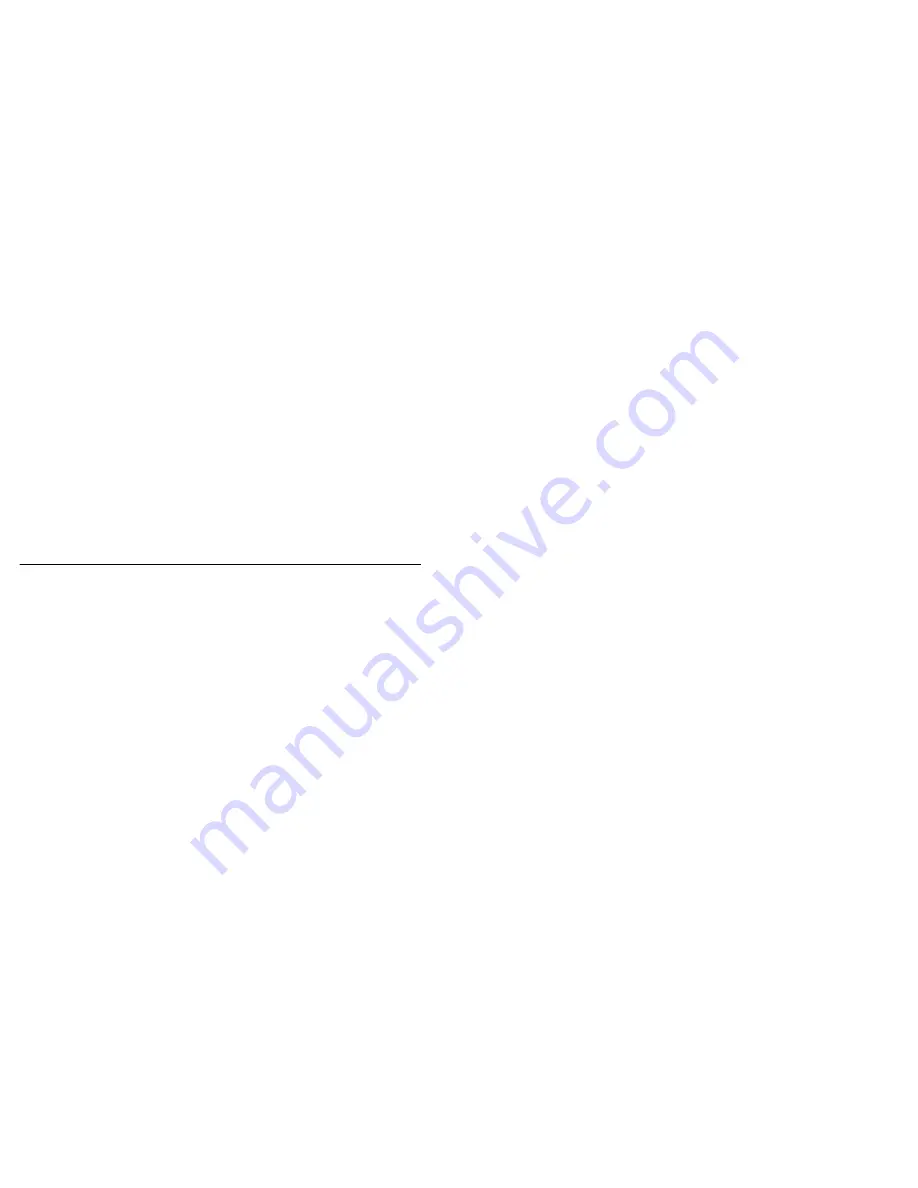
FIRST STAGE OF COOLING
A call for cooling at terminal Y1 energizes relay RY1. Relay
RY1 closes contacts RY1-1, energizing time delay relay 3TR.
If time delay relay 3TR is satisfied as described below, it will
energize its output terminal Y2, which is connected to compres-
sor 1 control module terminal M1.
If the compressor 1 control module is satisfied as described
below, it will apply power to terminal 7 of low or high pressure
lock out relay (LOR) contacts. See a description of the LOR
operation below. If the LOR coil is not energized (not locked
out), the LOR contacts will be closed, energizing contactor 1M,
which powers compressor 1 and condenser fan motor 1.
When 1M is energized on H3CE240 units, auxiliary contact
1M-AC2 is closed, powering terminal 1 for opening the stage 1
solenoid in air handlers which feature a stage 1 solenoid.
