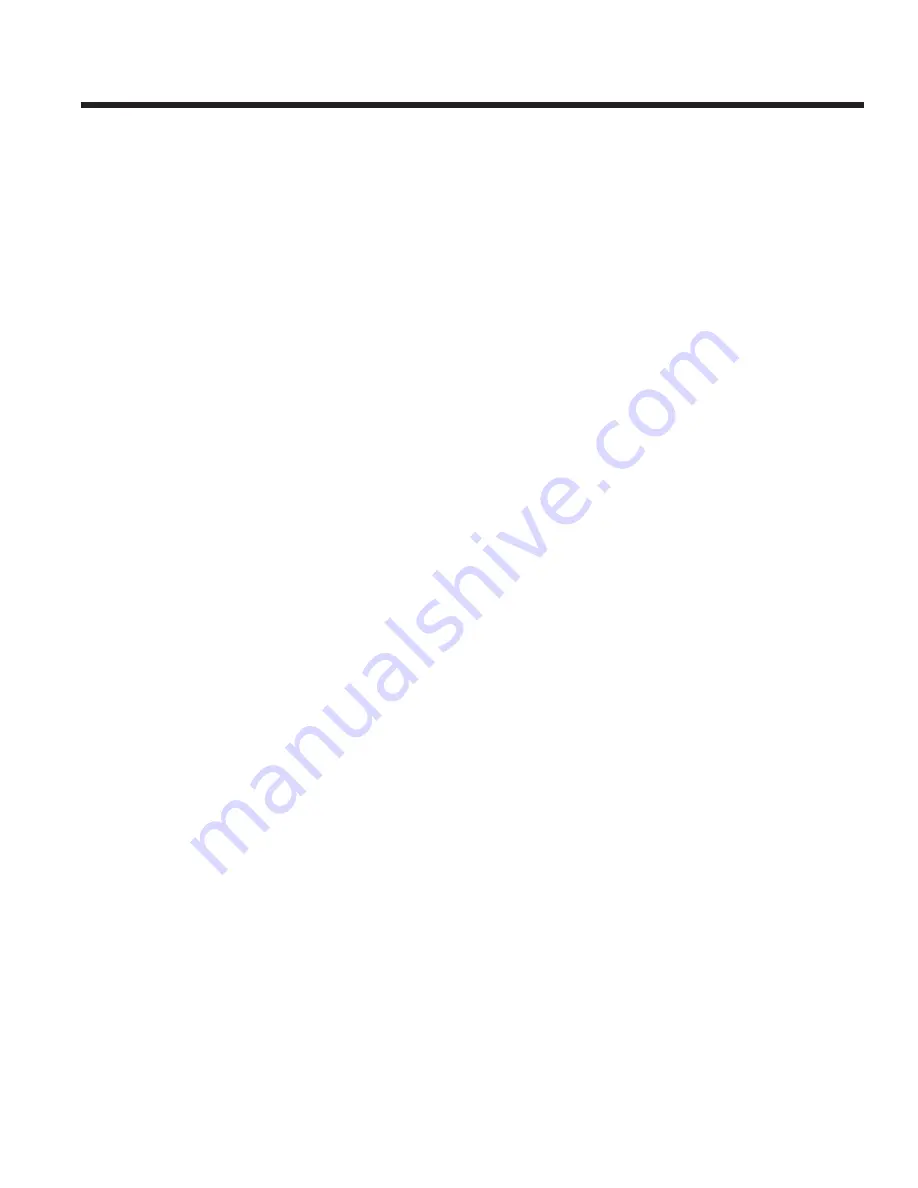
JOHNSON CONTROLS
FORM 201.23-EG1 (1007)
7
Accessories and Options
SOUND REDUCTION OPTIONS
– The standard chiller
has fans that operate at normal speed, no compressor
enclosure, and is typically used in non-sensitive sound
areas such as industrial areas or locations with loud traffic
background noise. One or more of the following sound re
-
duction options may be employed by the system designer
as normally generated machine noise is considered in the
overall project design.
Ultra Quiet Fans (Factory Mounted)
– With this option,
the basic chiller is equipped with specially designed fans
and motors to provide lower sound levels and retain ap
-
propriate airflow. The result is reduced fan generated
noise with no adverse effect on the chiller capacity or
efficiency performance.
Two-Speed Fans (Factory Mounted)
– With this option,
the basic chiller is equipped with fans designed with two
operating speeds. At high ambient conditions the fans
operate at the normal speed with sound levels equivalent
to Ultra Quiet Fans. As the ambient temperature falls the
fans automatically reduce to slow speed reducing sound
levels. If very low sound is required at all ambient condi
-
tions normal fan speed can be inhibited.
