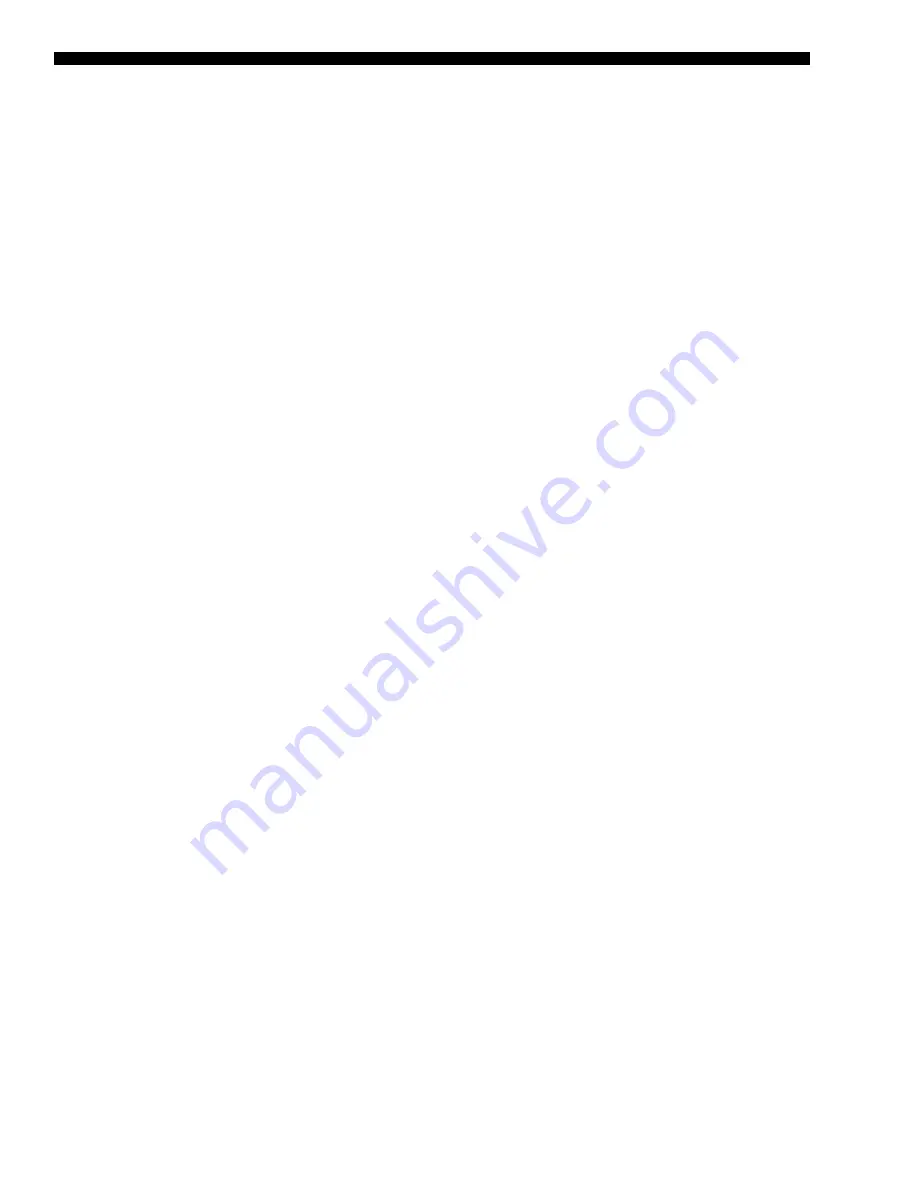
JOHNSON CONTROLS
FORM 150.67-EG1 (219)
98
2.03 REFRIGERANT CIRCUIT COMPONENTS
Each refrigerant circuit shall include liquid line shutoff valve with charging port, low side
pressure relief device, filter-drier, solenoid valve, sight glass with moisture indicator, ex-
pansion valves, and flexible, closed-cell foam insulated suction line. Unit also includes
service isolation valves as standard.
