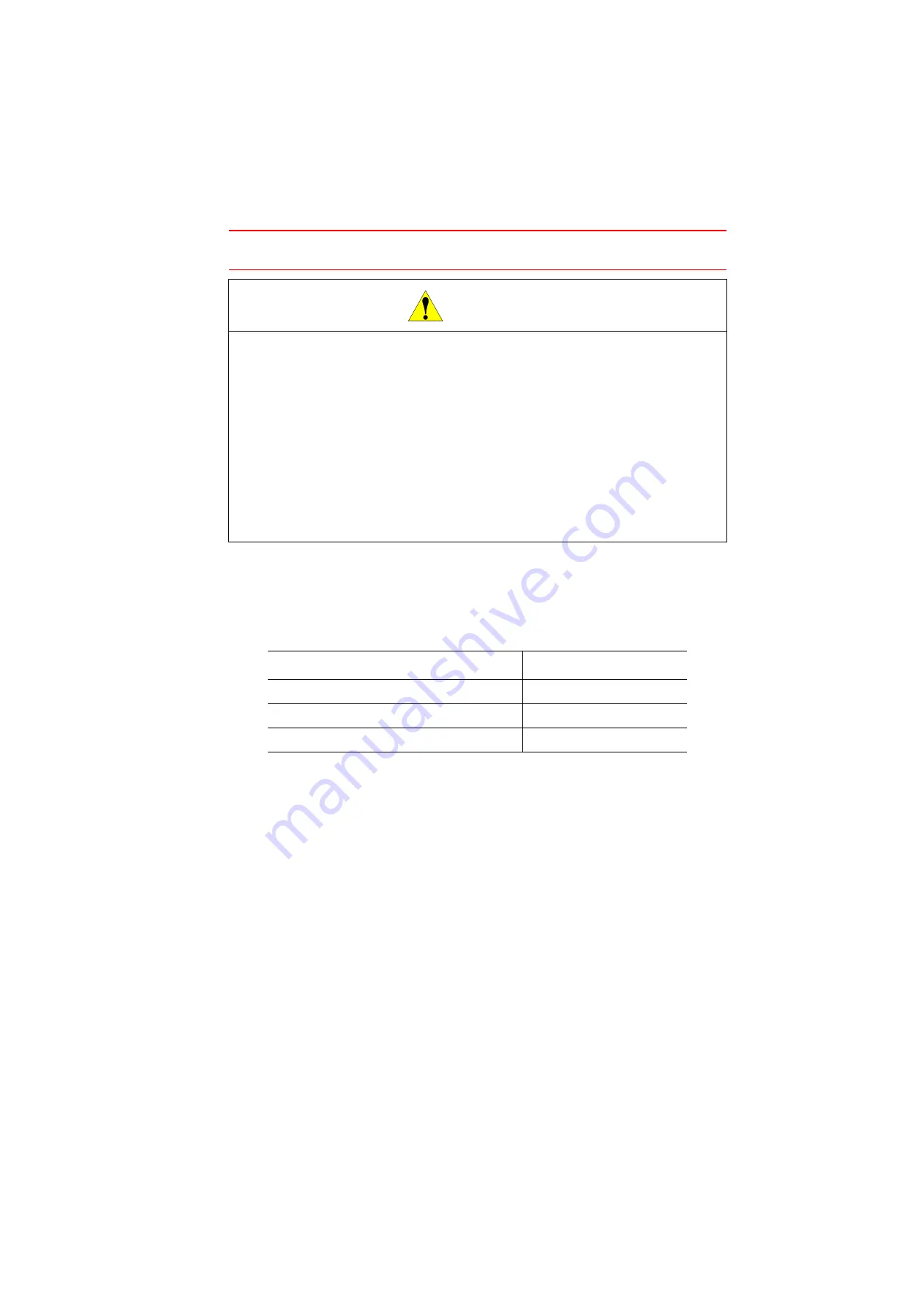
v
Definition of Terms Used Often in This Manual
The MOTOMAN manipulator is the YASKAWA industrial robot product.
The manipulator usually consists of the controller, the programming pendant, and supply
cables.
In this manual, the equipment is designated as follows:
• Perform the following inspection procedures prior to conducting manip-
ulator teaching. If problems are found, repair them immediately,
and be sure that all other necessary processing has been performed.
-Check for problems in manipulator movement.
-Check for damage to insulation and sheathing of external wires.
• Always return the programming pendant to the hook on the NX100 cabi-
net after use.
The programming pendant can be damaged if it is left in the P-point maximum envelope
of manipulator, on the floor, or near fixtures.
• Read and understand the Explanation of the Warning Labels in the
NX100 Instructions before operating the manipulator.
Equipment
Manual Designation
NX100 Controller
NX100
NX100 Programming Pendant
Programming Pendant
Cable between the Manipulator and the Controller
Manipulator Cable
CAUTION