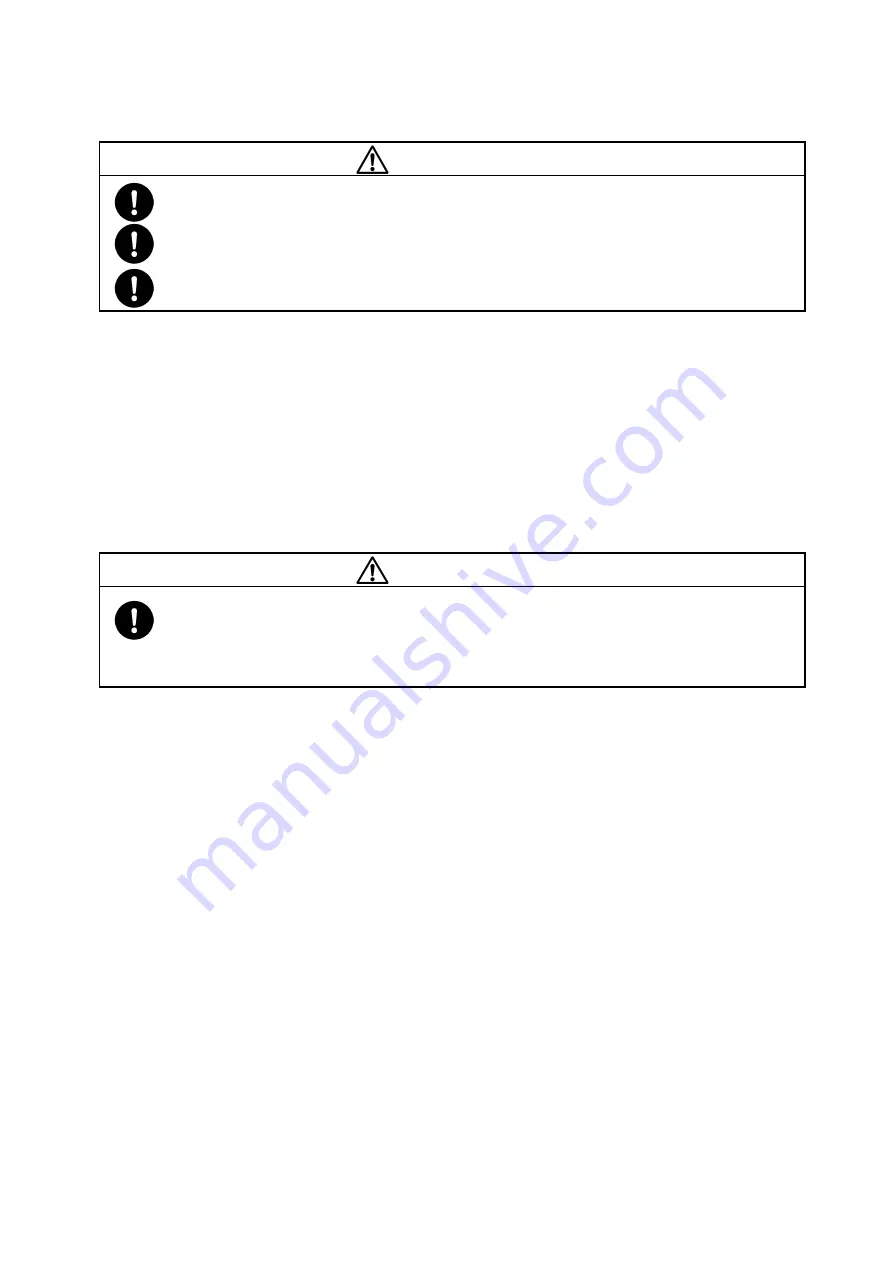
13
4.
Operation
4.1 Method of operation
CAUTION
- Before starting the pump, make sure that all piping is properly connected.
- Also, before starting the pump, make sure that all the bolts are securely tightened.
- Make sure that the air valve, regulator and the drain valve on the discharge side are closed.
Also, make sure that the valve on the suction side is opened.
1) Start the air compressor. Use dry compressed air.
2) Open the air valve in front of each piece of peripheral equipment, and adjust the supply air
pressure with a regulator to within the permissible range (0.4-0.7MPa).
3) Turn the closed needle valves (5 pcs) to the right about 30 degrees. Adjust the valves if the air
volume is not enough at this time.
4) Press the RESET button, and then slowly open the air valve of the pump.
5) First, verify that material is flowing inside the piping and is being pumped to the discharge side,
and then fully open the air valve.
4.2 Shutdown
- Close the air valve of the pump and shut off the supply air.
CAUTION
- After the pump shuts down, powder material will precipitate and get stuck in the out
chambers. Restarting the pump in such condition may result in damage to the diaphragms
or overload of the center disks, causing the center rod to bend.
Be sure to run the pump dry to remove the residual material from the inlet/outlet hoses, out
chambers, and piping at the end of work.