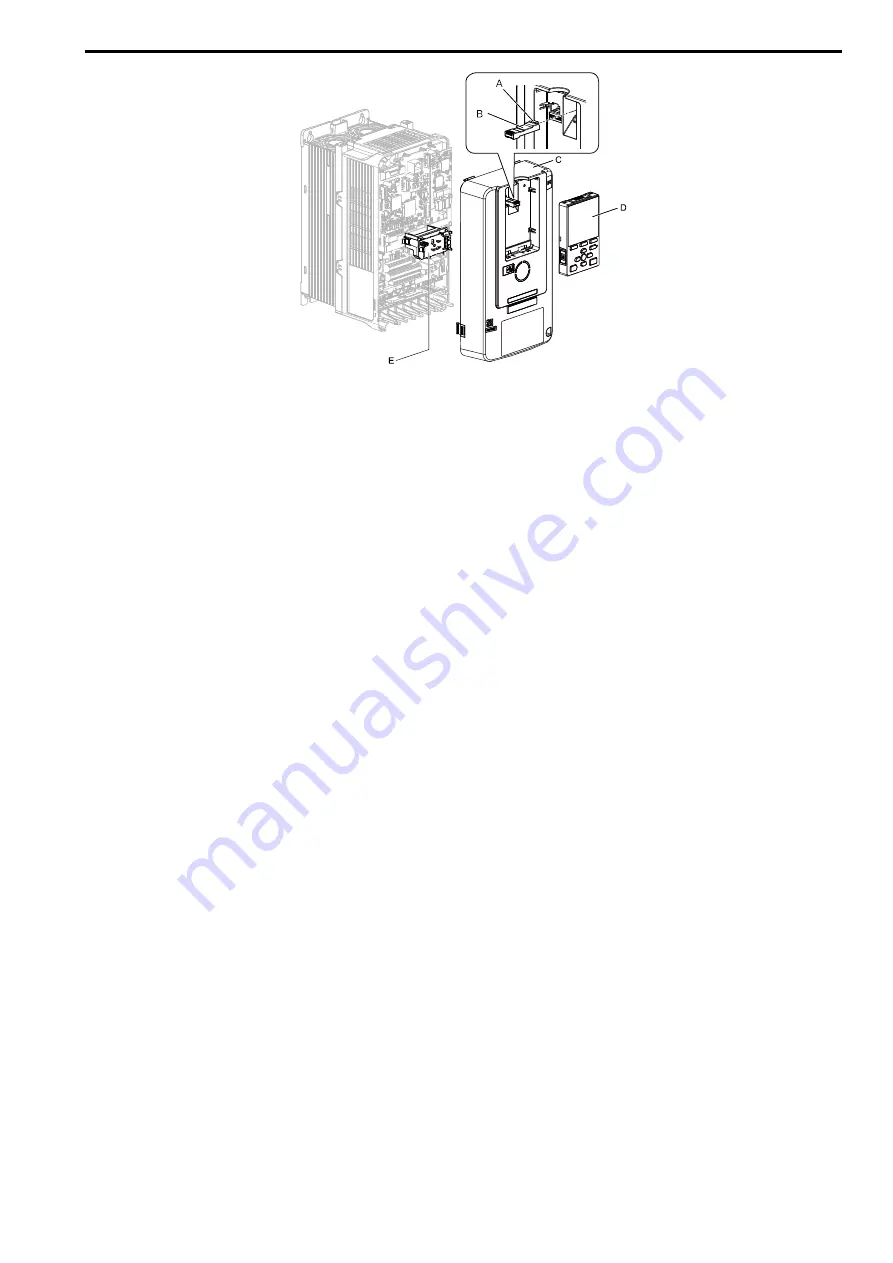
YASKAWA
SIEP C730600 0E YAI Modbus TCP/IP Technical Manual
21
A - Keypad connector tab
B - Keypad connector
C - Drive front cover
D - Keypad
E - LED Status Ring board
Figure 5.19 Install the LED Status Ring board, Front Cover, and Keypad
7.
Set drive parameters in
Related Drive Parameters on page 27
for correct option performance.
■
Procedure D
This section shows the procedure to install and wire the option on an HV600 drive.
Prepare the Drive for the Option
Before you install the option on a YASKAWA AC Drive HV600, make sure that the option software version is
PRG: 0383 or later.
Correctly wire the drive as specified by the manual packaged with the drive. Make sure that the drive functions
correctly. Refer to the drive manuals for more information.