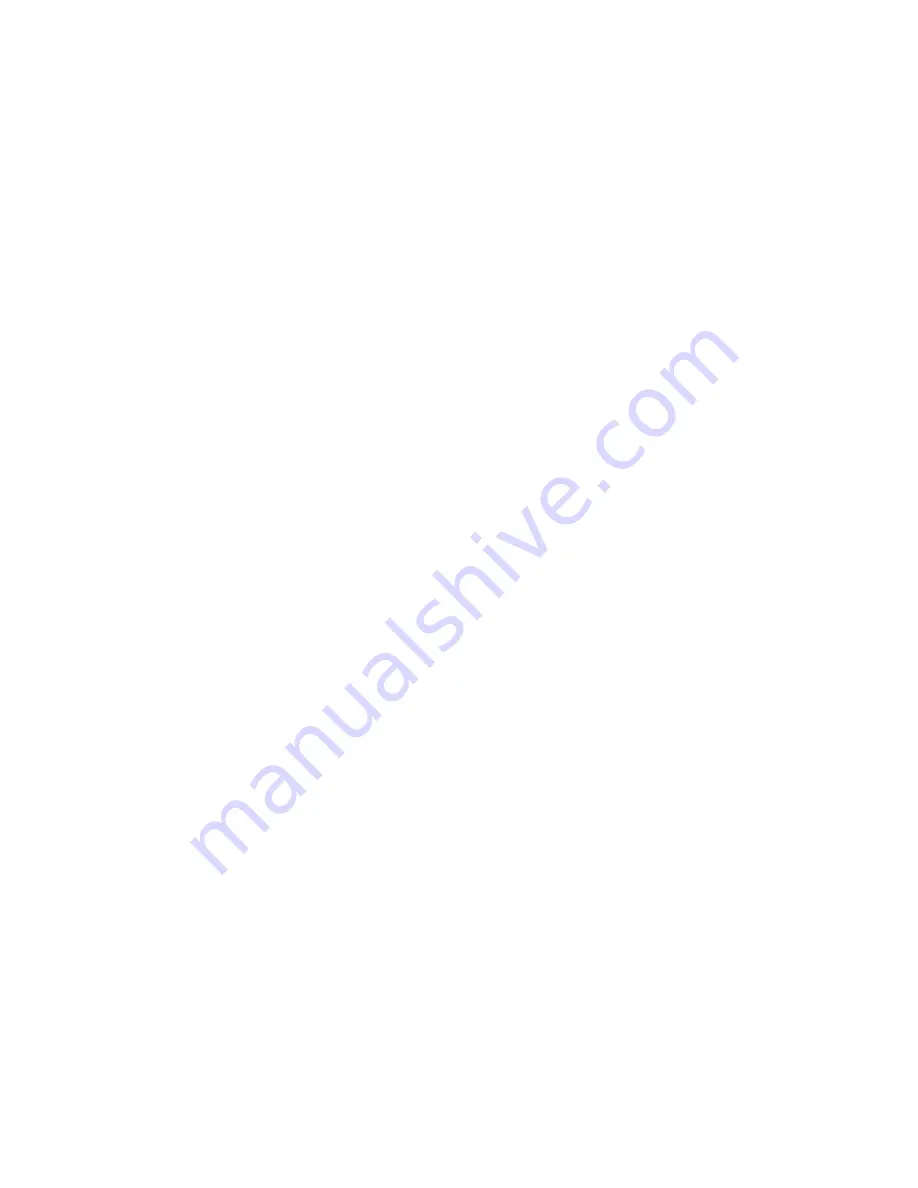
88
YORK INTERNATIONAL
sure no refrigerant is in the oil at start-up!
*
4. Program the Dip Switches on the Microproces-
sor Board (Page 43) and verify the selection by
pressing the OPTIONS key.
Switch 3 should always be closed.
Switch 6 should always be open.
NOTE: It is IMPORTANT that all switches are properly
programmed. Otherwise, undesirable operation
will result.
*
5. Press the PROGRAM key and program each of
the 11 limits and record them.
