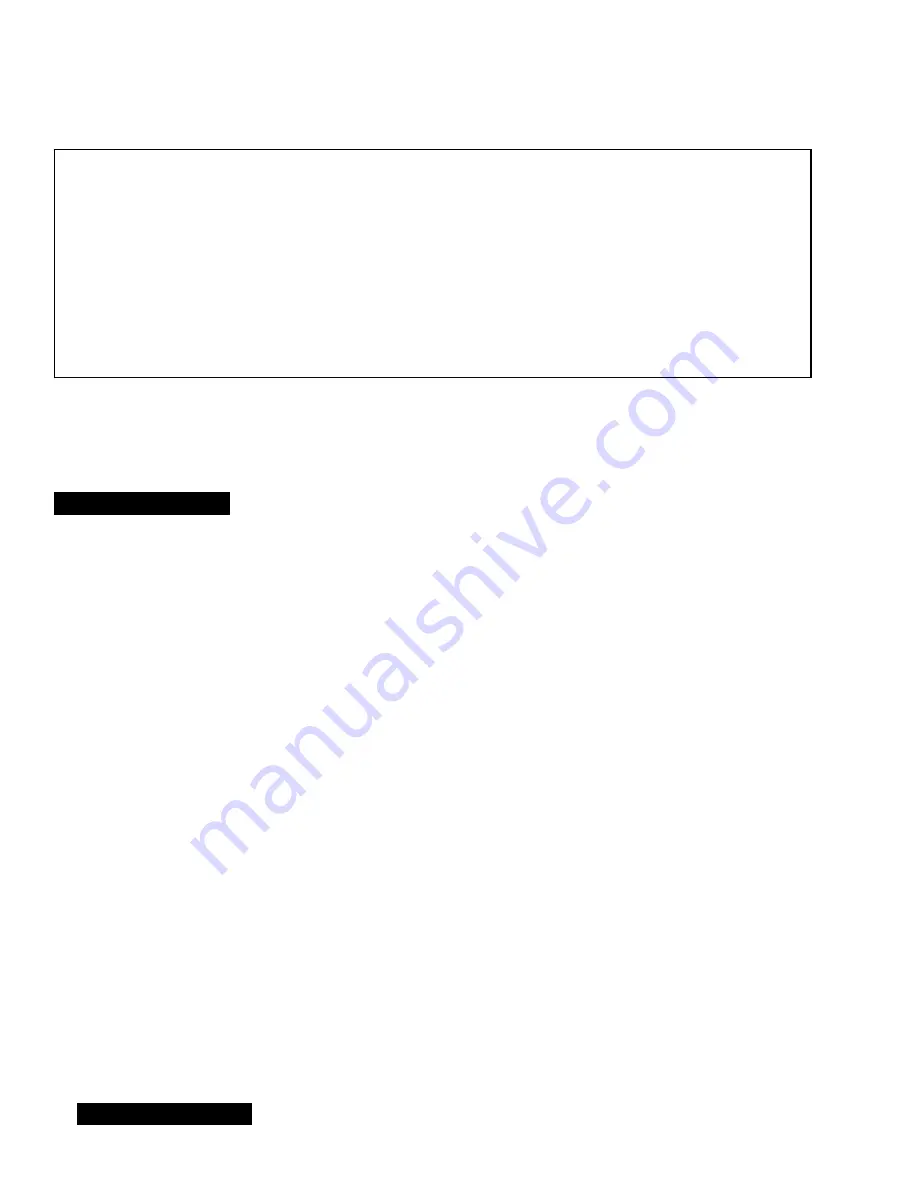
48
YORK INTERNATIONAL
START-UP PROCEDURE (Also see page 50)
Pre-Starting
Prior to starting the chiller, observe the MicroComputer
Control Center. Make sure the display reads:
SYSTEM READY TO START
To pre-start the chiller use the following procedure:
1.
OIL HEATER
The oil heater
must
be energized for
12 hours prior to starting the unit. The unit will not
start if the oil is less than 71°F or less than con-
denser saturation temp +40°F. If not possible, the
compressor oil should be drained and new oil must
be charged into the oil sump. (See Oil Charging Pro-
cedure, page 61.)
2.
OIL PUMP
To check, press and release the
MANUAL OIL PUMP
key under
SERVICE
on the
control center. The oil pump will run for 10 minutes
and shut down. Press and release the
MANUAL OIL
PUMP
key to stop the operation of the oil pump for
less than 10 minutes of operation.
3.
PREROTATION VANES
Make sure the control cen-
ter is in the
SERVICE
mode, and vane/speed toggle
START-UP is set for
VANE
then press the prerotation
vanes
OPEN/INCR
and
CLOSE/INCR
keys to ob-
serve the operation of the prerotation vanes. The con-
trol center supplies a signal to operate the prerotation
vanes. The movement of the vanes will be displayed
on the control center. The display readout is active
whenever power is supplied to the control center. Re-
turn from the
SERVICE
mode to
LOCAL
,
PRO-
GRAM
, or
REMOTE
mode to suit the method of
operation selected for the chiller application. Refer to
Section 2.
4.
% ENGINE LOAD LIMIT
Press the
% ENGINE
LOAD LIMIT
setpoint key on the Control Center. The
display should read:
ENGINE LOAD LIMIT = 100%
If the setpoint is not 100% and was predetermined for
the job application, the Control Center should be pro-
grammed to that specification. To program, refer to
Section 2.
5. All Control Center setpoints should be programmed
before the chiller is started. (Refer to Section 2). Prior
to start, the clock must be programmed for the proper
day and time. Any setpoints which are desired to be
changed may be programmed. If not programmed the
default value setpoints are as follows:
LCWT = 45°F
% Engine Load Limit = 100%
Pulldown Demand = None
Clock = Sun 12:00 A.M.
Daily Schedule = None
Holiday= None
Remote Reset Temp. Range = 20°F
Data Logger = No Operation
Start-Up
1. Turn on the 460 volt supply power via the AC power
starter panel located on the drive line package. Verify
that DC supply for engine is 24VDC.
2. Check engine control switch in engine panel, it should
be set to
AUTO
.
3. If the chiller water pump is manually operated, start
the pump. The control center will not allow the unit to
start unless chilled liquid flow is established through
the unit. (A field supplied chilled water flow switch is
required.) If the chilled liquid pump is wired to the
MicroComputer Control Center, the pump will auto-
matically start; therefore, this step is not necessary.
4. To start the unit, press the
COMPRESSOR START
switch. This switch will automatically spring return to
the
RUN
position. (If the unit was previously started,
press the
STOP/RESET
side of the
COMPRESSOR
switch and then press the
START
side of the switch
SECTION 3
SYSTEM OPERATING PROCEDURES
OIL HEATERS
If the oil heater is de-energized during a shutdown pe-
riod, they must be energized for 12 hours prior to start-
ing compressor, or remove all oil and recharge com-
pressor with new oil. (See Oil Charging Procedure,
page 61.)
NOTE: The oil heater is thermostatically controlled
and remains energized as long as the fused
disconnect switch to the starter is energized.
CHECKING THE OIL LEVEL IN THE OIL
RESERVOIR
Proper operating oil level the middle of the upper
sight glass.
If the oil level is excessively high after start-up, the
excess oil may be drained from the oil filter drain valve
while the compressor is running.
If oil level is low, oil should be added to the compres-
sor. (See Oil Charging Procedure, page 61.)
WARNING