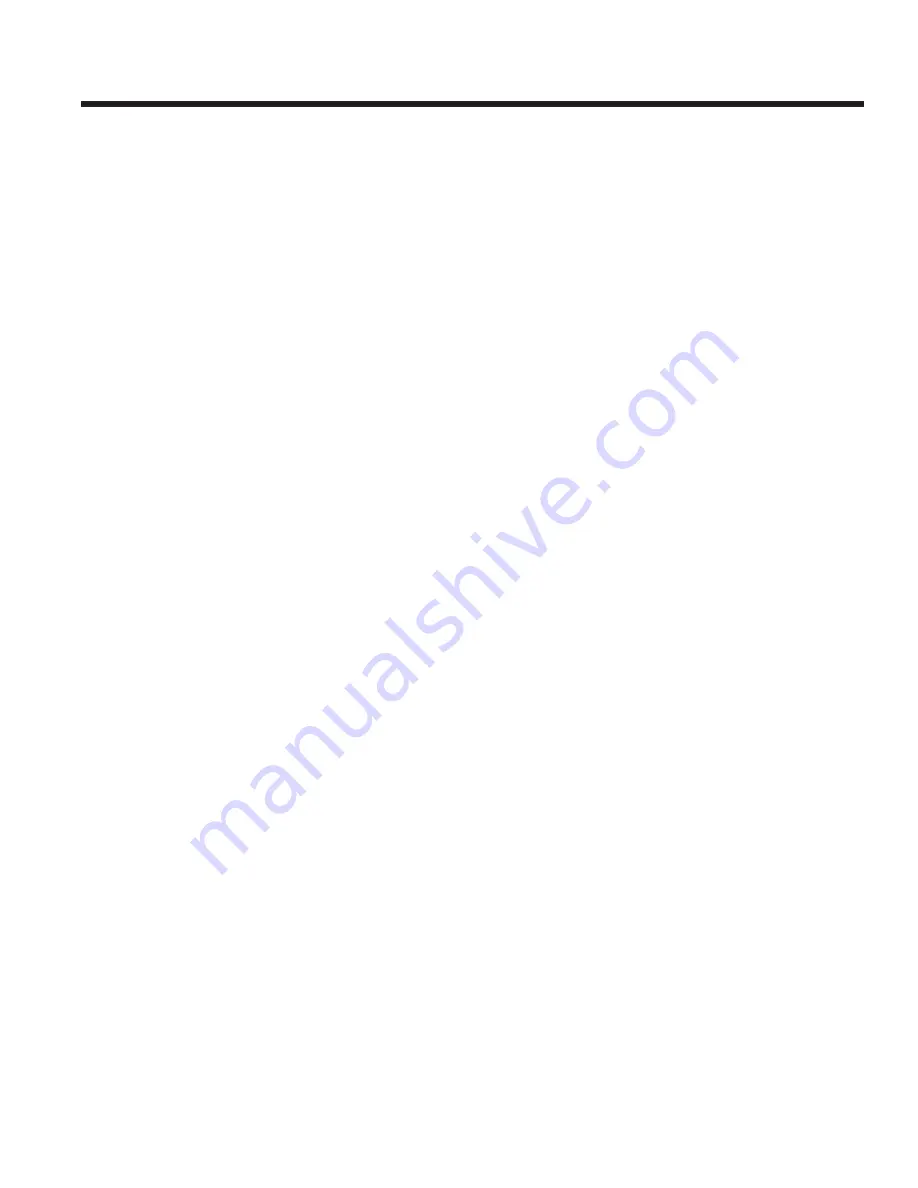
JOHNSON CONTROLS
FORM 201.23-EG1 (1013)
113
unit panels. Heavy gauge, welded wire-mesh,
coated to resist corrosion, around base of ma
-
chine to restrict unauthorized access.
E. Evaporator options:
1. Provide 1-1/2” (38mm) cooler insulation in lieu
of standard 3/4” (19mm).