If the low ambient temperature switch TLA is closed, it will allow
condenser fan 2 contactor 3M to energize. TLA opens as the
temperature falls below 50 F and closes as the ambient rises
above 60 F. TLA is used on the H3CE180, not the H3CE240.
Anti-short Cycle Time Delay Relays 3TR and 4TR
Relay 3TR, which serves compressor 1 control, has an adjust-
able low voltage lock out which is set at 20V in the factory. The
voltage applied to 3TR must be above its lock out setting and
5 minutes must elapse since the relay was last energized
before it will energize its output terminal Y2. Relay 4TR is
identical but it serves compressor 2 control.
Compressor Control Module
If the compressor control module terminals L1 (or T1) and L2
(or T2) have 24 V applied and the internal compressor tempera-
ture lock out is inactive, the internal switch connecting M1 and
M2 will be closed. M1 to M2 will open if one of the compressor’s
internal temperature sensors exceeds its limit. M1 to M2 stays
open for 30 minutes after a internal temperature limit is ex-
ceeded. The 30 minute lock out may be reset prior to the 30
minutes expiring by removing power to the control module
terminals L1 and L2. During normal operation, each compres-
sor control module should always be powered at the L1 and L2
terminals, whether there is a call for cooling or not.
Low or High Pressure Lock Out Operation
If the lock out circuit path is opened during a call for cooling,
the lock out relay (LOR) coil will energize, opening LOR-1
contacts and disabling all compressor operation. The lock out
circuit path is open if:
•
the lock out relay contacts LOR-1 are open, OR
•
the low pressure switch LP is open AND the low
pressure switch bypass timer contacts 1TR-1 are open
OR
•
the high pressure switch HP is open.
Once the LOR coil has been energized, it remains energized,
locking out cooling operation until the call for cooling has been
removed. When Y1 is returned to 0 volts, the LOR coil is no
longer energized, closing the LOR-1 contacts and removing the
lock out.
The low pressure bypass timer 1TR leaves the 1TR-1 contacts
closed upon the start of a call for cooling until its 90 second
(nominal) timer has expired. This bypasses the low pressure
switch during start up. After the time delay has elapsed, 1TR-1
contacts are opened, once again allowing low pressure to
trigger the lock out circuit if the low pressure switch opens.
START-UP
CRANKCASE HEATER
The crankcase heater must be energized at least 8 hours before
starting the compressor. To energize the crankcase heater, the
main disconnect switch must be closed. During this 8 hour
period, the system switch on the room thermostat must be
“OFF” to prevent the compressor from starting.
CAUTION: DO NOT ATTEMPT TO START THE COMPRES-
SOR WITHOUT AT LEAST 8 HOURS OF CRANK-
CASE HEAT OR COMPRESSOR DAMAGE CAN
OCCUR.
Make sure that the bottom of the compressor is warm to the
touch to prove crankcase heater operation.
PRE-START CHECK
Before starting the unit, complete the following check list:
1. Have sufficient clearances been provided?
2. Has all foreign matter been removed from the interior of the
unit (tools, construction or shipping materials, etc.)?
3. Have the condenser fans been rotated manually to check
for free rotation?
4. Are all wiring connections tight?
5. Does the available power supply agree with the nameplate
data on the unit?
6. Is the control circuit transformer set for the proper voltage?
7. Have the fuses, disconnect switch and power wire been
sized properly?
8. Are all compressor hold-down nuts properly secured?
9. Are any refrigerant lines touching each other or any sheet
metal surface? Rubbing due to vibration could cause a
refrigerant leak.
10. Are there any visible signs of a refrigerant leak, such as oil
residue?
11. Is any electrical wire laying against a hot refrigerant line?
INITIAL START-UP
1. Supply power to the unit through the disconnect switch at
least 8 hours prior to starting the compressor.
2. Move the system switch on the thermostat to the AUTO or
COOL position.
3. Reduce the setting of the room thermostat to energize the
compressor.
4. Check the operation of the evaporator unit per the manufac-
turer’s recommendations.
5. With an ammeter, check the compressor amps against the
unit data plate.
6. Check for refrigerant leaks.
7. Check for any abnormal noises and/or vibrations, and make
the necessary adjustments to correct (e.g. fan blade(s)
touching shroud, refrigerant lines hitting on sheet metal,
etc.)
8. After the unit has been operating for several minutes, shut
off the main power supply at the disconnect switch and
inspect all factory wiring connections and bolted surfaces for
tightness.
OPERATION
550.23-N6Y
12
Unitary Products Group