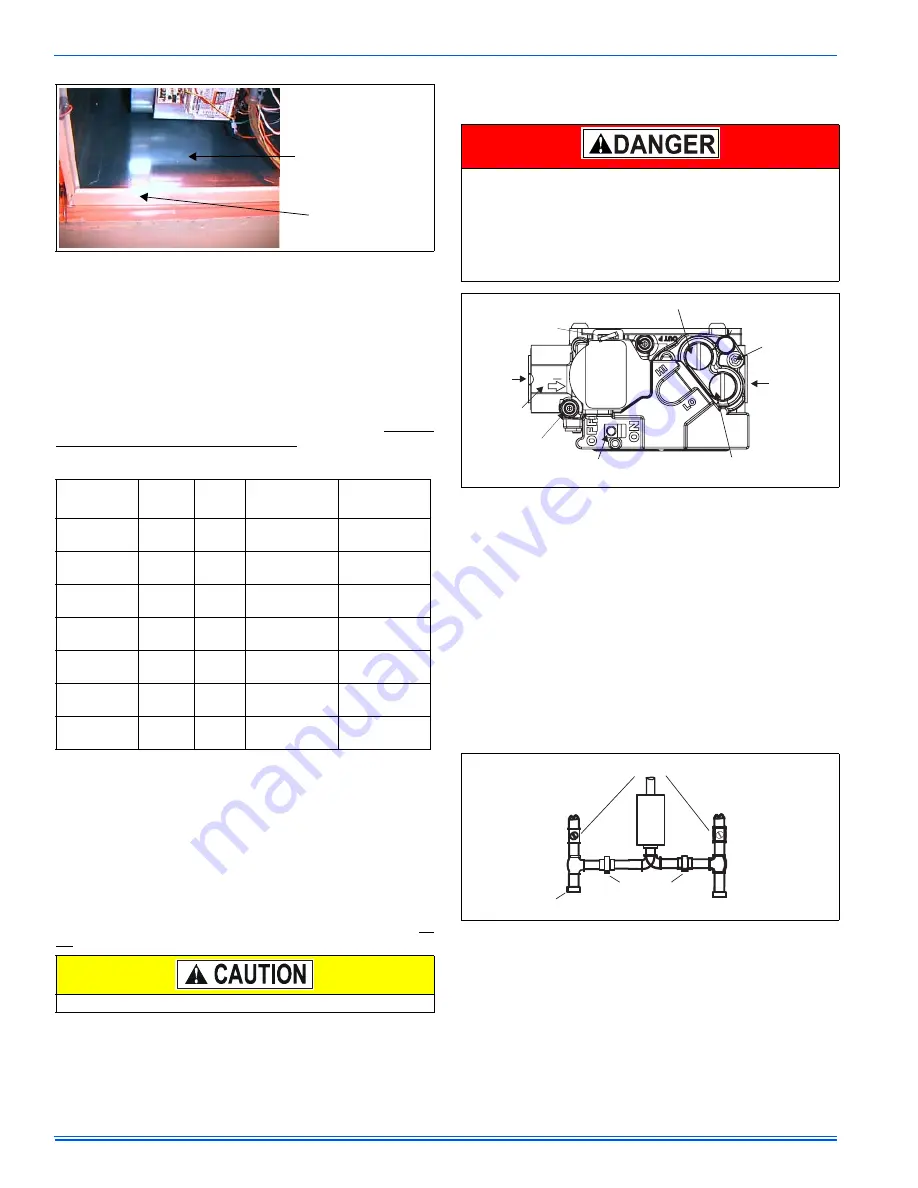
106633-UIM-A-0205
6
Unitary Products Group
IMPORTANT:
If an external mounted filter rack is being used see the
instructions provided with that accessory for proper hole cut size.
SECTION III: FILTERS
FILTER INSTALLATION
All applications require the use of a filter. A high velocity filter and a side
return filter rack are provided for field installation. Replacement filter
size is shown in Table 4.
Filters must be installed external to the furnace cabinet.
DO NOT
attempt to install filters inside the furnace.
SIDE RETURN - FILTER INSTALLATION
Locate and mark the side return opening. Refer to Figure 1 for dimen-
sions of the cutout.
