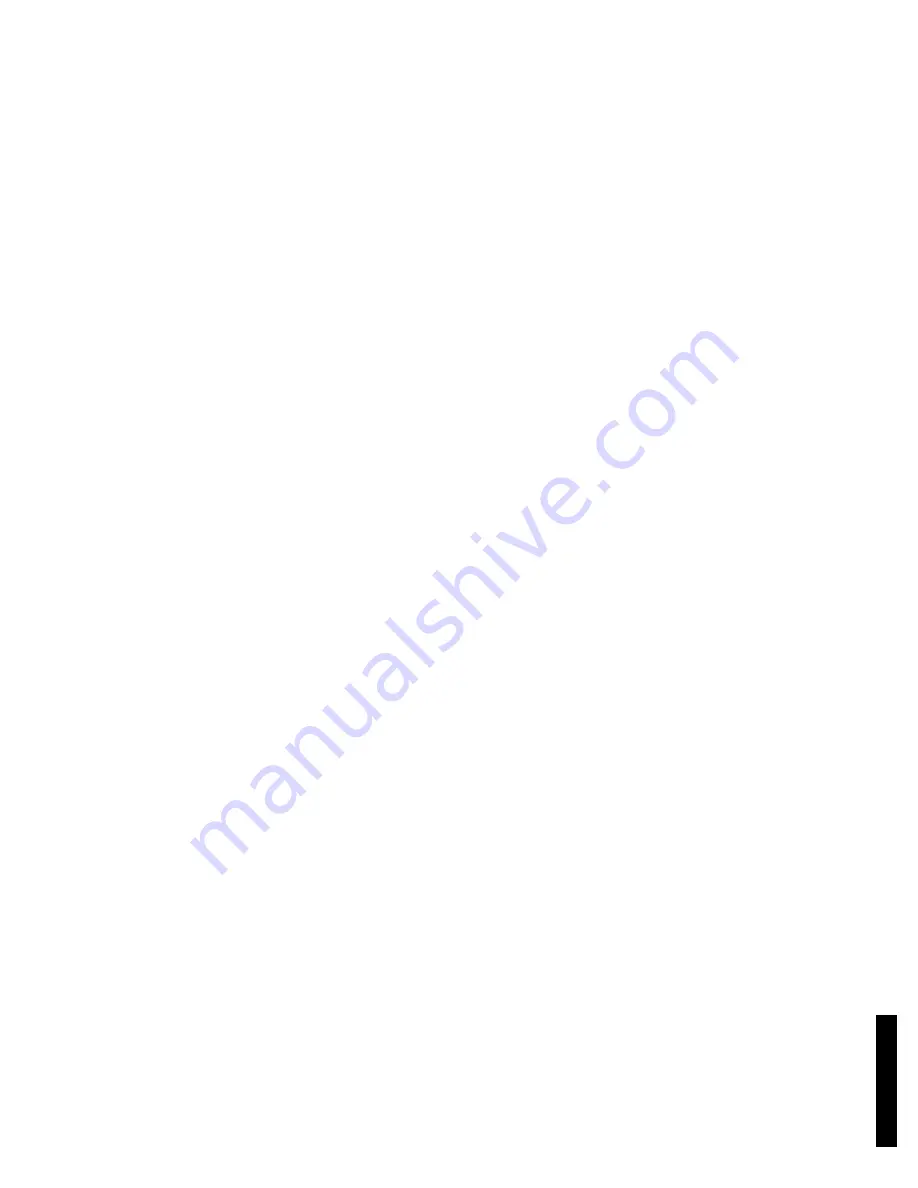
YORK INTERNATIONAL
71
FORM 160.60-O1
SECTION 8
PREVENTIVE MAINTENANCE
It is the responsibility of the owner to provide the neces-
sary daily, monthly and yearly maintenance requirements
of the system.
IMPORTANT
: If a unit failure occurs due
to improper maintenance during the warranty period;
YORK will not be liable for costs incurred to return the
system to satisfactory operation. In any operating sys-
tem it is most important to provide a planned mainte-
nance and inspection of its functioning parts to keep it
operating at its peak efficiency. Therefore, the following
maintenance should be performed when prescribed.
COMPRESSOR
1.
Oil Filter
The oil filter must be changed when the
oil pressure drops 30% or semi-annually if not required
earlier.
When the oil filter is changed it should be inspected
thoroughly for any aluminum particles which would
indicate possible bearing wear. If aluminum particles
are found this should be brought to the attention of
the nearest YORK office for their further investigation
and recommendations.
2.
Oil Charging
The oil in the compressor must be
charged annually or earlier if it becomes dark or cloudy.
PRESSURE TESTING
The unit should be pressure tested annually. Any leaks
found must be repaired immediately. Air and moisture
are the worst enemies of these systems and experience
has shown that units which are maintained tight, are sys-
tems that provide trouble-free efficient operation.
COOLER AND CONDENSER
The major portion of maintenance on the condenser and
cooler will deal with the maintaining the water side of the
condenser and cooler in a clean condition.
The use of untreated water in cooling towers, closed wa-
ter systems, etc. frequently results in one or more of the
following:
1. Scale Formation
2. Corrosion or Rusting
3. Slime and Algae Formation
It is therefore to the benefit of the user to provide for proper
water treatment to provide for a longer and more eco-
nomical life of the equipment. The following recommen-
dation should be followed in determining the condition of
the water side of the condenser and cooler tubes.
1. The condenser tubes should be cleaned annually or
earlier if conditions warrant. If the temperature differ-
ence between the water off the condenser and the
condenser saturation temperature is more than 4°
greater than the difference recorded on a new unit it is
a good indication that the condenser tubes require
cleaning. They should be cleaned as instructed on
page 69 of this manual.
2. The cooler tubes under normal circumstances will not
require cleaning. If however the temperature difference
between the refrigerant and the chilled water increases
slowly over the operating season, it is an indication
that the cooler tubes may be fouling or that there may
be a water by-pass in the water box requiring gasket
replacement or refrigerant may have leaked from the
chiller.
OIL RETURN SYSTEM
1. Change the dehydrator in the oil return system semi-
annually or earlier if the system fails to operate.
2. When the dehydrator is changed the nozzle of the
eductor should be checked for any foreign particles
that may be obstructing the jet.
ELECTRICAL CONTROLS
1. All electrical controls should be inspected for obvious
malfunctions.
2. It is important that the factory settings of controls
(operation and safety) not be changed. If the settings
are changed without YORKs approval the warranty
will be jeopardized.
3. A 5-11 year life battery is part of the RTC-Real Time
Clock. To replace, refer to Fig. 16.
S
E
C
T
8