Reduced Sound Option (Factory Mounted)
– With this
option the chiller is equipped with an unlined compres
-
sor enclosure. This option is typically used for daytime
operation where background noise is lower than normal
city traffic etc.
Low Sound Option (Factory Mounted)
– This option
is only available with the selection of Ultra Quiet Fans or
Two-Speed Fans. The chiller is equipped with an acousti
-
cally lined compressor enclosure. This option is typically
for locations near residential areas, hotels, or hospitals
etc where background noise is limited. When paired with
the Two-Speed Fan option the unit can operate at normal
speed during the day, when background noise levels are
noticeable, and at low speed in the evening and at night
when background levels are lower.
SilentNight™
- Standard variable speed compressors
result in a chiller system that has lower part load sound
values than conventional air-cooled chillers. Over 99%
of chiller operating hours occur when building loads are
less than design and/or ambient temperatures are less
than design. As a result, all YCIV model chillers will
operate with less than full load sound output nearly all
the time – this is especially important on evenings and
weekends when neighbors are home the most. Due to
time of day based sound regulations it may be desirable
to force the chiller to a lower sound level on demand.
The SilentNight™ control option provides a control input
to limit sound output of the chiller based on time of day.
This feature is programmable at the chiller panel or can
be controlled remotely via signal (4-20mA or 0-10 VDC)
from a BAS system.
CIRCUIT BREAKER
– Power panel will come equipped
with a factory mounted circuit breaker at point of incom
-
ing single or multi-point connection that provides the
following:
• Means to disconnect power mounted on chiller.
• Circuit breaker sized to provide the motor branch
circuit protection, short circuit protection and ground
fault protection for the motor branch-circuit conductors,
the motor control apparatus and the motors. (Chiller
mounted circuit breaker option sized for branch circuit
protection eliminates the need to provide a separate
‘line of sight’ disconnect and separate branch circuit
protection device.)
• Lockable operating handle that extends through power
panel door so that power may be disconnected without
opening any panel doors.
• Short Circuit Withstand Rating of the chiller electrical
enclosure when using circuit breaker option is 380,
400, & 460V: 65,000 Amps. Rating IAW UL508.
CONDENSER COIL PROTECTION
– Standard con-
denser coil construction materials include aluminum fins,
copper tubes, and galvanized tube supports for generally
good corrosion resistance. However, these materials are
not adequate for all environments. The system designer
can take steps to inhibit coil corrosion in harsh applica-
tions and enhance equipment life by choosing from these
options based on project design parameters and related
environmental factors. (
Factory Mounted
)
• PRE-COATED FIN CONDENSER COILS
– The air
cooled condenser coils are constructed of epoxy-
coated aluminum fins. This can provide corrosion
resistance comparable to copper-fin coils in typical
seashore locations. Either these or the post coated
coils (below), are recommended for units being in
-
stalled at the seashore or where salt spray may hit
the unit.
• POST-COATED EPOXY DIPPED CONDENSER
COILS
– The unit is built with dipped-cured epoxy
condenser coils. This is another choice for seashore
and other corrosive applications (with the exception
of strong alkalies, oxidizers and wet bromine, chlo-
rine and fluorine in concentrations greater than 100
ppm).
• COPPER FIN CONDENSER COILS
– The unit con-
structed with copper tube condenser coils, which have
copper fins. (This is not recommended for units in
areas where they may be exposed to acid rain.)
PROTECTIVE CHILLER PANELS:
• Wire Panels (full unit)
– UV stabilized black polyvi
-
nyl chloride coated, heavy gauge, welded wire mesh
guards mounted on the exterior of the unit. Protects
condenser coil faces and prevents unauthorized ac
-
cess to refrigerant components (compressors, pipes,
Summary of Contents for Latitude YCIV0157E
Page 115: ...JOHNSON CONTROLS FORM 201 23 EG1 1007 115 INTENTIONALLY LEFT BLANK...
Page 127: ...JOHNSON CONTROLS FORM 201 23 EG1 1007 127 INTENTIONALLY LEFT BLANK...
Page 128: ...JOHNSON CONTROLS 128 Typical Control Wiring Two Compressor...
Page 130: ...JOHNSON CONTROLS 130 Typical Control Wiring Three Compressor...
Page 138: ...JOHNSON CONTROLS 138...
Page 139: ...JOHNSON CONTROLS FORM 201 23 EG1 1007 139...
Page 140: ...Form 201 23 EG1 1007 Supersedes 201 23 EG1 607 File in ET2...