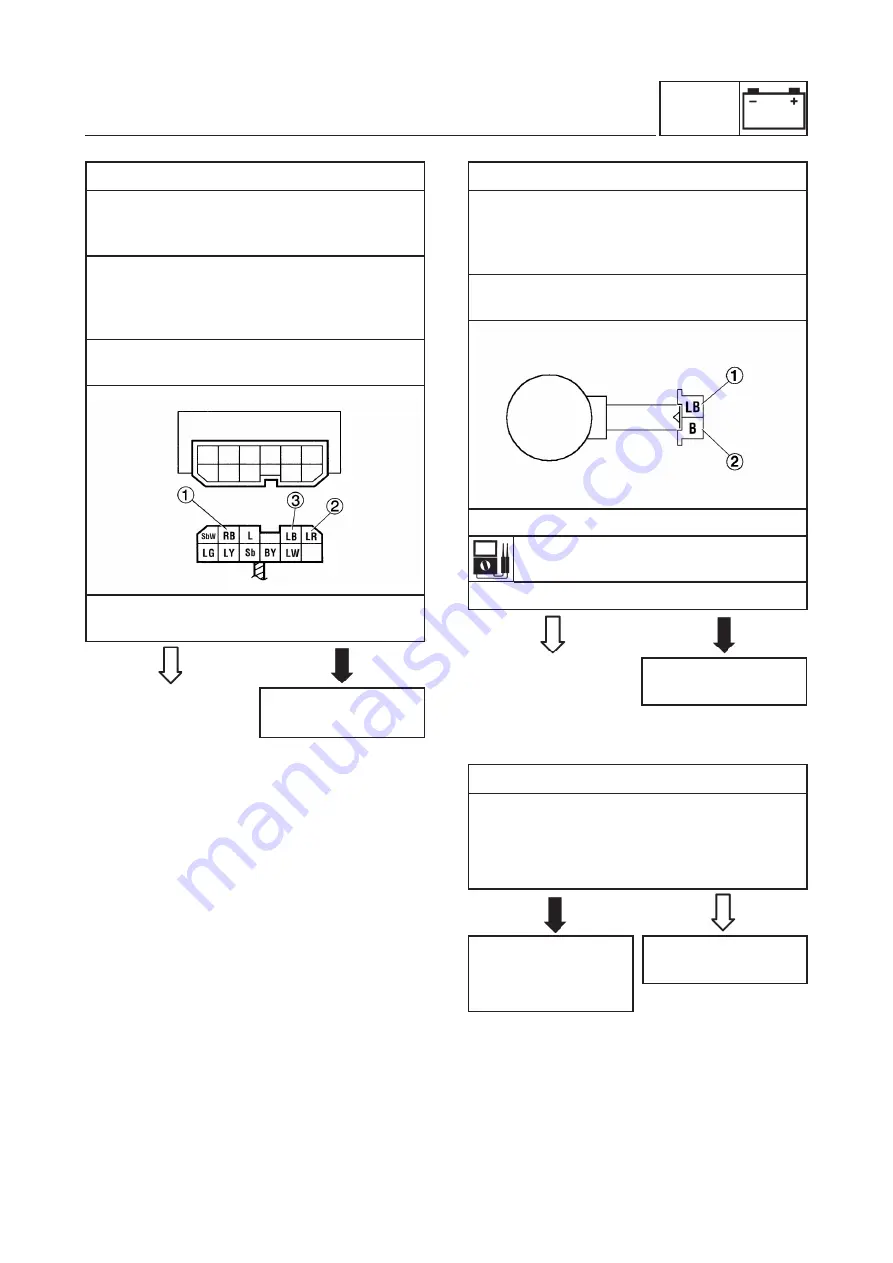
102
ELEC
FUEL PUMP SYSTEM
Replace the fuel
pump.
YES
NO
6. Fuel pump resistance
• Disconnect the fuel pump coupler from the
wire harness.
• Connect the pocket tester (
1) to the fuel
pump coupler terminals.
Tester (+) lead
→
Blue/Black terminal
1
Tester (–) lead
→
Black terminal
2
• Measure the fuel pump resistance.
Fuel pump resistance:
1.6 ~ 2.2
at 20 °C (68 °F)
Is the fuel pump OK?
EB808021
7. Wiring
• Check the entire fuel pump system’s wiring.
Refer to "CIRCUIT DIAGRAM".
• Is the fuel pump system’s wiring properly
connected and without defects?
Replace the ignitor
unit.
Properly connect or
repair the fuel pump
system’s wiring.
NO
YES
5. Starting circuit cutoff relay (fuel pump relay)
• Remove the relay unit from the wire harness.
• Connect the pocket tester (
1) and bat-
tery (12 V) to the relay unit terminals.
Battery (+) terminal
→
Red/Black terminal
1
Battery (–) terminal
→
Blue/Red terminal
2
Tester (+) lead
→
Red/Black terminal
1
Tester (–) lead
→
Blue/Black terminal
3
• Does the fuel pump relay have continuity
between Red/Black and Blue/Black?
EB803023
Replace the starting
circuit cutoff relay.
YES
NO