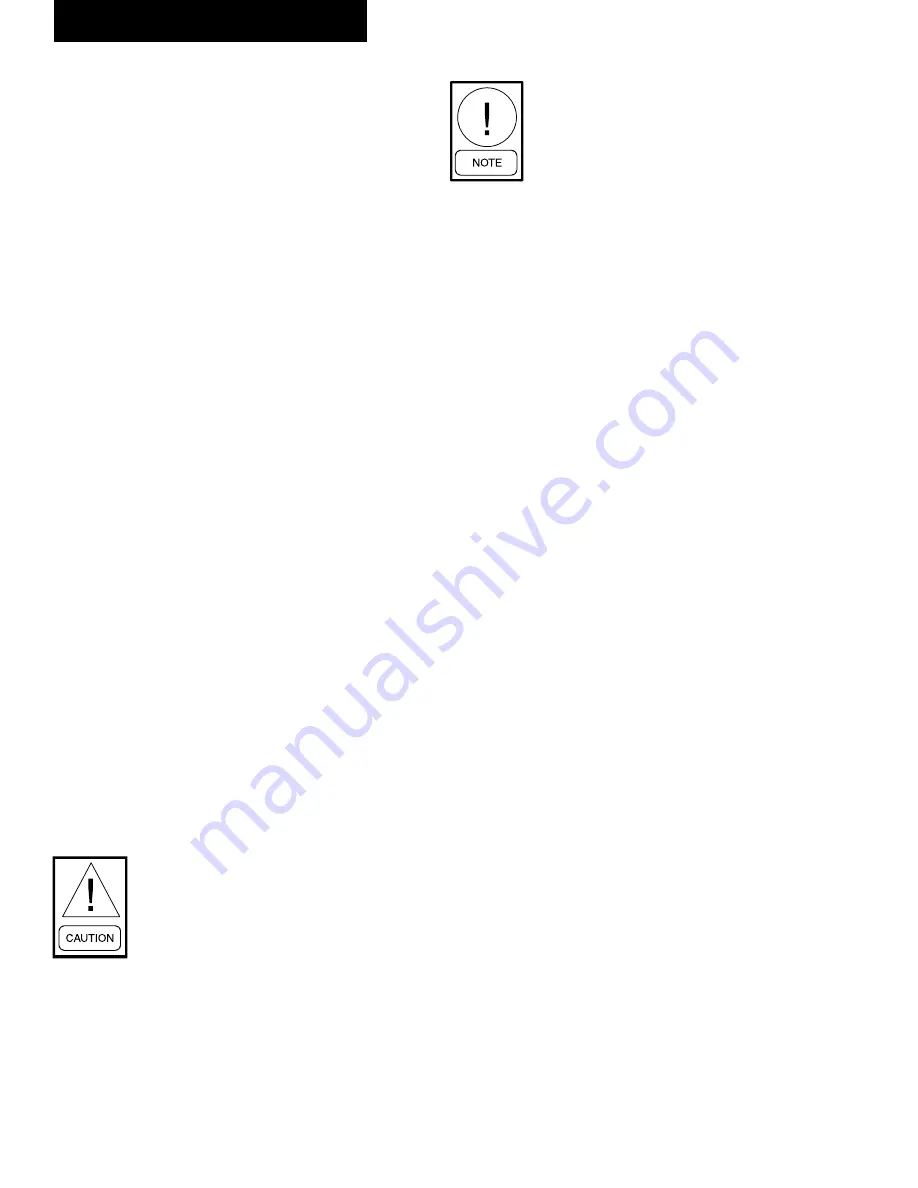
YORK INTERNATIONAL
20
FORM 160.54-O2(1102)
FORM 160.54-O2(1102)
21
YORK INTERNATIONAL
While the chiller is shut down, the orifice will be in
the fully open position causing the sensed level to be
approximately 0%. When the chiller is started, after
the vane motor end switch (VMS) opens when enter-
ing
SYSTEM RUN
, if actual level is less than the
level setpoint, a linearly increasing ramp is applied
to the level setpoint. This ramp causes the setpoint to
go from the initial refrigerant level (approximately
0%) to the programmed setpoint over a period of 15
minutes.
If the actual level is greater than the setpoint when the
VMS opens, there is no pulldown period, it imme-
diately begins to control to the programmed setpoint.
While the chiller is running, the refrigerant level is
normally controlled to the level setpoint. However,
anytime the vanes fully close (VMS closes), normal
level control is terminated, any refrigerant level set-
point pulldown in effect is cancelled and the outputs to
the level control will be opposite that which is supplied
to the vane motor (i.e., when a close pulse is applied
to the vane motor, an open pulse is applied to the level
control, etc.). When the VMS opens, if the refriger-
ant level is less than the level setpoint, a refrigerant
level setpoint pulldown is initiated as described above.
Otherwise, the level is controlled to the programmed
setpoint.
OPTIONAL SERVICE ISOLATION VALVES
If your chiller is equipped with optional service iso-
lation valves on the discharge and liquid line, these
valves must remain open during operation. These
valves are used for isolating the refrigerant charge in
either the evaporator or condenser to allow service
access to the system. A refrigerant pump-out unit will
be required to isolate the refrigerant.
Isolation of the refrigerant in this
system must be performed by a quali-
fied service technician.
OPTIONAL HOT GAS BYPASS
Hot gas bypass is optional and is used to eliminate
compressor surge during light load or high head
operation. The OptiView control panel will automati-
cally modulate the hot gas valve open and closed as
required. Adjustment of the hot gas control valve must
be performed by a qualified service technician fol-
lowing the Hot Gas Set-up procedure.
Changes in chilled water flow will
require readjustment of the hot gas
control to insure proper operation.
OTIVIEW CONTROL CENTER
(See Section 2)
The OptiView Control Center is factory-mounted,
wired and tested. The electronic panel automatically
controls the operation of the unit in meeting system
cooling requirements while minimizing energy usage.
For detailed information on the Control Center, refer
to “Section 2” of this manual.
SOLID STATE STARTER (Optional)
The Solid State Starter is a reduced voltage starter
that controls and maintains a constant current flow to
the motor during start-up. It is mounted on the chiller.
Power and control wiring between the starter and
chiller are factory installed. Available for 380-600
volts, the starter enclosure is NEMA-1 with a hinged
access door with lock and key. Electrical lugs for
incoming power wiring are provided.
VARIABLE SPEED DRIVE (Optional)
A 460V – 3-Ph – 60/50 Hz Variable Speed Drive can
be factory packaged with the chiller. It is designed to
vary the compressor motor speed and prerotation vane
position by controlling the frequency and voltage of
the electrical power to the motor. Operational infor-
mation is contained in Form 160.00-O1. The control
logic automatically adjusts motor speed and compres-
sor prerotation vane position for maximum part load
efficiency by analyzing information fed to it by sen-
sors located throughout the chiller.
System Components Description