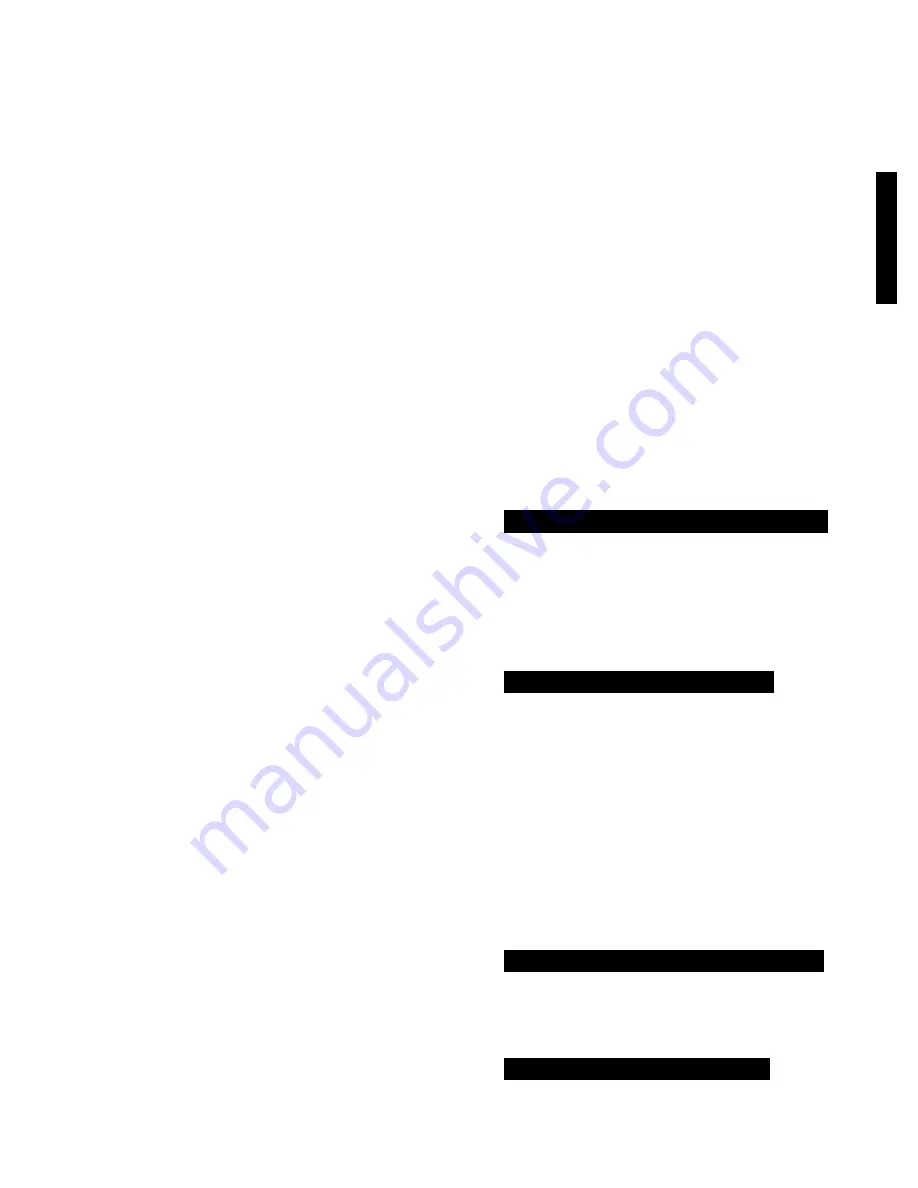
YORK INTERNATIONAL
33
FORM 160.60-O1
At the end of each level control period, the proportion
error and rate and direction (toward or away from setpoint)
of change during the level control period are evaluated to
determine whether the response should be an open or
close output and the duration of the output. The propor-
tion error is compared to programmable setpoints
pro-
portion limit close
and
proportion limit open
to de-
termine the influence of proportion error in the response.
The rate of change and direction of change during the
level control period are then compared to programmable
setpoints
rate limit close
and
rate limit open
to deter-
mine the influence of rate of change in the response.
