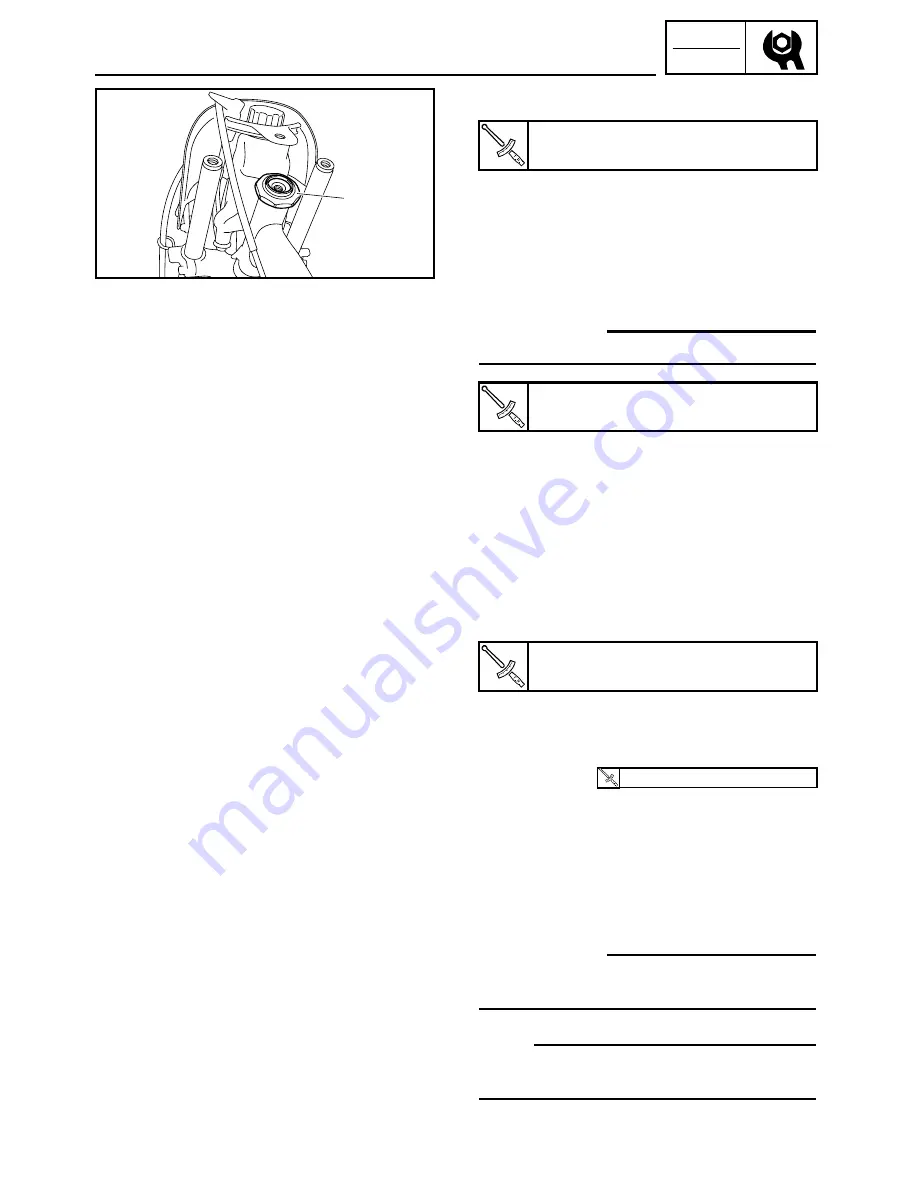
5
CHK
ADJ
3-15
CHECKING THE FRONT FORK
1. Stand the vehicle on a level surface.
w
Securely support the vehicle so that there
is no danger of it falling over.
NOTE:
Place the vehicle on a suitable stand so that
the front wheel is elevated.
CHECKING AND ADJUSTING THE STEERING HEAD/
CHECKING THE FRONT FORK
e. Check the steering head for looseness or
binding by turning the front fork all the
way in both directions. If any binding is
felt, remove the lower bracket and check
the upper and lower bearings. Refer to
“STEERING” in chapter 4.
f. Install the oil tank bracket, washer and
steering stem bolt, and then tighten the
steering stem bolt to specified torque.
▲▲▲▲▲▲▲▲▲▲▲▲▲▲▲▲▲▲▲▲▲▲▲
5. Install:
9
Washer
9
Cap bolt
9
Handle
9
Handle protector
Refer to “STEERING “in chapter 4.
b. Tighten the steering nut
5
with a wrench.
c. Lock to lock the steering head a few
times.
d. Fully loosen the steering nut and then
tighten the steering nut to specified
torque.
w
Do not over tighten the steering nut.
Steering nut (1st)
10 Nm (1.0 m·kg, 7.2 ft·lb)
Steering nut (2nd)
0.7 Nm (0.07 m•kg, 0.5 ft•lb)
Steering stem bolt
32 Nm (3.2 m•kg, 23 ft•lb)
32Nm (3.2 m•kg, 23 ft•lb)
5PG-7-10 45
06.5.16, 17:42:39
Summary of Contents for PW50W 2007
Page 1: ...SERVICE MANUAL 5PG 28197 10 LIT 11616 20 15 PW50W...
Page 2: ......
Page 8: ......
Page 165: ......
Page 166: ...YAMAHA MOTOR CO LTD 2500 SHINGAI IWATA SHIZUOKA JAPAN PRINTED IN U S A...