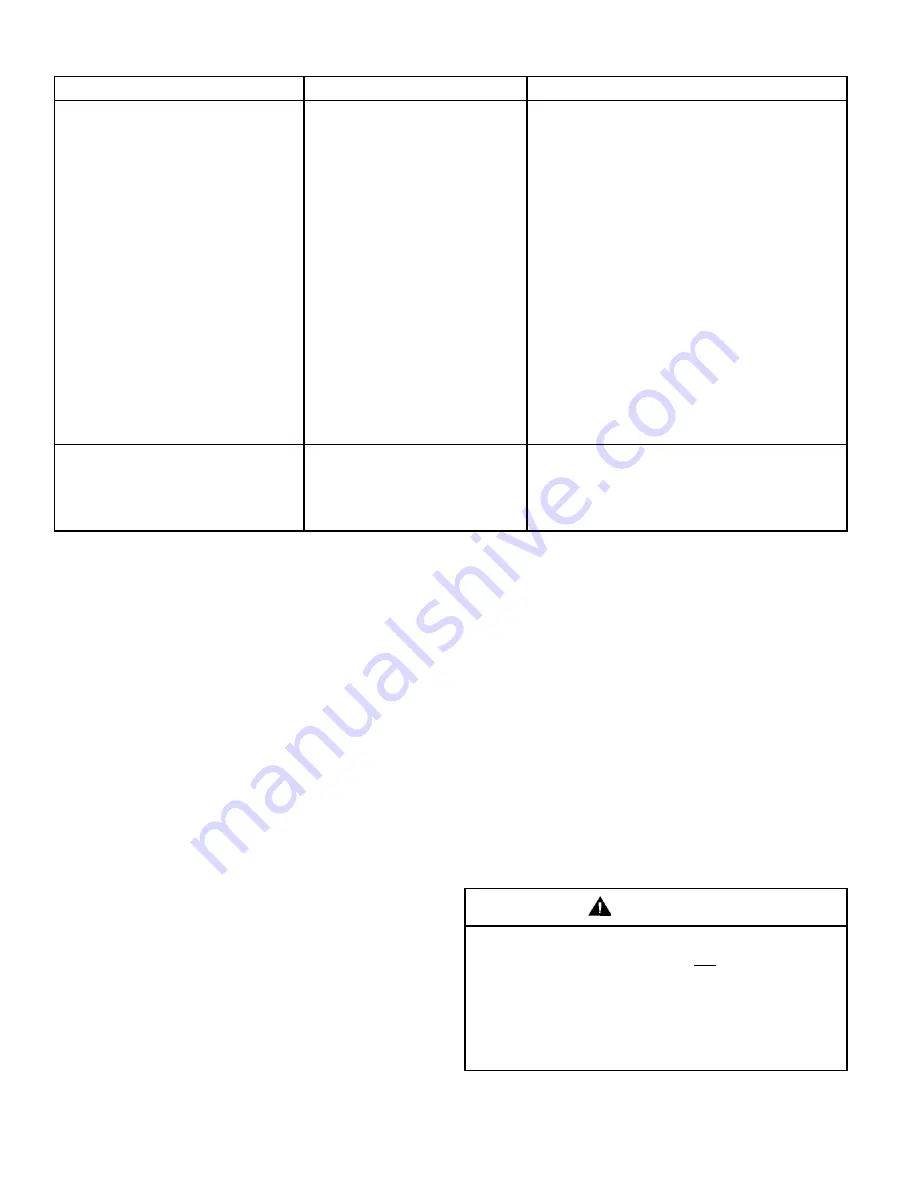
Page 22
SECTION Vl - TROUBLE SHOOTING (continued)
Trouble
Probable Cause
Possible Remedy
6-7. Hoist Motor Overheats
a. Excessive load.
a. Reduce loading to rated load of hoist,
shown on nameplate.
b. Excessive duty-cycle
b. Reduce frequency of lifts or amount of
jogging.
c. Wrong voltage or frequency.
c. Check current rating on motor data plate
against power supply.
d. Defective motor or worn
d. Disassemble hoist and inspect for defective,
bearings in hoist frame.
worn or damaged parts.
e. Overload clutch slipping
e. Adjust clutch per SECTION VII, Paragraph
without lifting load.
7-5.
f. Motor brake actuating
f. (1) Disassemble actuating mechanism and
mechanism sticking.
inspect for defective work or damaged
parts. (2) Check voltage to brake coil at
brake controller. Brake control with solenoid
connected provides a 100 volt DC pulse to
the solenoid for 1 /10 of a second, after
which time this voltage drops to 10 volts
DC ± 5 volts.
6-8. Hoist Operates Intermittently.
a. Collectors make poor contact.
a. Check collectors for free movement of
spring arm, weak spring or electrical
connections.
b. Loose connections.
b. Check all wiring for loose connections.
SECTION VII - ADJUSTMENTS
7-1. MECHANICAL LOAD BRAKE. The mechanical load brake
on SHAW-BOX hoists is a roller ratchet “Weston” type automatic
brake. The brake is not adjustable and requires only periodic
inspection and occasional replacement of the friction washers.
7-2. MOTOR BRAKE ADJUSTMENT. These brakes are
designed so that adjustment is seldom required. If, after a
period of service, the load hooks “drifts” downward more than
usual for your hoist before coming to a stop, the motor brake
may require adjustment to compensate for brake disc wear.
In addition to the adjustment instructions below motor brake
adjustment instructions may also be found inside the brake
cover. Refer to Figure 9-6 and proceed as follows:
a. Remove one hex socket button head cap screw
from brake cover and then remove brake cover.
b. Loosen set screw at gearcase cover (Ref. No. 1 in Figure
9-6).
c. Turn brake actuating assembly, by hand, until brake
adjustment indicator pin (Ref. No. 10) is flush with the
end of the body assembly (Ref. No. 9).
d. Retighten set screw.
Note: Do not overtighten set screw. Damage to actuator
or gearcase cover threads may occur.
e. Replace brake cover.
f. Operate hoist and brake to assure brake is free when
disengaged. If brake is dragging, loosen brake actuating
assembly by 1/8 turns until brake action is proper.
g. If, after above adjustment, the load hook continues to
“drift” downward more than normal for this hoist, make a
complete inspection of motor brake mechanism including
friction surfaces. See SECTION V, Paragraph 5-5.
7-3. BLOCK OPERATED LIMIT SWITCH. The block operated
limit stop, furnished as standard equipment, is nonadjustable
and designed to stop lower block at safest high point of travel
to eliminate any possibility of doubleblocking. When the safest
high point is reached, the limit switch automatically stops hook
travel.
Some hoists are shipped with the electrical controls
loose (disconnected) and will not have the upper
and lower limit switches connected. DO NOT
OPERATE HOIST UNTIL LIMIT SWITCHES ARE
PROPERLY CONNECTED AND ADJUSTED. Failure to
do so may allow hoist to be operated beyond proper
travel limits which can cause load to drop, resulting
in damage to equipment or injury.
WARNING
Summary of Contents for SHAW-BOX
Page 66: ...NOTES ...
Page 67: ...NOTES ...