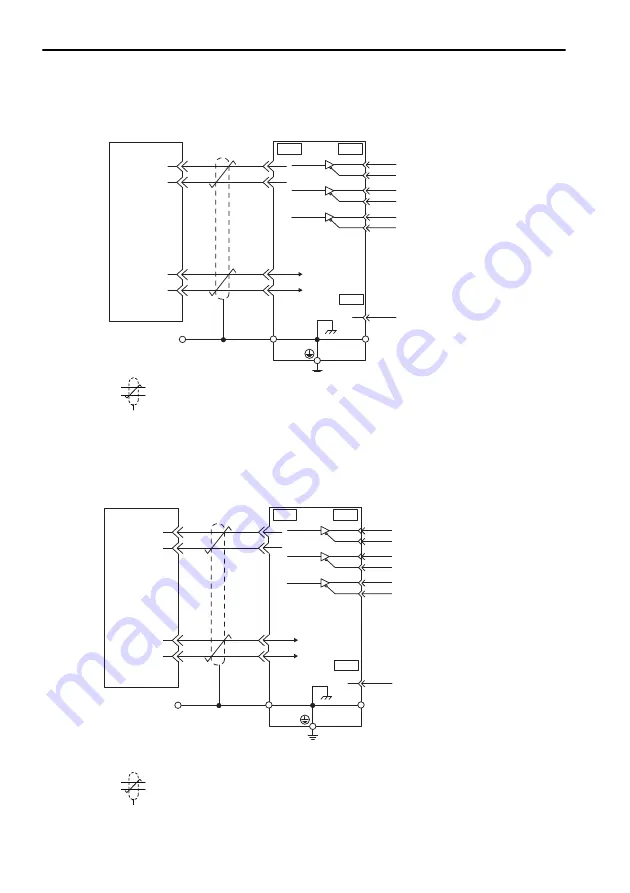
www.dadehpardazan.ir 88594014-15
3 Wiring and Connection
3.5.2 Linear Scale Connection Examples
3-44
(3)
Linear Scale Made by Mitutoyo
represents shielded twisted-pair wires.
(4)
Linear Scale Made by Magnescale Co., Ltd.
SR75, SR85, SR77, SR87
represents shielded twisted-pair wires.
∗
Absolute linear scale
made by Mitutoyo
PS
/PS
PG5V
PG0V
2
6
1
5
Shielded wire
Connector
shell
PG5 V
PG0 V
5
6
1
2
Connector
shell
SERVOPACK
CN2
CN1
19
0 V
PAO
/PAO
PBO
/PBO
PCO
/PCO
17
18
20
21
22
Connector
shell
Phase A
Phase B
Phase C
Output line-driver
SN75ALS194 manu-
factured by Texas
Instrument or the
equivalent
CN1
SG
16
JZSP-CLP70-
-E
∗
Linear scale made by
Magnescale Co., Ltd.
PS
/PS
PG5V
PG0V
Shielded wire
Connector
shell
PG5 V
PG0 V
5
6
1
2
Connector
shell
SERVOPACK
CN2
CN1
19
0 V
PAO
/PAO
PBO
/PBO
PCO
/PCO
17
18
20
21
22
Connector
shell
Phase A
Phase B
Phase C
CN1
SG
16
Output line-driver
SN75ALS194 manu-
factured by Texas
Instrument or the
equivalent
Connection cable made
by Magnescale Co., Ltd.