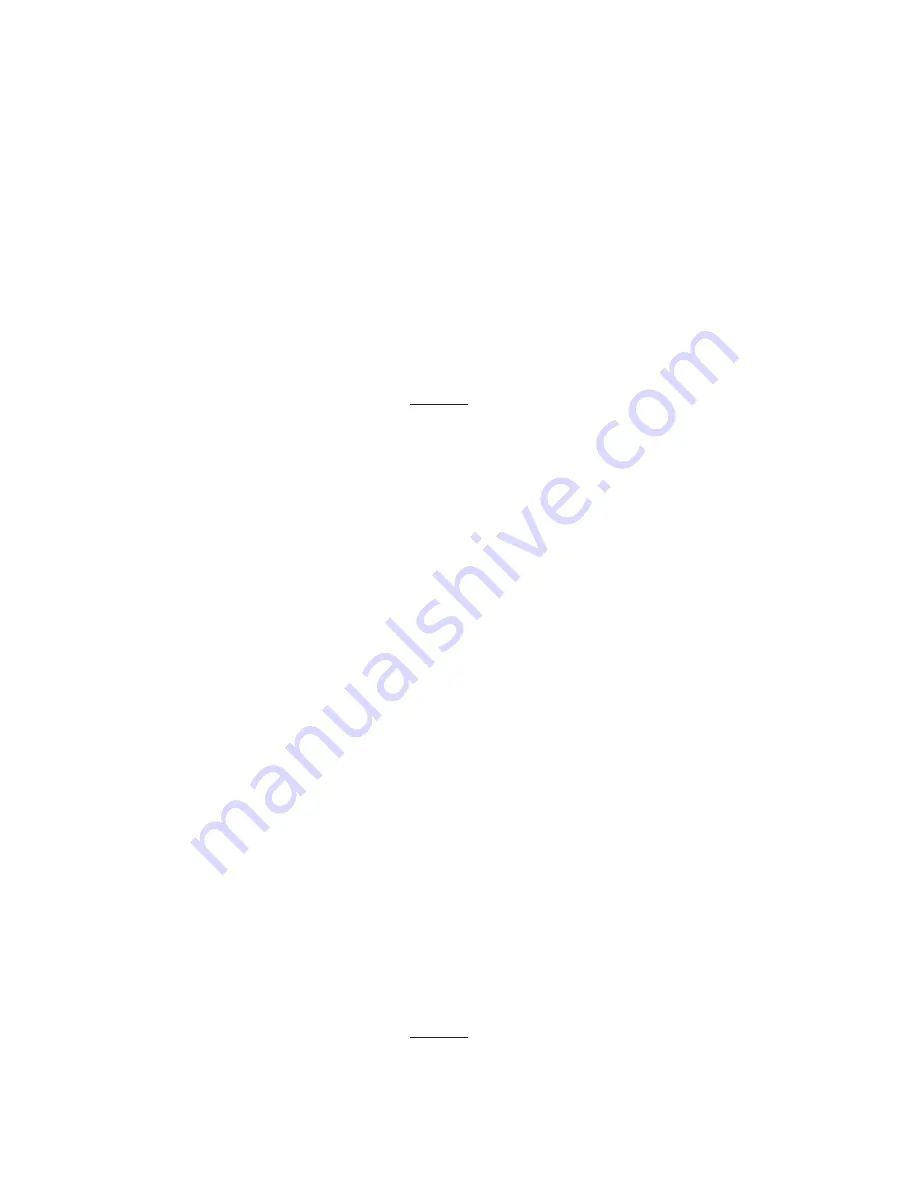
FORM 150.24-NM27
YORK INTERNATIONAL
89
OPERATING SEQUENCE UTILIZING RETURN WATER
CONTROL
NOTE: The Operating Sequence described below relates
to operation after power has been applied on a
hot water start such as start-up commissioning
or a hot water start at the beginning of the day. It
also assumes that 10 steps of loading are avail-
able and programmed. If less than 10 steps are
available, no chiller response will take place at
some of the operating points described.
1. For the system compressors to run, all Manual Re-
set Cut-outs must be reset, the Flow Switch must
be closed, the System Switches must be ON, the
Daily Schedule must be scheduling the chiller to
run, and temperature demand must be present.