To explain: At the completion of each level control period,
the actual refrigerant level is compared to the
level setpoint
(programmable from 20% to 80%) to determine the pro-
portion error. An error of plus or minus 3% is considered
zero. The proportion error is then compared to setpoints
proportion limit close
(if level below setpoint) and
pro-
portion limit open
(if level above setpoint). Both of these
setpoints are programmable over the range of 10% to 50%.
If the proportion error exceeds the limit setpoint, the pro-
portion error influence in the response will be large. If the
proportion error is less than the limit setpoint, the propor-
tion error influence in the response will be a result of how
close the proportion error is to the proportion limit setpoint.
Close yields larger influence, further yields smaller influ-
ence. Next, the amount of change in the refrigerant level
during the level control period is compared to program-
mable setpoints
rate limit close
(if level less than setpoint)
and
rate limit open
(If level greater than setpoint). Both of
these setpoints are programmable over the range of 10%
to 50%. A level change of plus or minus 1% during the
level control period is considered zero. If the level change
exceeds the limit setpoint, the rate influence in the re-
sponse will be large. If the level change is less than the
limit setpoint, the rate influence in the response will be a
result of how close the percentage change is to the rate
limit setpoint. Close yields larger influence, further yields
smaller influence.
Therefore, the values programmed for
proportion limit
close, proportion limit open, rate limit close
and
rate
limit open
determine the sensitivity of the response.
Smaller values generally yield greater response for the
same level of refrigerant level change in the
level con-
trol period.
The smaller the number programmed for the
level control period,
the more often an output is ap-
plied to the level control actuator.
Anytime the vanes (PRV) are fully closed (vane motor
switch closed), the output to the level control is opposite
of the output to the vane motor. If a close signal is being
applied to the vane motor, an open signal will be applied
to the level control. If an open signal is being applied to
the vane motor, a close signal will be applied to the level
control. This operation is in effect whether the chiller is
running or shutdown and continues for as long as the
vane motor switch
(VMS)
is closed.
While the chiller is shutdown, a close signal is continu-
ously applied to the vane motor. This causes the vanes
to fully close, closing the VMS. The closing of the VMS
initiates an open signal to the level control. This open
signal is applied to the level control for the duration of the
shutdown (unless someone manually operates the vanes
in
service
mode; then, the level control output is as ex-
plained above). Therefore, the orifice will be in the full
open position prior to starting the chiller.
Because the orifice is in the full open position while the
chiller is shutdown, the sensed refrigerant level will be ap-
proximately 0%. Elevated evaporator pressure with respect
to condenser pressure could cause the level to be higher.
When the chiller is started, after the VMS opens when
entering system run, a linearly increasing ramp is ap-
plied to the level setpoint. This ramp cause the setpoint
to go from the initial refrigerant level (approximately 0%)
to the programmed setpoint over a period of 15 minutes.
While this ramp is in effect,
PULLDN LEVEL=XXX%; SETP=XXX%; ACTUAL=XXX%
is one of the scrolled messages under the
display data
key. PULLDN LEVEL is the ramping setpoint that will
ramp up to the programmed setpoint SETP. SETP is
the level setpoint programmed by the service technician.
ACTUAL is the present refrigerant level. After the 15
minute ramp period has elapsed, this message is re-
placed by
ACTUAL LEVEL=XXX%; LEVEL SETP=XXX%
If the initial refrigerant level is greater than the programmed
setpoint, there is no ramp period. It immediately begins
to control to the programmed setpoint.
While the chiller is running, as long as the VMS is open,
the level control controls to the programmed setpoint. How-
ever, if the vanes close (VMS CLOSES), the outputs to
the level control will be opposite of the outputs applied to
the vane motor as described above; normal level control is
terminated and any ramp that is in effect is terminated.
When the VMS opens, if the actual level is less than the
setpoint, the setpoint is ramped from the actual level to
the programmed setpoint over a 15 minute period.
PULLDN LEVEL=XXX%; SETP=XXX%; ACTUAL=XXX%
is displayed as one of the scrolled messages under the
display data
key while the ramp is in effect. If the actual
level is greater than the level setpoint when the VMS
opens, normal level control is resumed and
ACTUAL LEVEL=XXX%; LEVEL SETP=XXX%
is displayed instead of the ramp message.
S
E
C
T
2