Install the side filter rack following the instructions provided with that
accessory. If a filter(s) is provided at another location in the return air
system, the ductwork may be directly attached to the furnace side
panel.If not provided with the furnace, an accessory filter rack is avail-
able for mounting the filter external to the cabinet.
IMPORTANT:
Some accessories such as electronic air cleaners and
pleated media may require a larger side opening. Follow the instruc-
tions supplied with that accessory for side opening requirements. Do
not cut the opening larger than the dimensions shown in Figure 1.
SECTION IV: GAS PIPING
GAS SAFETY
IMPORTANT:
Plan your gas supply before determining the correct gas
pipe entry. Use 90-degree service elbow(s), or short nipples and con-
ventional 90-degree elbow(s) to enter through the cabinet access holes.
GAS PIPING INSTALLATION
Properly sized wrought iron, approved flexible or steel pipe must be
used when making gas connections to the unit. If local codes allow the
use of a flexible gas appliance connection, always use a new listed con-
nector. Do not use a connector that has previously serviced another gas
appliance.
Some utility companies or local codes require pipe sizes larger than the
minimum sizes listed in these instructions and in the codes. The furnace
rating plate and the instructions in this section specify the type of gas
approved for this furnace - only use those approved gases. The instal-
lation of a drip leg and ground union is required. Refer to Figure 4.
IMPORTANT:
An accessible manual shutoff valve must be installed
upstream of the furnace gas controls and within 6 feet (1.8 m) of the fur-
nace.
The furnace must be isolated from the gas supply piping system by
closing its individual external manual shutoff valve during any pressure
testing of the gas supply piping system at pressures equal to or greater
than 1/2 psig (3.5 kPa).
FIGURE 2:
Furnace Base Rectangular Blockoff Panel
TABLE 4:
Filter Sizes
Input / Output
BTU/H (kW)
CFM
(m
3
/min)
Cabinet
Size
Side Return
Filter in. (cm)
Bottom Return
Filter in. (cm)
40/38
(11.7/10.8)
1200
(34.0)
A
16 x 25
(41 x 64)
14 x 25
(36 x 64)
60/56
(17.8/16.1)
1200
(34.0)
B
16 x 25
(41 x 64)
16 x 25
(41 x 64)
80/75
(23.4/22.0)
1200
(34.0)
B
16 x 25
(41 x 64)
16 x 25
(41 x 64)
80/75
(23.4/22.0
1600
(45.3)
C
16 x 25
(41 x 64)
20 x 25
(51 x 64)
100/93
(29.3/27.8)
1600
(45.3)
C
16 x 25
(41 x 64)
20 x 25
(51 x 64)
100/93
(29.3/27.8)
2000
(56.6)
C
16 x 25
(41 x 64)
20 x 25
(51 x 64)
120/112
(35.1/32.8)
2000
(56.6)
D
(2) 16 x 25
(2) (41 x 64)
22 x 25
(56 x 64)
All installations must have a filter installed.
Toe Plate
Removable Rectangular
Base Panel.
An overpressure protection device, such as a pressure regulator,
must be installed in the gas piping system upstream of the furnace
and must act to limit the downstream pressure to the gas valve so it
does not exceed 0.5 PSI {14" w.c. (3.48 kPa)}. Pressures exceed-
ing 0.5 PSI {14” w.c. (3.48 kPa)} at the gas valve will cause damage
to the gas valve, resulting in a fire or explosion or cause damage to
the furnace or some of its components that will result in property
damage and loss of life.
FIGURE 3:
Gas Valve
FIGURE 4:
Gas Piping
INLET
WRENCH
BOSS
INLET
PRESSURE
PORT
ON OFF
SWITCH
LOW STAGE REGULATOR
ADJUSTMENT
OUTLET
OUTLET
PRESSURE
PORT
VENT
PORT
HIGH STAGE REGULATOR
ADJUSTMENT
EXTERNAL MANUAL
SHUTOFF VALVE
TO GAS
SUPPLY
TO GAS
SUPPLY
GROUNDED JOINT UNION
MAY BE INSTALLED
INSIDE OR OUTSIDE UNIT.
DRIP
LEG