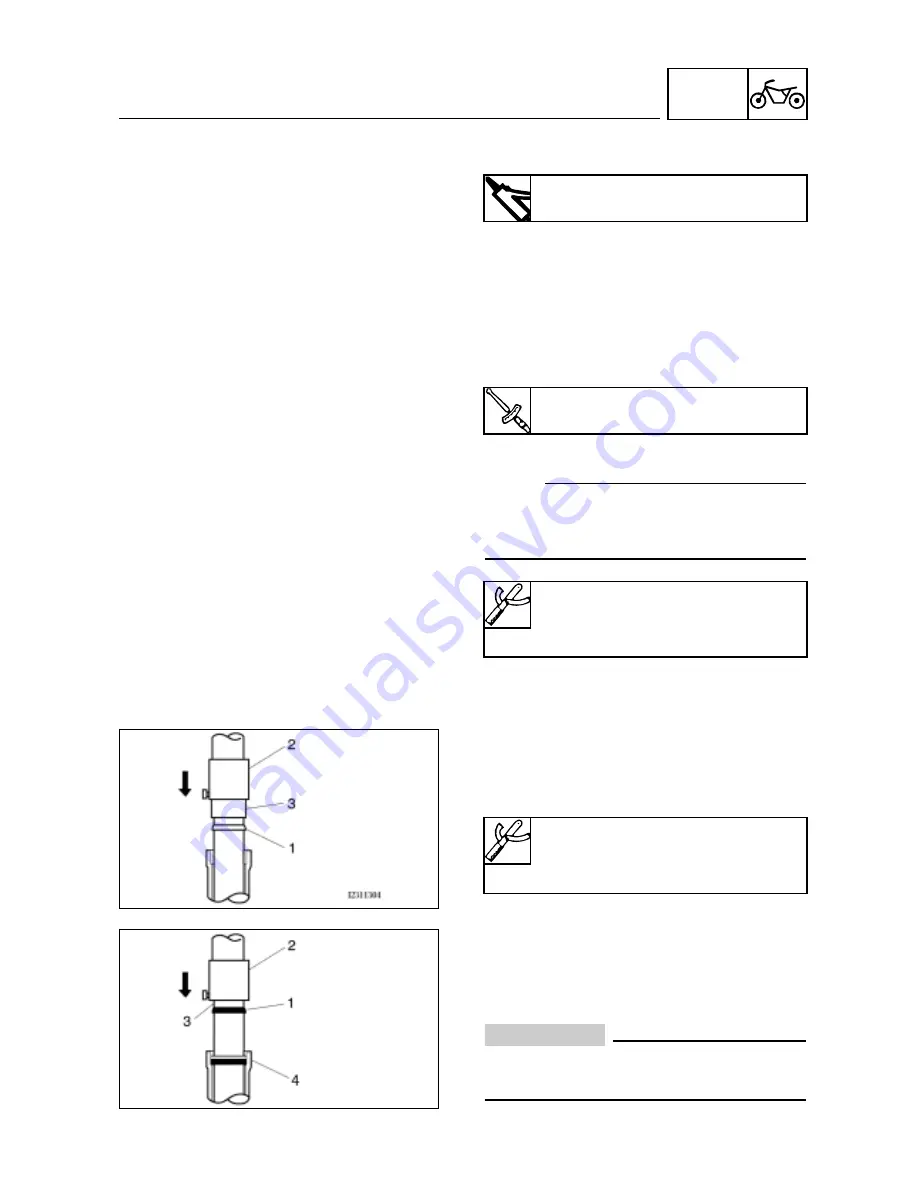
CHAS
ASSEMBLING THE FRONT FORK LEGS
4-42
2. Lubricate:
• inner tube’s outer surface
3. Tighten:
• damper rod assembly bolt
NOTE:
While holding the damper rod assembly with
the damper rod holder and T-handle, tighten
the damper rod assembly bolt.
4. Install:
• outer tube bushing
(with the fork seal driver weight and fork
seal driver attachment)
5. Install:
• washer
• oil seal
(with the fork seal driver weight and fork
seal driver attachment)
CAUTION
Make sure the numbered side of the oil seal
faces up.
Recommended lubricant
Fork oil 10W or equivalent
62 Nm (6.2 m•kg, 45 ft•lb)
LOCTITE®
Damper rod holder
90890-01388
T-handle
90890-01326
Fork seal driver weight
90890-01367
Fork seal driver attachment
90890-01381
Summary of Contents for DT125RE 2005
Page 1: ...SERVICE MANUAL DT125RE1D01 AE1 DT125X 2005 ...
Page 7: ...GEN INFO ...
Page 8: ...1 ...
Page 16: ......
Page 17: ...SPEC ...
Page 18: ...2 ...
Page 39: ...CHK ADJ ...
Page 40: ...3 ...
Page 86: ...CHAS ...
Page 87: ...4 ...
Page 160: ...ENG ...
Page 161: ...5 ...
Page 223: ...COOL ...
Page 224: ...6 ...
Page 239: ...CARB ...
Page 240: ...7 ...
Page 255: ...ELEC ...
Page 256: ...8 ...
Page 263: ...ELEC IGNITION SYSTEM 8 6 IGNITION SYSTEM The circuit diagram showns the ignition system ...
Page 270: ......
Page 282: ......
Page 307: ...TRBL SHTG ...
Page 308: ...9 ...
Page 319: ...DT125 WIRING DIAGRAM ...