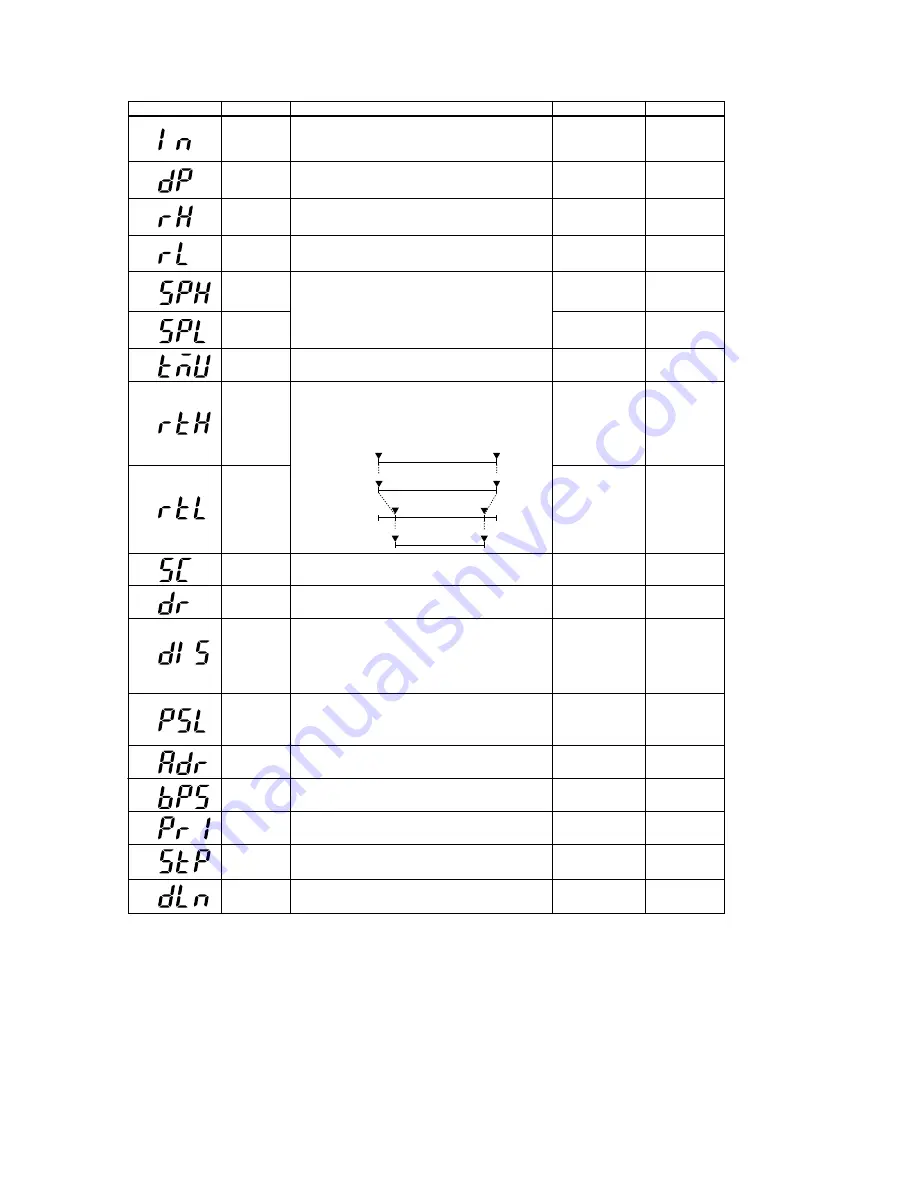
IM 05C01F12-41E
15
IN
Measured input
type
1 to 23, 31 to 48 (See measured input range code list.) (See page3)
OFF(0): No input
(If no measured input type is specified at the time of ordering,
you must set the measured input type.)
OFF(0) or
the input range code
specified with order
DIS
DI-function
selection
OFF(0):Function of /EX does not work
ON(1):Terminals (3)-(5) Hold when DI=ON
Cancel hold when DI=OFF
Terminals (4)-(5) Start program operation when DI=ON
Stop program operation when DI=OFF
Note: When DIS=ON, the operation mode can not be changed by
key operation. However, only the RESET key is operable.
OFF(0)
SC
SUPER
function
ON(1): Uses the SUPER function
OFF(0): Does not use SUPER function
OFF(0)
DR
Direct/reverse
action
0: Reverse action
1: Direct action
0
TMU
Program time
unit
Sets the time unit of a program.
0: hour,minute
1: minute,second
0
RTH
RTL
RL
RL
DP
ADR
Controller
address
1 to 99
However, the number of controllers that can be connected per
host device is 31 at the maximum.
1
BPS
Baud rate
2.4(0): 2400 bps
4.8(1): 4800 bps
9.6(2): 9600 bps
9.6(2)
PRI
Parity
NON(0): Disabled
EVN(1); Even parity
ODD(2): Odd parity
EVN(1)
STP
Stop bit
1 or 2 bits
1 bit
DLN
Data length
7 or 8 bits
• 8 bits when ladder, MODBUS (RTU)
• 7 bits when MODBUS (ASCII)
8 bits
PSL
Protocol
selection
0: PC-link communication
1: PC-link communication with sum check
2: Ladder communication
3: MODBUS in ASCII mode
4: MODBUS in RTU mode
0
(2) Setup Parameters
Code
Name
Setting range and unit
Default
User setting
Decimal point
position of
measured input
0: No decimal place (nnnn)
1: One decimal place (nnn.n)
2: Two decimal places (nn.nn)
3: Three decimal places (n.nnn)
1
Maximum value
of measured
input scale
100.0
Minimum value
of measured
input scale
–1999 to (RH –1)
0.0
(Displayed at voltage input)
(RL + 1) to 9999
(Displayed at voltage input)
(Displayed at voltage input)
Maximum value
of retransmission
output
Minimum value
of retransmission
output
Temperature input : Within measured input range
Voltage input : (RTL+1digit) to max. value of measured input
scale (RH)
Min. value of measured input scale (RL) to (RTH-1digit)
However, RTL<RTH
Maximum value of
measured input range
(scale)
Minimum value of
measured input range
(scale)
SPH
SPL
Maximum value
of program
setting range
Minimum value
of program
setting range
(SPL+1digit) to max. value of measured input range (scale).
Min value of measured input range (scale) to (SPH-1digit)
Unit:
°
C/
°
F
Note that SPL<SPH
Place limits on the program setting range within the measured
input range (scale) to prevent a program setpoint from being
beyond the limits of setting range by mistake.
Maximum value of
measured input range
(scale)
Minimum value of
measured input range
(scale)
Numbers in ( ) are the parmeter setpoints that apply when the
communication function is used. Ex. OFF(0), ON(1)
Parameter rarely changed in normal use after once having been set.
Measured input range
PV retransmission range
(Factory-set default)
PV retransmission range
(after scaling)
RTL
RTL
Minimum value
of measured input
range (scale)
Maximum value
of measured input
range (scale)
RTH
4mA
20mA
RTH
PV retransmission output
(4 to 20mA)