2. Provide Raised Face Flanges for cooler nozzles:
a. 150 psig (10.3 barg), welded flanges (field kit,
matching pipe flange by contractor).
b. 150 psig (10.3 barg) companion flanges. (not
available with 460V units)
c. 150 psig (10.3 barg), ANSI/AWWA C-606
couplings (field kit, matching pipe flange by
contractor).
F. Flow Switch (
Field Mounted
): Vapor proof SPDT,
NEMA 3R switch [ ___150 psig (10.3 barg) or ___300
psig (20.7 barg)], -20°F to 250°F (-28.9°C to 121.1°C).
G. Building Automation System Interface:
1. Chiller to accept 4 to 20mA or 0 to 10 VDC input
to reset the leaving chilled liquid temperature.
(
Factory Mounted
)
H. Multi-Unit Sequence Control (
Field Mounted
): Sepa-
rate Sequencing control center provided to permit
control of up to eight chillers in parallel based on mixed
liquid temperature.
I. Vibration Isolation (
Field Mounted
):
1. Elastomeric Isolators.
2. 1 Inch Deflection Spring Isolators: Level adjust
-
able, spring and cage type isolators for mounting
under the unit base rails.
3. 2" Deflection Seismic Isolators: Level adjust
-
able, restrained mounts in rugged welded steel
housing with vertical and horizontal limit stops.
Housings shall be designed to withstand a mini
-
mum 1.0g accelerated force in all directions to
2” (50.8 mm).
J. Service Shut-Off Valve: Provide suction service shut-off
valve for each compressor. (
Factory Mounted
)
PART 3 — EXECUTION
3.01 INSTALLATION
A. General: Rig and Install in full accordance with
Manufacturer’s requirements, Project drawings, and
Contract documents.
B. Location: Locate chiller as indicated on drawings, in
-
cluding cleaning and service maintenance clearance
per Manufacturer instructions. Adjust and level chiller
on support structure.
C. Components: Installing Contractor shall provide and
install all auxiliary devices and accessories for fully
operational chiller.
D. Electrical: Coordinate electrical requirements and con-
nections for all power feeds with Electrical Contractor
(Division 16).
E. Controls: Coordinate all control requirements and
connections with Controls Contractor.
F. Finish: Installing Contractor shall paint damaged and
abraded factory finish with touch-up paint matching
factory finish.
Summary of Contents for YCIV0157E/V
Page 57: ...JOHNSON CONTROLS FORM 201 23 EG1 1013 57...
Page 59: ...JOHNSON CONTROLS FORM 201 23 EG1 1013 59...
Page 61: ...JOHNSON CONTROLS FORM 201 23 EG1 1013 61...
Page 63: ...JOHNSON CONTROLS FORM 201 23 EG1 1013 63...
Page 65: ...JOHNSON CONTROLS FORM 201 23 EG1 1013 65...
Page 67: ...JOHNSON CONTROLS FORM 201 23 EG1 1013 67...
Page 69: ...JOHNSON CONTROLS FORM 201 23 EG1 1013 69...
Page 71: ...JOHNSON CONTROLS FORM 201 23 EG1 1013 71...
Page 73: ...JOHNSON CONTROLS FORM 201 23 EG1 1013 73...
Page 75: ...JOHNSON CONTROLS FORM 201 23 EG1 1013 75...
Page 77: ...JOHNSON CONTROLS FORM 201 23 EG1 1013 77...
Page 89: ...JOHNSON CONTROLS FORM 201 23 EG1 1013 89 INTENTIONALLY LEFT BLANK...
Page 102: ...JOHNSON CONTROLS 102 FORM 201 23 EG1 1013 Typical Control Wiring Two Compressor...
Page 104: ...JOHNSON CONTROLS 104 FORM 201 23 EG1 1013 Typical Control Wiring Three Compressor...
Page 106: ...JOHNSON CONTROLS 106 FORM 201 23 EG1 1013 Typical Control Wiring Four Compressor...
Page 107: ...JOHNSON CONTROLS FORM 201 23 EG1 1013 107...
Page 114: ...Form 201 23 EG1 1013 Supersedes 201 23 EG1 713...