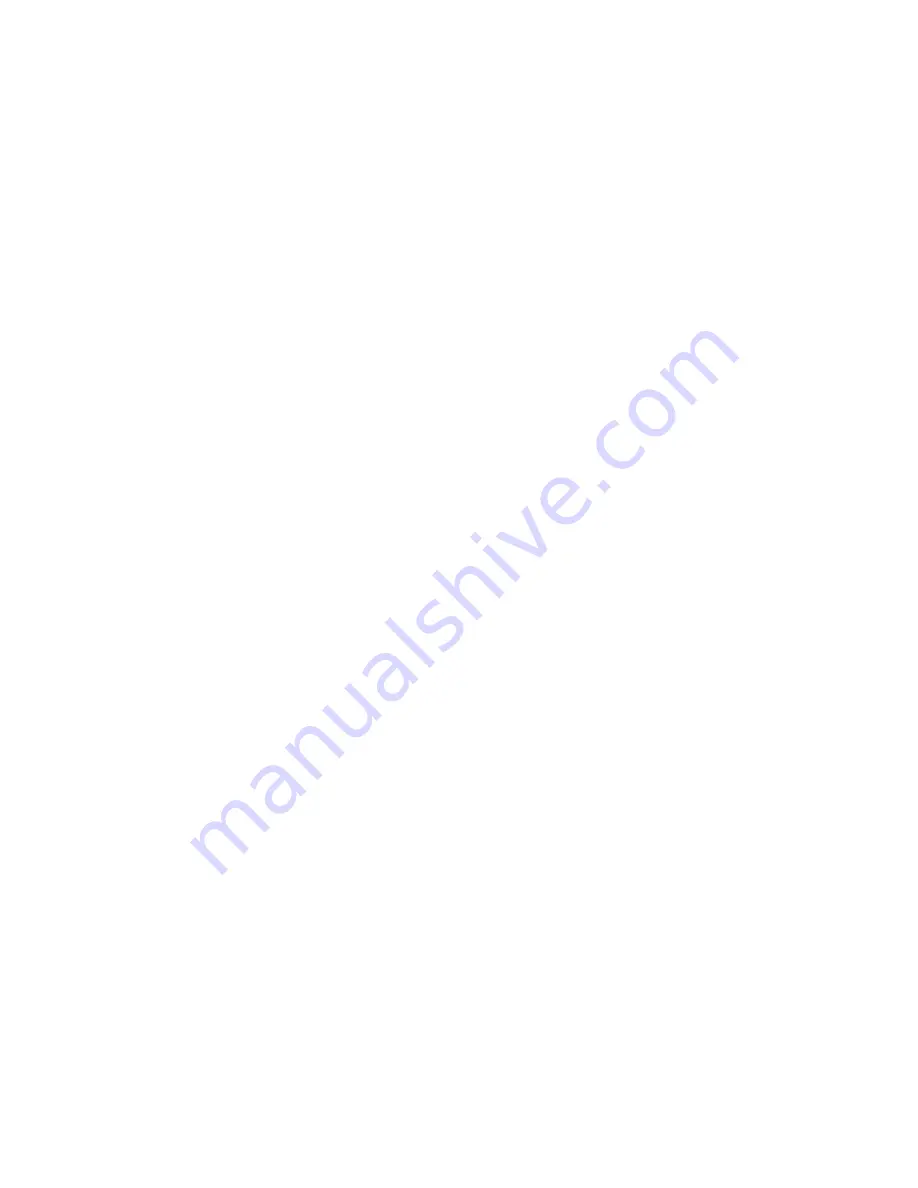
YORK INTERNATIONAL
15
FORM 160.52-N1
NOTE: Units shipped dismantled MUST be
re-assembled by, or under the super-
vision of, a YORK representative.
(See Form 160.52-N6)
Form 7 – Split Shells – Shipped as four major assem-
blies. Unit first factory assembled, refriger-
ant piped, wired and leak tested; then dis-
mantled for shipment. Compressor/motor
assembly removed from shells and skidded.
Cooler and condenser shells are separated
at tube sheets and are not skidded. Refriger-
ant lines between shells are flanged and
capped, requiring no welding.
All wiring integral with compressor is left on
it. All wiring harnesses on shells are removed.
All openings on compressor and shells are
closed and charged with dry nitrogen (2 to 3
PSIG).
Miscellaneous packaging of control center,
tubing, water temperature controls, wiring, oil
isolators, solid state starter (option), etc.; re-
frigerant charge shipped separately.
NOTE: Units shipped dismantled MUST be
re-assembled by, or under the super-
vision of, a YORK representative.
(See Form 160.52-N6)
When more than one chiller is involved, the major parts
of each unit will be marked to prevent mixing of assem-
blies. (Piping and Wiring Drawings to be furnished by
YORK.)
INSPECTION – DAMAGE – SHORTAGE
The unit shipment should be checked on arrival to see
that all major pieces, boxes and crates are received.
Each unit should be checked on the trailer or rail car
when received, before unloading, for any visible signs
of damage. Any damage or signs of possible damage
must be reported to the transportation company imme-
diately for their inspection.
YORK WILL NOT BE RESPONSIBLE FOR ANY
DAMAGE IN SHIPMENT OR AT JOB SITE OR LOSS
OF PARTS. (Refer to Shipping Damage Claims, Form
50.15-NM)
When received at the job site all containers should be
opened and contents checked against the packing list.
Any material shortage should be reported to YORK im-
mediately. (Refer to Shipping Damage Claims, Form
50.15-NM)
CHILLER DATA PLATE
A unit data plate is mounted on the control center as-
sembly of each unit, giving unit model number; design
working pressure; water passes; refrigerant charge; se-
rial numbers; and motor power characteristics and con-
nection diagrams.
Additional information may be found on the motor data
plate. This information should be included when con-
tacting the factory on any problem relating to the motor.
RIGGING
The complete standard chiller is shipped without skids.
(When optional skids are used it may be necessary to
remove the skids so riggers skates can be used under
the unit end sheets to reduce overall height.)
Each unit has four (4) lifting holes (two in each end) in
the end sheets which should be used to lift the unit.
(See Fig. 4)
Care should be taken at all times during rigging and
handling of the chiller to avoid damage to the unit and
its external connections. Lift only using holes shown
in Fig. 4.
Do not lift the unit with slings around motor/com-
pressor assembly or by means of eyebolts in the
tapped holes of the compressor motor assembly.
Do not turn a unit on its side for rigging. Do not rig
vertically.
Use of Slings (See Fig. 4 for proper use of slings in
rigging.)
CAUTION: If necessary to rig the chiller by one end to
permit lifting or dropping through a vertical
passageway, such as an elevator shaft, con-
tact YORK factory shipping for special rig-
ging instructions.
The rigging and operating weights and overall dimen-
sions are given on pages 5 thru 12 as a guide in deter-
mining the clearances required for rigging. (Add 6" to
overall height for optional skidded unit.)