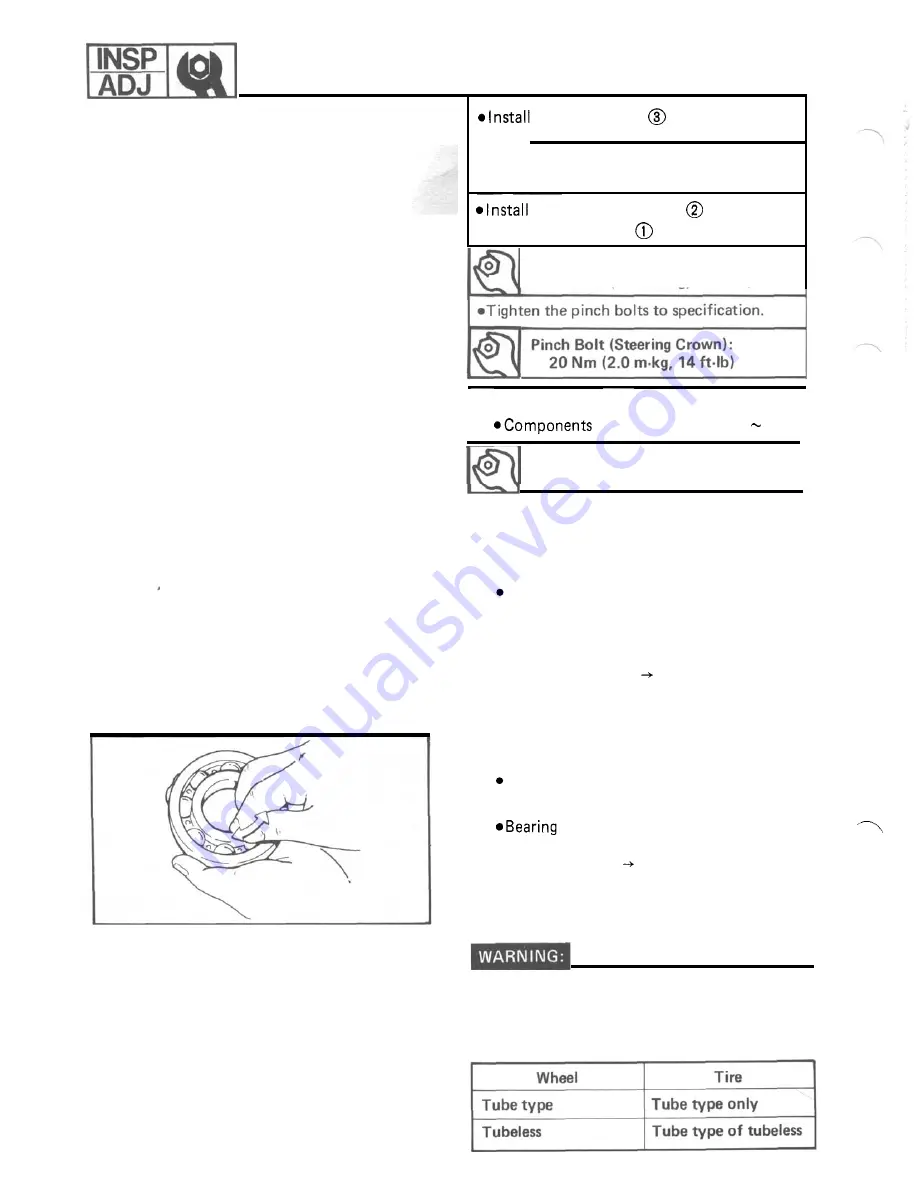
WHEEL BEARINGS CHECK/TIRES CHECK
2-31
the lock washer
.
NOTE:
Make sure the lock washer tab
is placed in
the slots.
the steering crown
and tighten
the steering stem nut
to specification.
Nut (Steering Stem) :
110
Nm
(11.0 m-kg, 80 ft-lb)
11. Install:
in above list (steps
"6
2")
I
Handlebar Lower Holder:
40 Nm (4.0
m-kg,
29 ft-lb)
WHEEL BEARINGS CHECK
Front Wheel
1. Check:
Front wheel bearings
Raise the front end of the motorcycle, and
spin the wheel by hand. Touch the axle or
front fender while spinning the wheel.
Excessivevibration
Replace bearings.
Rear
Wheel
1. Remove:
2. Check:
Rear wheel
movement
With the fingers.
Roughness/Wear
Replace.
TIRES CHECK
Do not attempt to use tubeless tires on a wheel
designed for tube type
tires
only. Tire failure
and personal injury may result from sudden
deflation.
Summary of Contents for VMX12H
Page 1: ...VMXl2N NC K KC...
Page 2: ...LIT 11616 10 12...
Page 22: ...VAMAHA MOTOR CO LTD PRINTEDI N U S A...
Page 23: ...E LIT 11616 08 77...
Page 44: ...CIRCUIT DIAGRAM ELECTRICAL CIRCUIT DIAGRAM I I 1...
Page 48: ...VAMAHA MOTOR CO LTD PRINTED IN U S A...
Page 49: ...I LIT I1616 06 08...
Page 56: ...TO IWATA JAPAN PRINTED IN U S A...
Page 57: ...LIT 1...
Page 64: ...IWATA JAPAN PRINTED IN U S A...
Page 65: ...I Serr ice L 1616 04 67...
Page 206: ...ENGINE ASSEMBLY AND ADJUSTMENT MEMO 3 82...
Page 304: ...CIRCUIT DIAGRAM I I ELECTRICAL CIRCUIT DIAGRAM w w 7 1...
Page 308: ...ELECTRIC STARTING SYSTEM I I ELECTRIC STARTING SYSTEM CIRCUIT DIAGRAM 7 5...
Page 320: ...CHARGING SYSTEM CHARGING SYSTEM CIRCUIT DIAGRAM 7 17...
Page 325: ...MEMO 7 22...
Page 326: ...IGNITION SYSTEM IGNITION SYSTEM CIRCUIT DIAGRAM 7 23...
Page 334: ...LIGHTING SYSTEM LIGHTING SYSTEM CIRCUIT DIAGRAM 7 31...
Page 339: ...MEMO 7 36...
Page 340: ...SIGNAL SYSTEM SIGNAL SYSTEM CIRCUIT DIAGRAM 7 37...
Page 348: ...COOLING SYSTEM COOLING SYSTEM CIRCUIT DIAGRAM 7 45...
Page 354: ...FUEL PUMP SYSTEM FUEL PUMP SYSTEM CIRCUIT DIAGRAM 7 51...
Page 362: ...V BO O ST SYSTEM V BO O ST SYSTEM CI RCUI T DI AG RAM...
Page 390: ...LUBRICATION DIAGRAMS LUBRICATION AGRAMS LUBRICATION DIAGRAM 8 20...
Page 391: ...LUBRICATION DIAGRAMS LUBRICATION DIAGRAM 2 8 21...
Page 392: ...LUBRICATION AGRAMS LUBRICATION DIAGRAM 8 22...
Page 393: ...LUBRICATION DIAGRAMS LUBRICATION DIAGRAM 4...
Page 401: ...CABLE ROUTING CANISTER PIPE ROUTING To carburetor To fuel tank TO Canister...
Page 403: ...m...