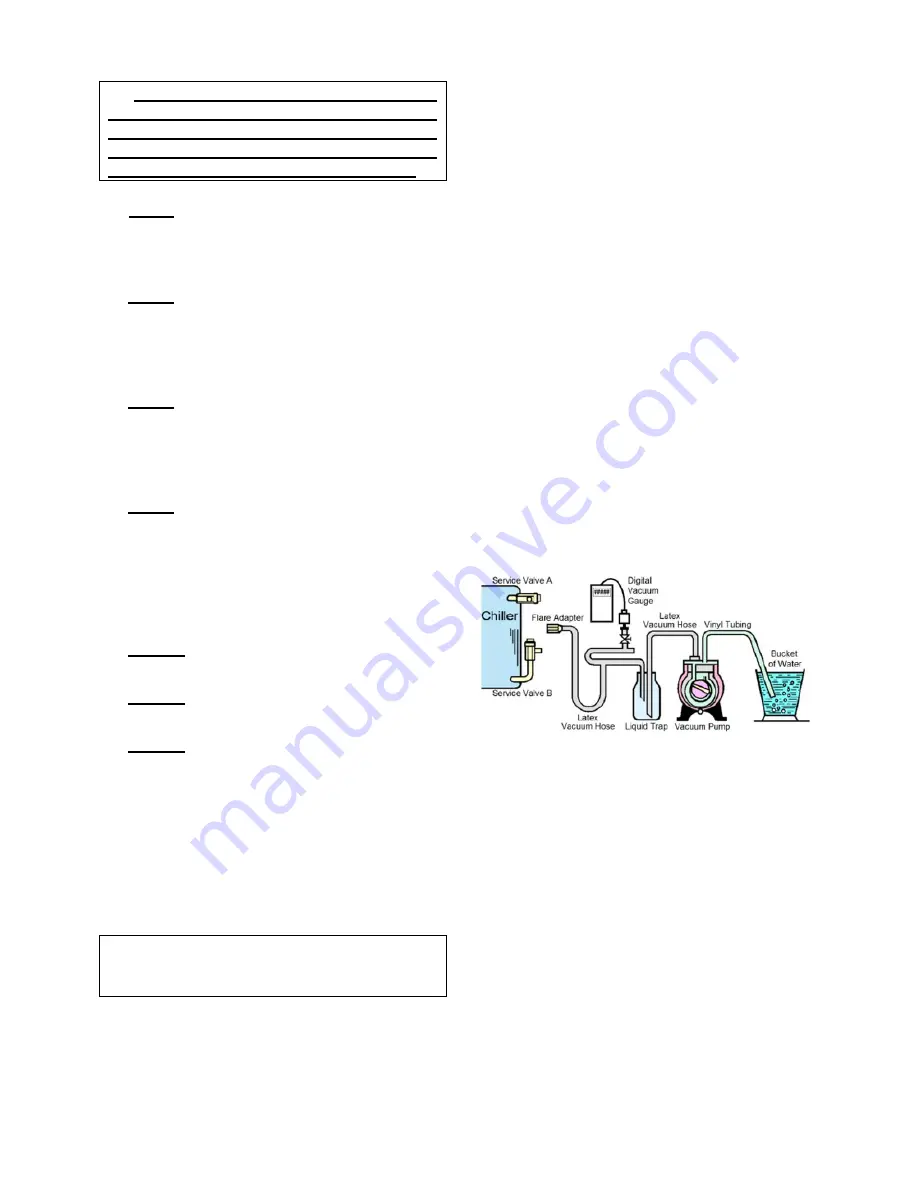
9
*** Great care must be taken to ensure
that no oil enters the Yazaki chiller-
heater! Permanent damage could result
from even a small amount of oil being
introduced into the vacuum section! ***
Never
leave a vacuum pump running
unattended. Power loss could allow the
chiller-heater vacuum section to suck oil
out of the pump in a matter of seconds.
Never
have the Service Valve open
unless the vacuum pump is running and
the integrity of the vacuum lines between
the valve and the pump has been verified
as tight.
Never
have the vacuum pump discharge
tube in the water bucket unless the
vacuum pump is running. The vacuum
pump could suck water from the bucket
and contaminate the oil charge.
Never
pull
an
extended
vacuum
(exceeding a few hours)
. If such seems to
be necessary, there is likely to be
something wrong with the vacuum pump
or the oil has been contaminated with
moisture inherently found inside the
chiller-heater vacuum section.
Always
start with a fresh oil charge in the
vacuum pump.
Always
use a liquid trap or collection
flask.
Always
use a vacuum gauge to verify the
level of vacuum achieved. Run time has
almost nothing to do with the level of
vacuum achieved.
Use only dual-stage, deep vacuum
pumps. Typical refrigeration vacuum pumps
may not perform well on a vessel as large as
the chiller-heater
’s vacuum section. Just
because the vacuum pump has stopped
producing bubbles in the water bucket does
NOT mean the vacuum level is adequate. A
digital vacuum gauge MUST be used in
order to determine the true level of vacuum
achieved.
The desired level of vacuum on a
machine that is not running would be less
than 2000 microns
(<2 mmHg)
, with less than
1000 microns
(<1 mmHg)
preferred. On a
machine actively running in Cool mode
(currently attempting to satisfy chilled water loop
load)
, the desired level of vacuum is 4000-
5000 microns
(4-5 mmHg)
, no less. Any lower
than that on a running machine can cause
the
vacuum
pump
to
remove
an
extraordinary amount of refrigerant vapor
(water)
.
A
step-by-step,
detailed
evacuation
method is provided in the Service Manual.
The general evacuation assembly setup is
displayed in Figure 9.
Figure 9
– GENERAL EVACUATION
ASSEMBLY SETUP
CHEMICAL MAINTENANCE
It is not necessary to perform regular
chemical maintenance on the Yazaki
chiller-heater itself.
The
chemical
balance
has
been
established in the factory during run testing.
Normally, the only chemical that must be
maintained is the inhibitor charge. By
capturing
non-condensable
gases,
comparisons can be made to determine if
the normal hydrogen byproduct is being
produced at anticipated rates. If more
hydrogen is being produced than anticipated,
a maintenance inhibitor charge may need to
be introduced into the machine by the ASP.
An inhibitor charge is typically needed every
three
(3)
years in Yazaki gas-fired chiller-
heaters.
Summary of Contents for CH-K100
Page 15: ......