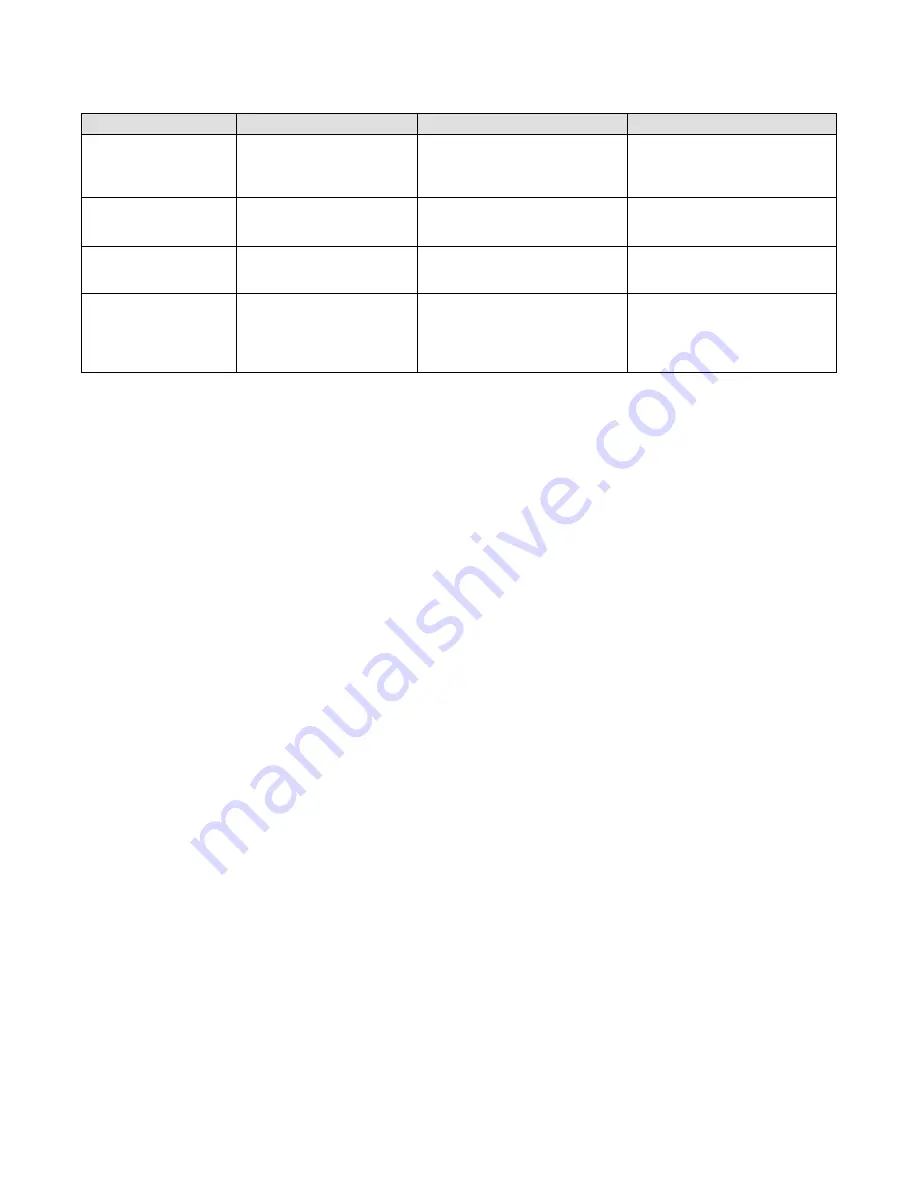
Date: 05/16/08, Rev: 08-05
Page 13 of 38
TM.G7SW.117
4.9
Alarms
Alarm Display
Description
Cause
Countermeasures
RHS
Run Homing Seq
Run homing sequence
A move or learn command was
given before the drive has been
homed. This will only occur when
P1-01 = 1 or 2.
Perform a homing routine.
POSOT
Pos Ovr Travel
Positive Over-travel
The machine has moved past the
positive over-travel switch.
Drive can be moved out of positive
over-travel using the “Jog Reverse”
input.
NEGOT
Neg Ovr Travel
Negative Over-travel
The machine has moved past the
negative over-travel switch.
Drive can be moved out of negative
over-travel using the “Jog Forward”
input.
SENCR
Serial Encoder Reading
The drive is receiving position
information from the absolute
incremental encoder. All run
commands are ignored during
this time.
Absolute incremental encoder is
reporting its position by bringing a
multifunction input (A2 or A3) above
9V.
Wait for the absolute incremental
encoder to finish homing (35 sec.
max), or troubleshoot analog input
wiring.