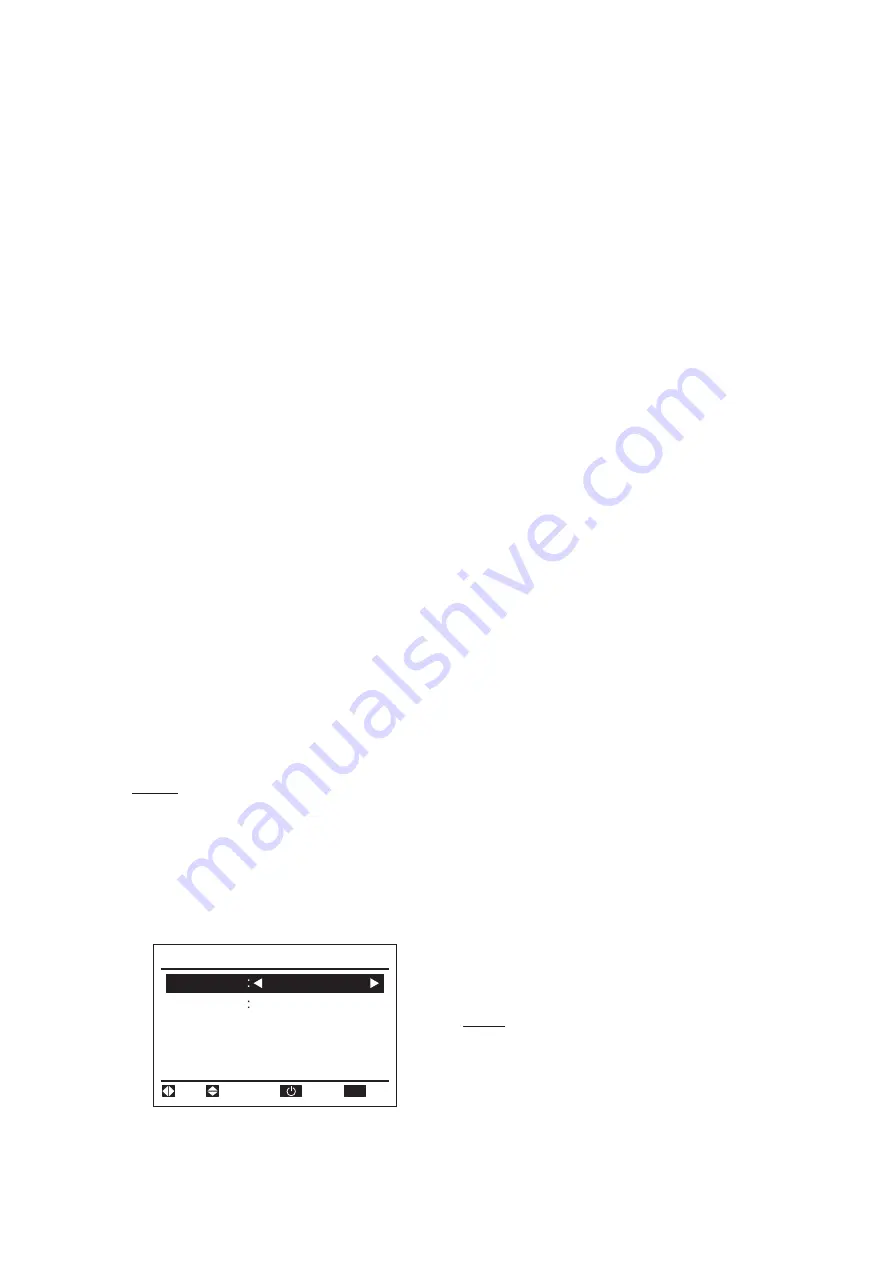
P01432Q-rev.1
35
9. Test Run
Test Run Screen
9.1 Before Test Run
Verify that there are no problems with the installation, and do not perform Test Run until all the following
conditions have been resolved.
Refer to the "Installation and Maintenance Manual" for the outdoor unit for details on Test Run operations
from the outdoor unit.
Verify that refrigerant piping and the communication cable are connected to the same refrigerant cycle
system. If not, it will cause an abnormal operation and damage to instrumentation.
(1) Verify that electrical resistance is more than one megaohm, by measuring the resistance between
ground and the terminal the terminus for electrical components. If the electrical resistance is less than
one megaohm, do NOT operate the system until the electrical current outflow to ground is detected and
repaired. Do not introduce any high voltage to the terminals of the communication cables
(TB2 [A, B, 1 and 2]).
(2) Verify that each wire is connected correctly at the correct phase for the power supply. If it is incorrectly
connected, the unit will not operate and the wired controller will display the alarm code “05”. In this
case, check the phase for the primary power supply according to the “Attention” label affixed to the back
side of the service cover. Then, with the power supply turned OFF at the power supply, remake the
necessary connections.
(3) Check to ensure that the main power supply has been turned ON for more than 12 hours, to warm up
the compressor oil by the crankcase heater.
(4) Verify that all DIP Switch settings are correct. Refer to Section 8.5 “DIP Switch Settings”.
9.2 Test Run
After all installation work is completed, Test Run should be performed.
(1) Check to ensure that stop valves (gas and liquid) for the outdoor unit are fully opened.
(2) Whenever indoor units are connected to the VRF system, perform the Test Run for the indoor units one
by one sequentially and then check the refrigerant piping system and the electrical wiring system for
conformity. (If these multiple indoor units are operated simultaneously, system conformity cannot be
verified.)
(3) Perform the Test Run in accordance with the following procedure. Ensure that the Test Run is carried
out without any problem. The following procedure shows a case where a wired controller is utilized.
If other controllers are activated instead, refer to the "Installation and Maintenance Manual" for those
other controllers.
NOTE:
The outdoor unit may not be operated depending on the indoor and outdoor temperature conditions.
Refer to the "Installation and Maintenance Manual" for outdoor units for details.
(a) Press and hold “Menu” and “Back/Help” simultaneously for at least 3 seconds.
The Test Run menu will be displayed.
● The Test Run menu will be displayed.
Back
Adj.
Sel.
ON
Rtrn
Test Run Setting: 2 units
MODE
SPEED
AUTO
COOL
NOTE
When the “00 unit” is displayed, the auto-address
function may be working.
Cancel
“Test Run”
mode and reset.