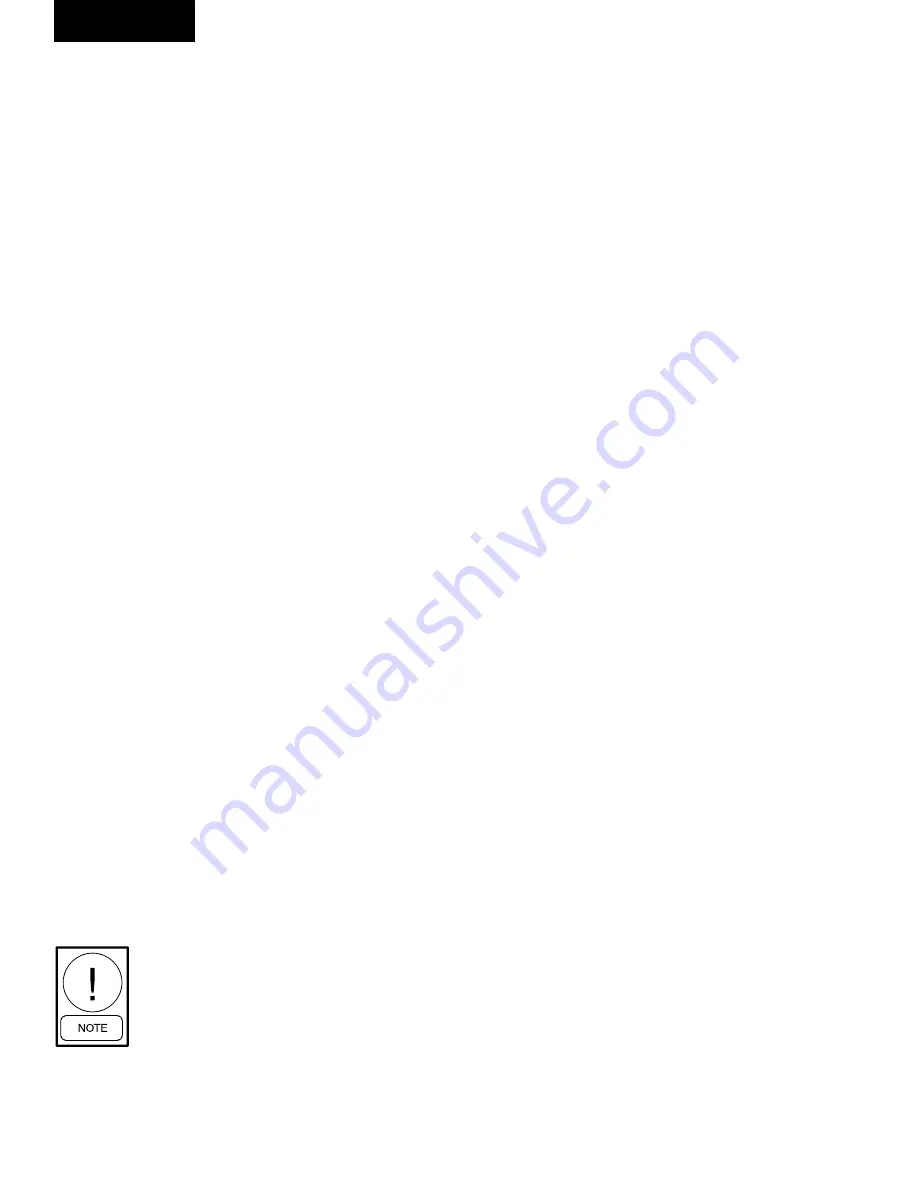
YORK INTERNATIONAL
32
FORM 160.54-O2(1102)
FORM 160.54-O2(1102)
33
YORK INTERNATIONAL
COMMERCIAL ACID CLEANING
In many major cities, commercial organizations now
offer a specialized service of acid cleaning evapora-
tors and condensers. If acid cleaning is required,
YORK recommends the use of this type of organiza-
tion. The Dow Industries Service Division of the Dow
Chemical Company, Tulsa, Oklahoma, with branches
in principal cities is one of the most reliable of these
companies.
TESTING FOR EVAPORATOR AND CONDENSER
TUBE LEAKS
Evaporator and condenser tube leaks in R-134a
systems may result in refrigerant leaking into the
water circuit, or water leaking into the shell depend-
ing on the pressure levels. If refrigerant is leaking
into the water, it can be detected at the liquid head
vents after a period of shutdown. If water is leaking
into the refrigerant, system capacity and efficiency
will drop off sharply. If a tube is leaking and water
has entered the system, the evaporator and condenser
should be valved off from the rest of the water circuit
and drained immediately to prevent severe rusting
and corrosion. The refrigerant system should then be
drained and purged with dry nitrogen to prevent se-
vere rusting and corrosion. If a tube leak is indicated,
the exact location of the leak may be determined as
follows:
1. Remove the heads and listen at each section of
tubes for a hissing sound that would indicate gas
leakage. This will assist in locating the section of
tubes to be further investigated. If the probable
location of the leaky tubes has been determined,
treat that section in the following manner (if the
location is not definite, all the tubes will require
investigations).
2. Wash off both tube heads and the ends of all tubes
with water.
Do not use carbon tetrachloride for
this purpose since its fumes give the
same flame discoloration that the
refrigerant does.
3. With nitrogen or dry air, blow out the tubes to
clear them of traces of refrigerant laden moisture
from the circulation water. As soon as the tubes
are clear, a cork should be driven into each end of
the tube. Pressurize the dry system with 50 to 100
PSIG (345 to 690 kPa) of nitrogen. Repeat this
with all of the other tubes in the suspected section
or, if necessary, with all the tubes in the evaporator
or condenser. Allow the evaporator or condenser
to remain corked up to 12 to 24 hours before
proceeding. Depending upon the amount of leak-
age, the corks may blow from the end of a tube,
indicating the location of the leakage. If not, if will
be necessary to make a very thorough test with the
leak detector.
4. After the tubes have been corked for 12 to 24
hours, it is recommended that two men working at
both ends of the evaporator carefully test each tube
– one man removing corks at one end and the other
at the opposite end to remove corks and handle the
leak detector. Start with the top row of tubes in the
section being investigated. Remove the corks at
the ends of one tube simultaneously and insert the
exploring tube for 5 seconds – this should be long
enough to draw into the detector any refrigerant
gas that might have leaked through the tube walls.
A fan placed at the end of the evaporator opposite
the detector will assure that any leakage will travel
through the tube to the detector.
5. Mark any leaking tubes for later identification.
6. If any of the tube sheet joints are leaking, the leak
should be indicated by the detector. If a tube sheet
leak is suspected, its exact location may be found
by using a soap solution. A continuous buildup of
bubbles around a tube indicates a tube sheet leak.
Maintenance