They are as follows:
*
Discharge Cut-out _________________ PSIG
*
Outside Air Temp Low Cut-out _________ °F
*
Outside Air Temp High Cut-out _________ °F
*
Discharge Pressure
Unload Pressure __________________ PSIG
*
Suction Pressure
Unload Pressure __________________ PSIG
*
Leaving Water Temp Cut-out ___________ °F
*
Suction Pressure Cut-out ___________ PSIG
*
Rate Control Temp __________________ °F
*
Anti Recycle Time _________________ SEC
*
Rate Sensitivity __________________ °F/MIN
*
Number of Load Steps _________________
See page 44 for assistance in programming these
values.
*
6. Program the date and time by first assuring that
the CLK jumper J18 on the Microprocessor Board
(Fig. 28) is in the ON position (Top 2 pins).
Press the SET TIME key and set the date and
time (Page 55).
*
7. Program the Daily and Holiday Start/Stop
Schedule by pressing the SET SCHEDULE/
HOLIDAY key (Page 56).
*
8. Program the Chilled Liquid Setpoint and Control
Range by pressing the CHILLED LIQUID TEMP/
RANGE key (Page 58).
*
9. If the Remote Reset is to be used, the maxi-
mum reset must be programmed. This can be
programmed by pressing the REMOTE RESET
TEMP RANGE key (Page 84).
INITIAL START-UP
After the operator has become thoroughly familiar with
the control panel and has performed the preceeding
checks 24 hours prior to start-up, the unit can be put
into operation.
*
Place the System Switches to the ON position. See
the OPERATING SEQUENCE for unit operation.
*
The compressor will start and a flow of liquid should
be noted in the liquid indicator. After several min-
utes of operation, the bubbles will disappear and
there will be a solid column of liquid when the unit is
operating normally. On start-up, foaming of the oil
may be evident in the compressor oil sight glass.
After the water temperature has been pulled down to
operating conditions, the oil should be clear. Normal
operation of the unit is evidenced by a hot discharge
line (discharge superheat should not drop below
50°F) clear oil in the compressor crankcase, solid
liquid refrigerant in the liquid indicator and usually
no more than 2 PSIG variation in suction pressure
for any given set of operating conditions.
*
Allow the compressor to run for a short time, being
ready to stop it immediately if any unusual noise or
other adverse condition should develop. When start-
ing the compressor, always make sure the oil pump
is functioning properly. Compressor oil pressure must
be as described in the SYSTEM SAFETIES Sec-
tion, page 69.
*
Check the system operating parameters. Do this by
selecting various readouts such as pressures and
temperatures. Compare these to test gauge read-
ings.
CHECKING SUPERHEAT AND SUBCOOLING
The subcooling should always be checked when charg-
ing the system with refrigerant and/or before setting the
superheat.
When the refrigerant charge is correct, there will be no
bubbles in the liquid sightglass with the system operat-
ing under full load conditions, and there will be 10°F to
15°F subcooled liquid refrigerant leaving the condenser.
An overcharged system should be guarded against. Evi-
dences of overcharge are as follows:
a. If a system is overcharged, the discharge pressure
will be higher than normal. (Normal discharge/
condensing pressure can be found in refrigerant
temperature/pressure chart; use entering air tempera-
ture +30°F for normal condensing temperatures.)
b. The temperature of the liquid refrigerant out of the
condenser should not be more than 15°F less than
Summary of Contents for YCWJ45EE0
Page 29: ...FORM 150 24 NM27 YORK INTERNATIONAL 29 CONTROL CIRCUIT With I O Expansion Board LD02106...
Page 30: ...30 YORK INTERNATIONAL FIG 9 SYSTEM WIRING...
Page 31: ...FORM 150 24 NM27 YORK INTERNATIONAL 31 LD02678...
Page 35: ...FORM 150 24 NM27 YORK INTERNATIONAL 35 LD02679...
Page 36: ...36 YORK INTERNATIONAL MICROPANEL CONNECTION DIAGRAM With I O Expansion Board LD02107...
Page 37: ...FORM 150 24 NM27 YORK INTERNATIONAL 37 LD02108...