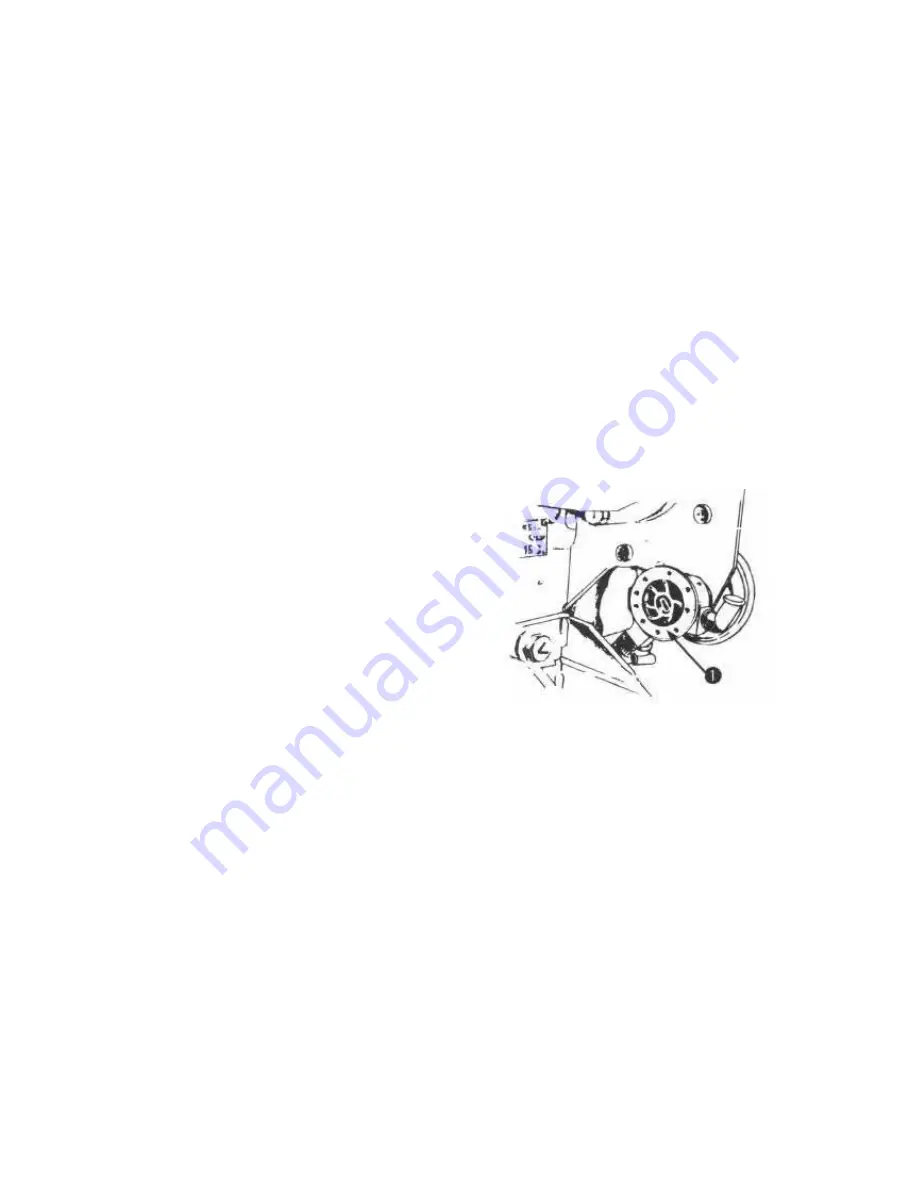
V III. Storage
[8-1.] Storing
Whenever the engine will not be used for several months, use the following procedure to
properly store it.
This minimizes corrosion and deterioration.
1) Drain fuel completely from fuel tank, otherwise moisture from the fuel system will mix
with the fuel.
2) Wash the cooling system with clean tap water and drain out the cooling water from the
engine completely.
2-a)
Cylinder body
2-b) Exhaust manifold.
2-c)
Cooling water pump Remove the cover of the
cooling water pump and drain out the water inside of
the cooling water pump.
3) Apply an anti-rust oil to any parts which rust
easily.
4) Since the battery will automatically discharge
itself if left, disconnect when fully charged, wash the
exterior and store in a dry, well-aired place.
Re-charge once a month during storage.
1. Cooling water pump
5) Tape to seal air inlet, exhaust pipe, and fuel tank cap.
6) Clean the engine throughly. Touch up any painted surfaces that are scratched or chipped.
7) If boat must be stored outside, cover it with waterproof material.
[82.] Removing engine from storage
1) Wipe off anti-rust oil and check that the remote control system move smoothly.
2) Wiring the battery.
2-a) Rewire as shown in the wiring diagram.
2-b) Make sure wires are connected to the correct terminals.
Summary of Contents for 1GM
Page 1: ...Yan...
Page 4: ......
Page 6: ......
Page 22: ...1 Dipstick 2 Empty 3 Full 1 Oil Supply Port 1 Oil Gauge Rod 2 Lower Limit 3 Upper Limit...
Page 26: ...1 Push Button DIRECTION OF ROTATION...
Page 37: ......
Page 38: ......
Page 54: ......
Page 55: ......
Page 56: ......