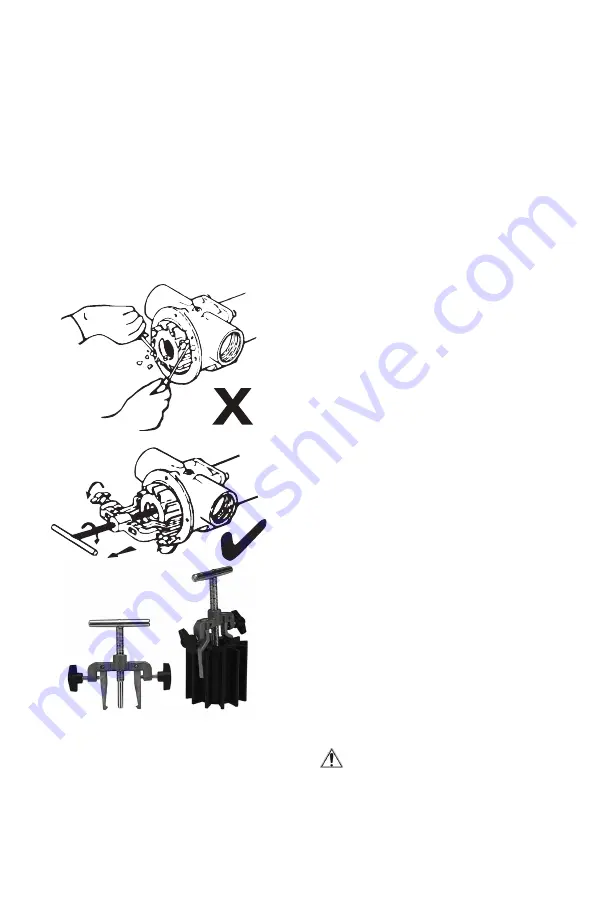
4
PUMP ASSEMBLY AND DISASSEMBLY
1. Disassembly
• Remove the end cover screws and remove the
end cover and o-ring.
• Use Jabsco impeller removal tool
P/N: 50070-0040.
• Remove the first impeller using a Jabsco
impeller removal tool, shown below.
• Remove the second impeller using a Jabsco
impeller removal tool, shown below.
• Remove the screws holding the body to the
motor.
• Remove the lip seal from the body.
• Do not disassemble the motor.
2. Assembly
• Moisten the new lip seal, and press the seal
into location with the lip facing the front of
the pump body. The impeller will not be in
location when the lip seal installed.
• Lubricate the motor shaft and fit the body to
the motor by tightening the motor screws.
• Ensure the body and impeller are lubricated.
WARNING!
When terminated at the power supply
using permanent connections, red leads
should be terminated to the positive and
black to the negative. If reversed pump
will run in reverse.
• Fit the impeller with a rotating movement in
the intended direction of the pump rotation.
• Lubricate the o-ring with water, fit it in position
and fasten the end cover screws to the body.
• Torque value for end cover to body screws:
30– 40 lbf.ins / 3.4 – 4.5 Nm.
• Torque value for body to motor screws:
21 – 28 lbf.ins / 2.4 – 3.1 Nm.
ELECTRICAL CONFIGURATION
AND INSTALLATION
• 33710-0107 configured with Deutsch DTP04-
2P connector, Pin 1 - Positive, Pin 2 - Negative.
• It is the responsibility of the installer to per-
form the correct installation.
• Make all electrical connections in dry loca-
tions, connections in humid environments
should be sealed to prevent corrosion.
• Protect the circuit with a correctly rated fuse
or circuit breaker in the red positive (+) lead
as close as possible to the power source (see
page 6 for recommended fuse).
• Ensure fuses for the Ballast SuperKing pump
are slow burning, being capable of handling
the start-up and reversing current.
• Connect the black motor wire to the negative
(-) battery terminal.
• Inadequate voltage at the motor terminals
when the pump is running (no less than 95%
of rated voltage at full load) due to partially
discharged batteries or insufficient cable size
may result in blowing fuses, failure to start or
poor pump performance.
• The motor is equipped with built in thermal
protection to prevent it from over-heating.
• Power is automatically restored when the
motor is cooled.
• Ensure the vessel’s ballast control system is
rated to accept the amperage draw of motor
prior to installation.
• Choose the wire size in accordance with total
wire length per ABYC.
• All Ballast SuperKing wiring and connections
to be carried out in accordance to ISO 10133.