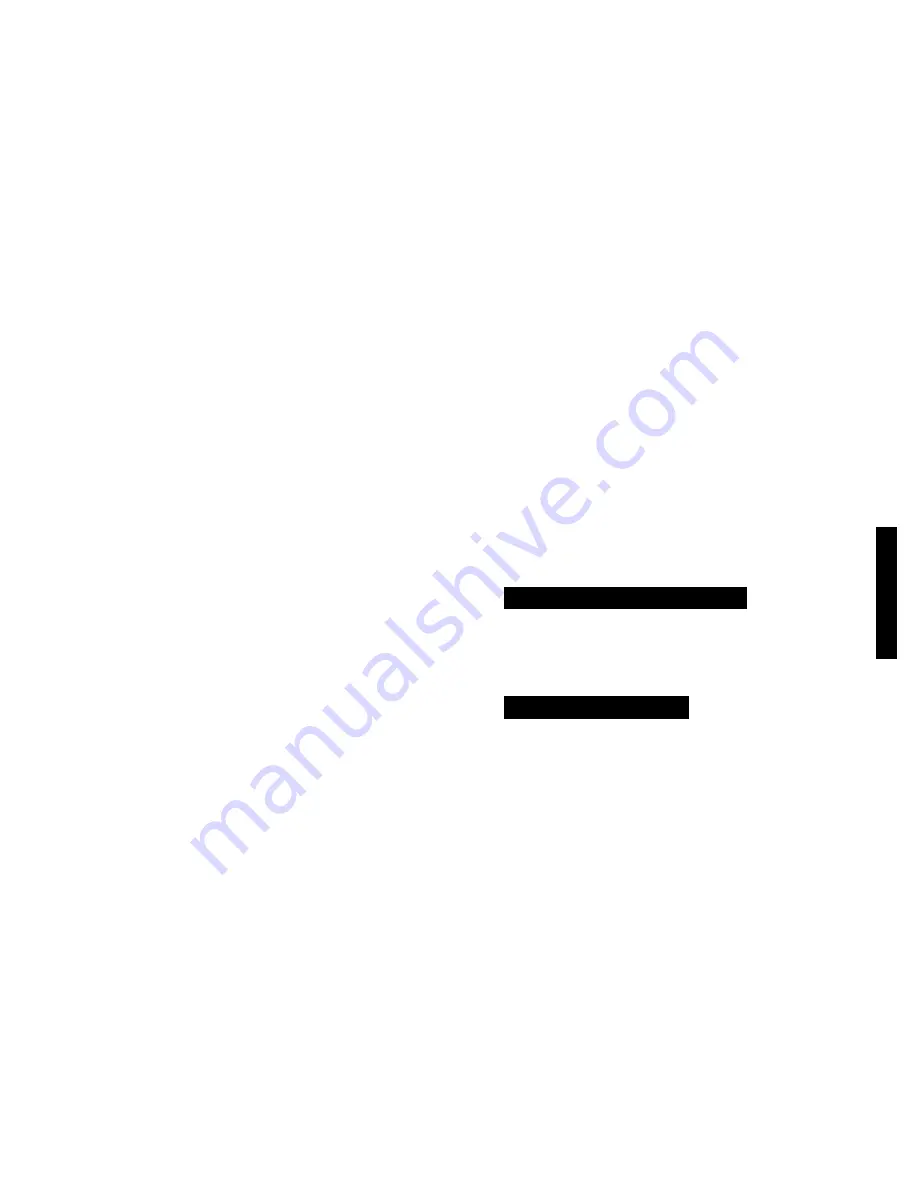
YORK INTERNATIONAL
53
FORM 160.60-O1
Daily
1. Check MicroComputer Control Center displays.
2. If the compressor is in operation, check the bearing oil
pressure by pressing
OIL PRESSURE
key to read
the display on the control center. Also check the oil
level in the oil reservoir. Drain or add oil if necessary.
3. Check entering and leaving condenser water pressure
and temperatures for comparison with job design con-
ditions. Condenser water temperatures can be
checked by pressing
CONDENSER LlQUID TEM-
PERATURES
display key.
4. Check the entering and leaving chilled liquid tem-
peratures and evaporator pressure for comparison with
job design conditions. This can be accomplished by
pressing the
CHILLED LIQUID TEMPS
key and the
REFRIGERANT PRESSURES
key.
5. Check the condenser saturation temperature (based
upon condenser pressure sensed by condenser trans-
ducer). Press the
CHILLER DATA
key. This key may
be depressed repeatedly after depressing the
DIS-
PLAY HOLD
key to display different parameters.
6. Check the compressor discharge temperature. Press
CHILLER DATA
key. During normal operation dis-
charge temperature should not exceed 220°F.
7. Check for any signs of dirty or fouled condenser tubes.
(The temperature difference between water leaving con-
denser and condenser saturation temperature should
not exceed the difference recording for a new unit by
more than 4°F.)
8. Verify proper water treatment.
9. Press the
STATUS
key whenever the display indi-
cates so. This allows any warning messages to be
displayed.
Weekly
1. Check the oil charge (See Oil Charging Procedure,
page 61).
Quarterly
1. Perform chemical analysis of compressor oil.
Semi-Annually (or more often as required.)
1. Change and inspect compressor oil filter element.
2. Oil return system
a.Change dehydrator.
b.Check nozzle or eductor for foreign particles.
3. Check controls and safety cutouts.
Annually (more often if necessary.)
1. Drain and replace the oil in the compressor oil sump
(See Oil Charging Procedure, page 61.)
2. Cooler and Condenser
a.Inspect and clean facility water strainers.
b.Inspect and clean tubes as required.
c.Inspect end sheets.
NEED FOR MAINTENANCE OR SERVICE
If the system is malfunctioning in any manner or the unit is
stopped on one of the safety controls, consult the OPER-
ATING ANALYSIS CHART (pages 64 and 65) of this in-
struction manual. After consulting this chart, if you are un-
able to make the proper repairs or adjustments to start the
compressor or the particular trouble continues to hinder the
performance of the unit, please call the nearest YORK Dis-
trict Office. Failure to report constant troubles could dam-
age the unit and increase the cost of repairs considerably.
NORMAL AND SAFETY SYSTEM SHUTDOWNS
Normal and safety system shutdowns have been built
into the unit to protect it from damage during certain op-
erating conditions. Therefore, it should be understood that
at certain pressures and temperatures, the system will
be stopped automatically by controls that respond to high
temperatures, low temperatures, and low and high pres-
sures, etc. Table 2 (page 62) is an explanation of each
specific shutdown. If the unit shuts down on a Safety
shutdown, the display will read:
SYSTEM SHUTDOWN – PRESS STATUS
Upon pressing the status key, the day-of-week, time-of-
day and cause of shutdown is displayed. Safety shutdowns
require the operator to manually reset the control center
prior to restarting the chiller. When the display reads:
START SEQUENCE INITIATED
the cause of the safety shutdown is automatically cleared
from the memory.
SAFETY SHUTDOWNS (Also see page 14)
Low Discharge Temperature
High Discharge Temperature
Low Evaporator Pressure
High Condenser Pressure
Faulty Condenser Transducer
Low Oil Pressure Differential
High Oil Pressure Differential
High Oil Temperature
Faulty Oil Transducer
Oil Transducer Differential Error
Proximity Sensor Fault
High Drain Line Temperature
Open Thermocouple
Faulty Proximity Sensor
Power Failure
S
E
C
T
3