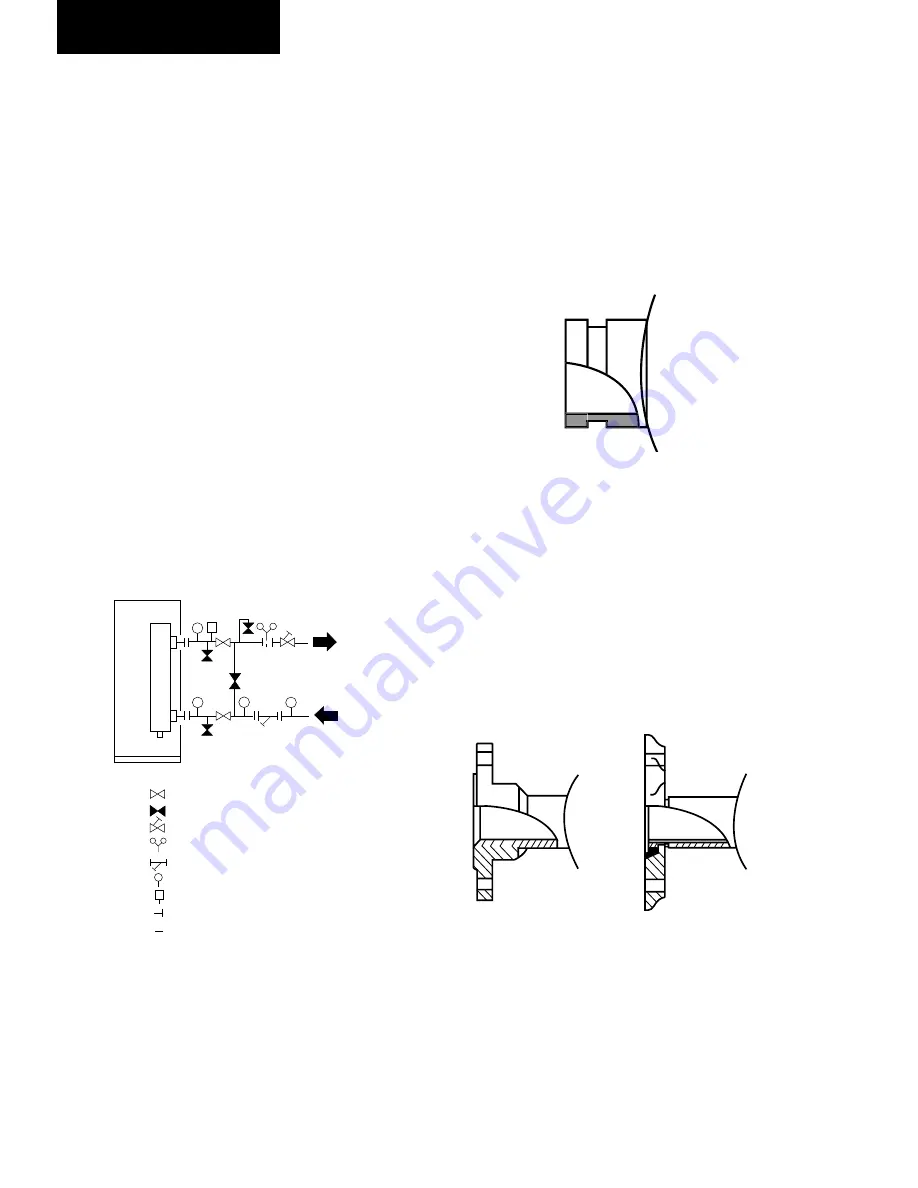
32
JOHNSON CONTROLS
FORM 201.21-NM1 (1223)
INSTALLATION
WATER TREATMENT
The unit performance provided in the Design Guide
is based on a fouling factor of 0.0001 ft
2
hr°F/Btu
(0.018m2/hr °C/kW). Dirt, scale, grease and certain
types of water treatment will adversely affect the heat
exchanger surfaces and therefore the unit performance.
Foreign matter in the water system(s) can increase the
heat exchanger pressure drop, reducing the flow rate and
causing potential damage to the heat exchanger tubes.
Aerated, brackish or salt water is not recommended
for use in the water system(s). YORK recommends
that a water treatment specialist should be consulted
to determine whether the proposed water composition
will adversely affect the evaporator materials of carbon
steel and copper. The pH value of the water flowing
through the evaporator must be kept in a range between
7 and 8.5.
PIPEWORK ARRANGEMENT
The following is a suggested piping arrangement for
single unit installations. For multiple unit installations,
each unit should be piped as shown in FIG. 3.
-Isolating Valve - Normally Open
-Isolating Valve - Normally Closed
-Flow Regulating Valve
-Flow Measurement Device
-Strainer
-Pressure Tapping
-Flow Switch
-Flanged Connection
-Pipework
FIG. 3 - PIPEWORK ARRANGEMENT
CONNECTION TYPES & SIZES
For connection sizes relevant to individual models refer
to the Technical Data Section.
COOLER CONNECTIONS
Standard chilled liquid connections on all coolers are of
the Victaulic Groove type (See FIG. 4).
FIG. 4 - VICTAULIC GROOVE
LD10494
Option Flanges
One of two types of flanges may be fitted depending
on the customer or local Pressure Vessel Code require-
ments. These are Victaulic-Adapter flanges, normally
supplied loose, or weld flanges, which may be supplied
loose or ready-fitted. Victaulic-Adapter and weld flange
dimensions are to ISO 7005 - NP10.
FIG. 5 - FLANGE ATTACHMENT
LD10495
WELD FLANGE
VICTAULIC ADAPTER
LD10507
Summary of Contents for YCAV0157
Page 43: ...43 JOHNSON CONTROLS FORM 201 21 NM1 1223 This page intentionally left blank 6...
Page 55: ...55 JOHNSON CONTROLS FORM 201 21 NM1 1223 This page intentionally left blank 6...
Page 57: ...57 JOHNSON CONTROLS FORM 201 21 NM1 1223 ELEMENTARY CONTROL WIRING DIAGRAM CON T 6 LD12519...
Page 64: ...64 JOHNSON CONTROLS FORM 201 21 NM1 1223 LOCATION LABEL LD10519 TECHNICAL DATA...
Page 65: ...65 JOHNSON CONTROLS FORM 201 21 NM1 1223 This page intentionally left blank 6...
Page 123: ...123 JOHNSON CONTROLS FORM 201 21 NM1 1223 This page intentionally left blank 6...
Page 211: ...211 JOHNSON CONTROLS FORM 201 21 NM1 1223 8 This Page Intentionally Left Blank...
Page 233: ...233 JOHNSON CONTROLS FORM 201 21 NM1 1223 This page intentionally left blank 8...
Page 253: ...253 JOHNSON CONTROLS FORM 201 21 NM1 1223 8 This page intentionally left blank...
Page 281: ...281 JOHNSON CONTROLS FORM 201 21 NM1 1223 8 This page intentionally left blank...