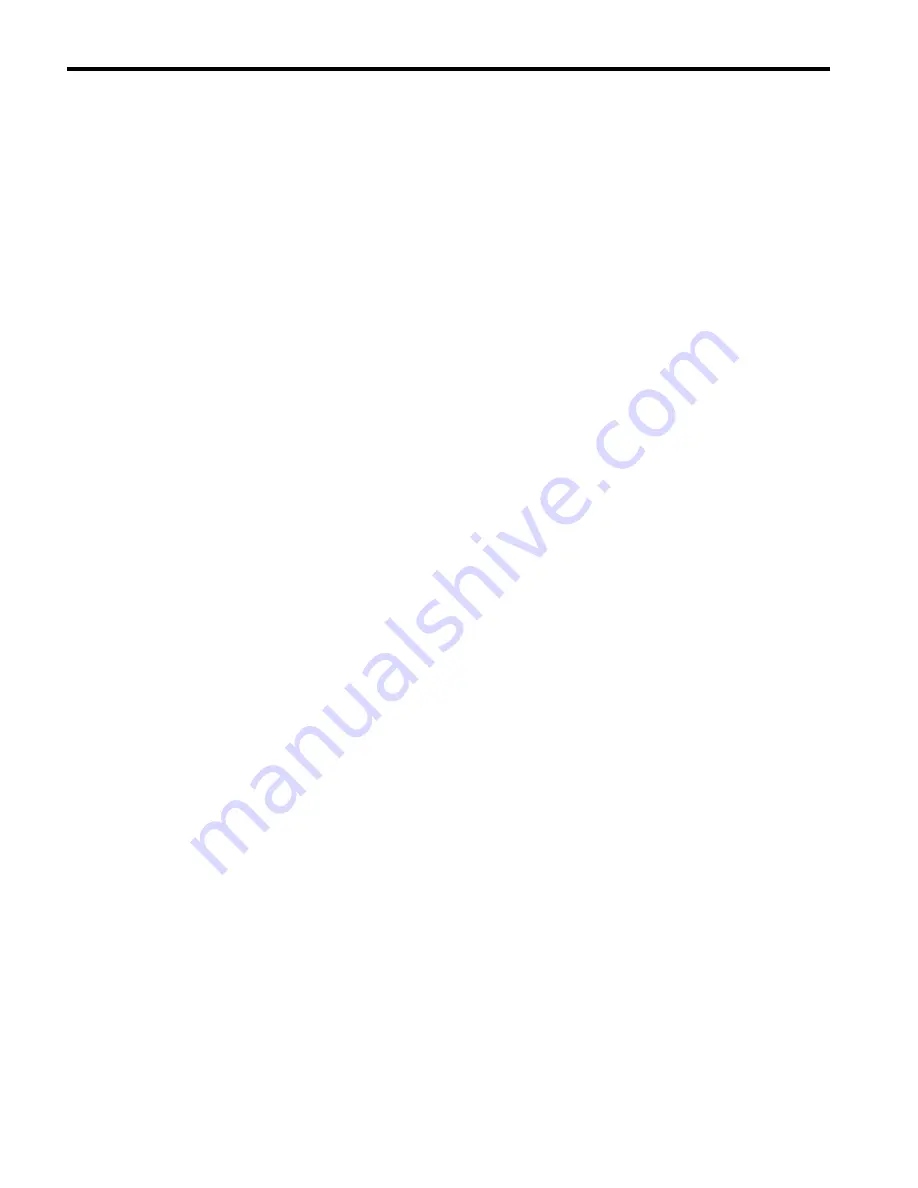
EN 2
YASKAWA ELECTRIC
TOEP C710606 15C - AC Drive V1000 - Quick Start Guide
Copyright © 2012
YASKAWA Electric Corporation.
All rights reserved. No part of this publication may be reproduced, stored in a retrieval sys-
tem, or transmitted, in any form, or by any means, mechanical, electronic, photocopying,
recording, or otherwise, without the prior written permission of YASKAWA. No patent lia-
bility is assumed with respect to the use of the information contained herein. Moreover,
because YASKAWA is constantly striving to improve its high-quality products, the informa-
tion contained in this manual is subject to change without notice. Every precaution has been
taken in the preparation of this manual. Nevertheless, YASKAWA assumes no responsibility
for errors or omissions. Neither is any liability assumed for damages resulting from the use
of the information contained in this publication