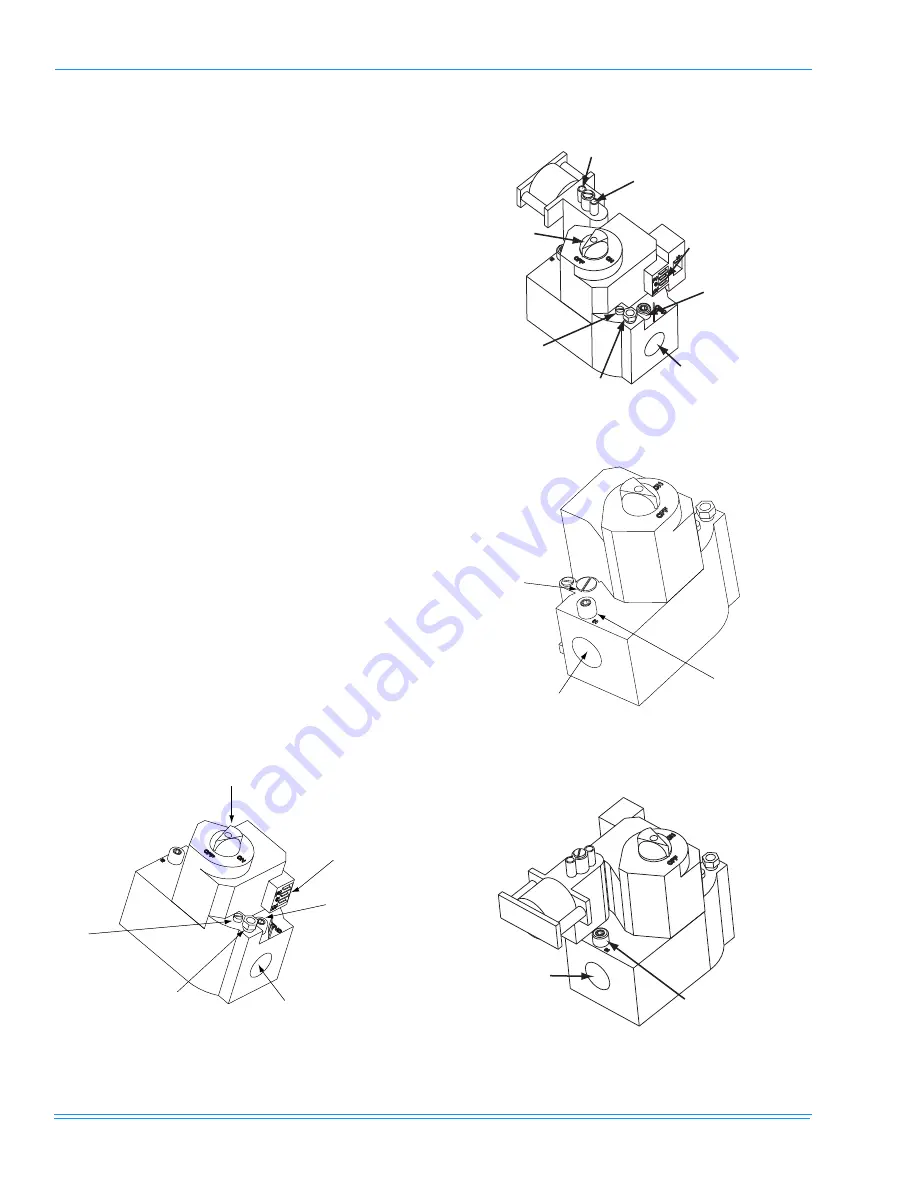
280241-YIM-D-0909
20
Johnson Controls Unitary Products
TO TURN OFF GAS TO UNIT
1.
Set the thermostat to the OFF position.
2.
Turn off all electric power to the appliance if service is to
be performed.
3.
Remove the control access panel.
4.
Turn the gas valve switch to the OFF position. DO NOT
FORCE.
5.
Replace the control access panel.
POST-START CHECK LIST (GAS)
After the entire control circuit has been energized and the
heating section is operating, make the following checks:
1.
Check for gas leaks in the unit piping as well as the sup-
ply piping.
2.
Check for correct manifold gas pressures. See Checking
Gas Input.
3.
Check the supply gas pressure. It must be within the lim-
its shown on rating nameplate. Supply pressure should
be checked with all gas appliances in the building at full
fire. At no time should the standby gas line pressure
exceed 13.5", nor the operating pressure drop below
4.5" for natural gas units. If gas pressure is outside these
limits, contact the local gas utility for corrective action.
MANIFOLD GAS PRESSURE ADJUSTMENT
Small adjustments to the gas flow may be made by turning
the pressure regulator adjusting screw on the automatic gas
valve. Refer to Figures 13 and 14.
FIGURE 13 - SINGLE STAGE GAS VALVE - FRONT
FIGURE 14 - TWO STAGE GAS VALVE - FRONT
FIGURE 15 - SINGLE STAGE GAS VALVE - REAR
FIGURE 16 - TWO STAGE GAS VALVE - REAR
Manual
Gas Switch
Pilot
Adjustment
(Remove Cap)
Pilot Gas
Connection
(1/4” Compression)
1/2” NPT
(Outlet)
Outlet Pressure
Tap (1/8” NPT)
Electrical
Connection
Hi Fire
(2nd Stage)
Manifold Pressure
Low Fire
(1st Stage)
Manifold Pressure
Adjustment
Electrical
Connection
½
NPT
(Outlet)
Manifold
Pressure
Tap
Pilot
Gas
Connect
Pilot
Adjustment
(Remove Cap)
Manual
Gas
Switch
Manifold Pressure
Adjustment
(Under Cap)
1/2” NPT
(Inlet)
Line Pressure
Tap (1/8” NPT)
Line Pressure
Tap
½
NPT
(Inlet)