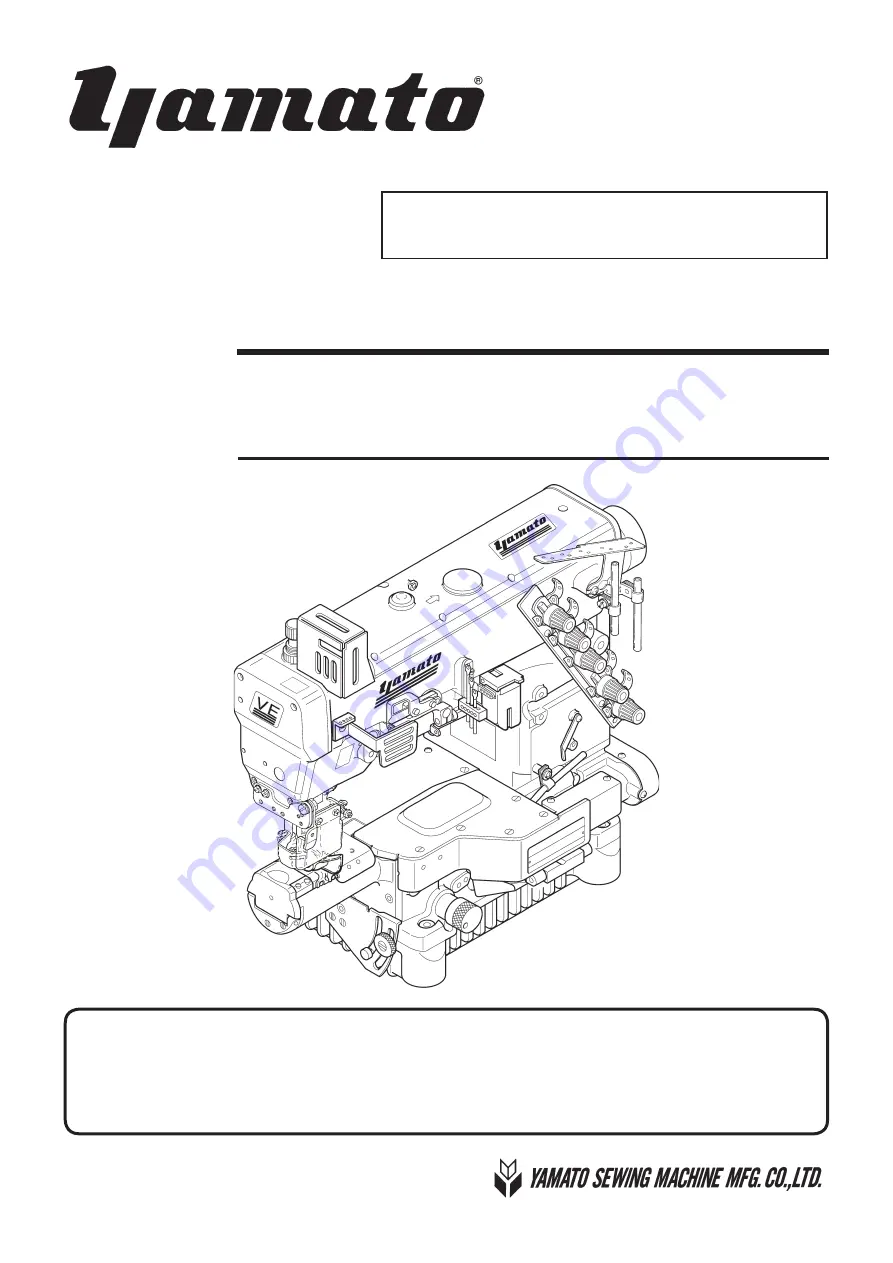
VE2711-1-8,VE2711-2-8F,VE2713-2-8F,VE2740PR-1-8F,VE2740PR-2-8F
VE2700-8 class
HIGH SPEED SMALL CYLINDER BED INTERLOCK STITCH MACHINE
Instruction Manual
Thank you for purchasing VE2700-8 class. Before using your VE2700-8 class, please read the
instruction manual and understand the contents well.
After reading the instruction manual, please keep it in a location where it is easily accessible
to the operator.