2. As long as power is applied, the Crankcase Heat-
ers will be on and stay on as long as the compres-
sors are not running.
3. If power has just been applied to the system, the
microprocessor will start a 2 minute timer. This is
the same timer that prevents an instantaneous start
after a power failure. NOTE: Compressor Crankcase
Heaters should be on for a period of 24 hours prior
to commissioning. Failure to allow the heater suffi-
cient time to warm the oil may damage the com-
pressor due to liquid refrigerant in the oil.
4.
At the end of the 2 minute timer,
the micropro-
cessor will check for cooling demand as well as
check to see if any system safeties have been ex-
ceeded. If all conditions allow for start, the lead com-
pressor will start unloaded. Coincident with the start,
the programmable anti-recycle timer will be set and
the condensing temperature. (The temperature cor-
responding to the condensing pressure from refriger-
ant temperature/pressure chart).
The subcooling temperature should be taken by record-
ing the temperature of the liquid line at the outlet of the
condenser and recording the liquid line pressure at the
liquid stop valve with the system fully loaded after steady
state operation has been established and converting it
to a temperature from temperature/pressure chart. Be
sure to insulate the thermometer or thermocouple at-
tached to the piping.
Example:
LIQUID LINE PRESSURE
202 PSIG converted to
102°F
Minus Liquid Line Temperature
- 90°F
Subcooling =
12°F
Record: SYS 1 _______ SYS 2 _______
The proper refrigerant charge is attained when subcooling
is measured at 10 - 15°F. Add charge as needed to in-
crease subcooling and remove charge as necessary to
reduce subcooling. Whenever removing charge, be sure
to recover it into an approved container.
After the subcooling is set at 10-15°F by adding or re-
moving charge and steady state fully loaded operation is
established, system superheat should also be adjusted
for 10-15°F. A factory recomended superheat setting of
15°F is appropriate for systems that operate over a vari-
ety of ambient temperatures, chilled liquid temperatures,
and loading conditions. It also compensates for gauge
and temperature sensor inaccuracy. When measuring
superheat, be sure to insulate a thermometer or thermo-
couple attached to the piping to assure a true tempera-
ture is measured.
The superheat is the difference between the actual tem-
perature of the returned refrigerant gas entering the com-
pressor and the temperature corresponding to the suc-
tion pressure as shown in a standard pressure/tem-
perature chart. The suction temperature should be taken
6" before the compressor service valve, and the suction
pressure is taken at the compressor suction service valve.
Example:
Suction Temperature
46°F
Minus Suction Pressure 56 PSIG
Converted to Temperature
- 31°F
Superheat =
15°F
Superheat SYS 1 _______ SYS 2 _______
Normally, the thermal expansion valve need not be ad-
justed in the field. If, however, an adjustment is to be
made, the expansion valve adjusting screw should be
turned not more than one turn at a time, allowing suffi-
cient time (approximately 15 minutes) between ad-
justments for the system and the thermal expansion valve
to respond and return to settled operation.
Proper subcooling and superheat will assure optimum
performance and reliability of the system. Checks should
always be made when commissioning a chiller and on a
yearly basis.
If the unit has been functioning satisfactorily during the
initial operating period, it is ready for continuous opera-
tion.
*
Leak check compressors, fittings, and piping to
assure no leaks are present from improper han-
dling.
Summary of Contents for YCWJ45EE0
Page 29: ...FORM 150 24 NM27 YORK INTERNATIONAL 29 CONTROL CIRCUIT With I O Expansion Board LD02106...
Page 30: ...30 YORK INTERNATIONAL FIG 9 SYSTEM WIRING...
Page 31: ...FORM 150 24 NM27 YORK INTERNATIONAL 31 LD02678...
Page 35: ...FORM 150 24 NM27 YORK INTERNATIONAL 35 LD02679...
Page 36: ...36 YORK INTERNATIONAL MICROPANEL CONNECTION DIAGRAM With I O Expansion Board LD02107...
Page 37: ...FORM 150 24 NM27 YORK INTERNATIONAL 37 LD02108...