2.04 HEAT EXCHANGERS
C. Evaporator:
1. Evaporator shall be brazed-plate stainless steel construction, single or dual circuit
heat exchangers capable of refrigerant working pressure of 650 psig (3103 kPa)
and liquid side pressure of 150 psig (1034 kPa) (Option for 300 psig [2068 kPa]
available.)
2.
Evaporator shall be covered in 3/4" (19mm) flexible, closed cell insulation, thermal
conductivity of 0.26k (BTU/HR-FT
2
-
°
F]/in.) maximum.
3. Cooler shall have thermostatically controlled heaters to protect to -20°F (29°C) am-
bient in off-cycle.
4. Brazed plate heat exchangers shall be UL listed.
5. Installing contractor must include accommodations in the chilled water piping to
allow proper drainage and venting of the heat exchanger. A strainer with a mesh
size between 0.5 and 1.5mm (40 mesh) is recommended upstream of the heat ex-
changer to prevent clogging.
D. Air Cooled Condenser:
1. Coils: Internally enhanced, seamless copper tubes, mechanically expanded into
aluminum alloy fins with full height collars. Subcooling coil an integral part of con
-
denser. Design working pressure shall be 650 PSIG (45 barg).
2. Low Noise Fans: Shall be dynamically and statically balanced, direct drive, propel-
ler type fan, providing vertical air discharge and low sound. Each fan in its own
compartment to prevent crossflow during fan cycling. Guards of heavy gauge, PVC
(polyvinyl chloride) coated or galvanized steel.
3.
Fan Motors: High efficiency, direct drive, 6 pole, 3 phase, insulation class “F”, cur
-
rent protected, Totally Enclosed Air-Over (TEAO), rigid mounted, with double sealed,
permanently lubricated, ball bearings.
2.05 CONTROLS
E. General: Automatic start, stop, operating, and protection sequences across the range
of scheduled conditions and transients.
F. Microprocessor Enclosure: Rain and dust tight NEMA 3R/12 powder painted steel cab-
inet with a gasket sealed protective cover.
G. Microprocessor Control Center:
1. Automatic control of compressor start/stop, anti-coincidence and anti-recycle tim-
ers, automatic pump-down on shutdown, condenser fans, evaporator pump, evapo-
rator heater, unit alarm contacts, and chiller operation from 0°F to 125°F (-18°C to
52°C) ambient. Automatic reset to normal chiller operation after power failure.
Guide Specifications (Cont'd)
Summary of Contents for YCAL Series
Page 4: ...JOHNSON CONTROLS FORM 150 67 EG1 219 4 THIS PAGE INTENTIONALLY LEFT BLANK...
Page 47: ...FORM 150 67 EG1 219 JOHNSON CONTROLS 47 Unit Dimensions Cont d YCAL0028 LD18674...
Page 55: ...FORM 150 67 EG1 219 JOHNSON CONTROLS 55 45 1 8 18 1 2 LD18682 Unit Dimensions Cont d YCAL0052...
Page 57: ...FORM 150 67 EG1 219 JOHNSON CONTROLS 57 Unit Dimensions Cont d YCAL0056 45 1 8 16 3 4 LD18684...
Page 63: ...FORM 150 67 EG1 219 JOHNSON CONTROLS 63 Unit Dimensions Cont d YCAL0022 SI LD18692...
Page 73: ...FORM 150 67 EG1 219 JOHNSON CONTROLS 73 Unit Dimensions Cont d YCAL0052 SI 424 LD18702...
Page 88: ...JOHNSON CONTROLS FORM 150 67 EG1 219 88 Power Wiring Single Circuit ld18707...
Page 89: ...FORM 150 67 EG1 219 JOHNSON CONTROLS 89 Power Wiring Single Circuit Cont d...
Page 90: ...JOHNSON CONTROLS FORM 150 67 EG1 219 90 Power Wiring Single Circuit Cont d...
Page 91: ...FORM 150 67 EG1 219 JOHNSON CONTROLS 91 LD18746 Power Wiring Dual Circuit...