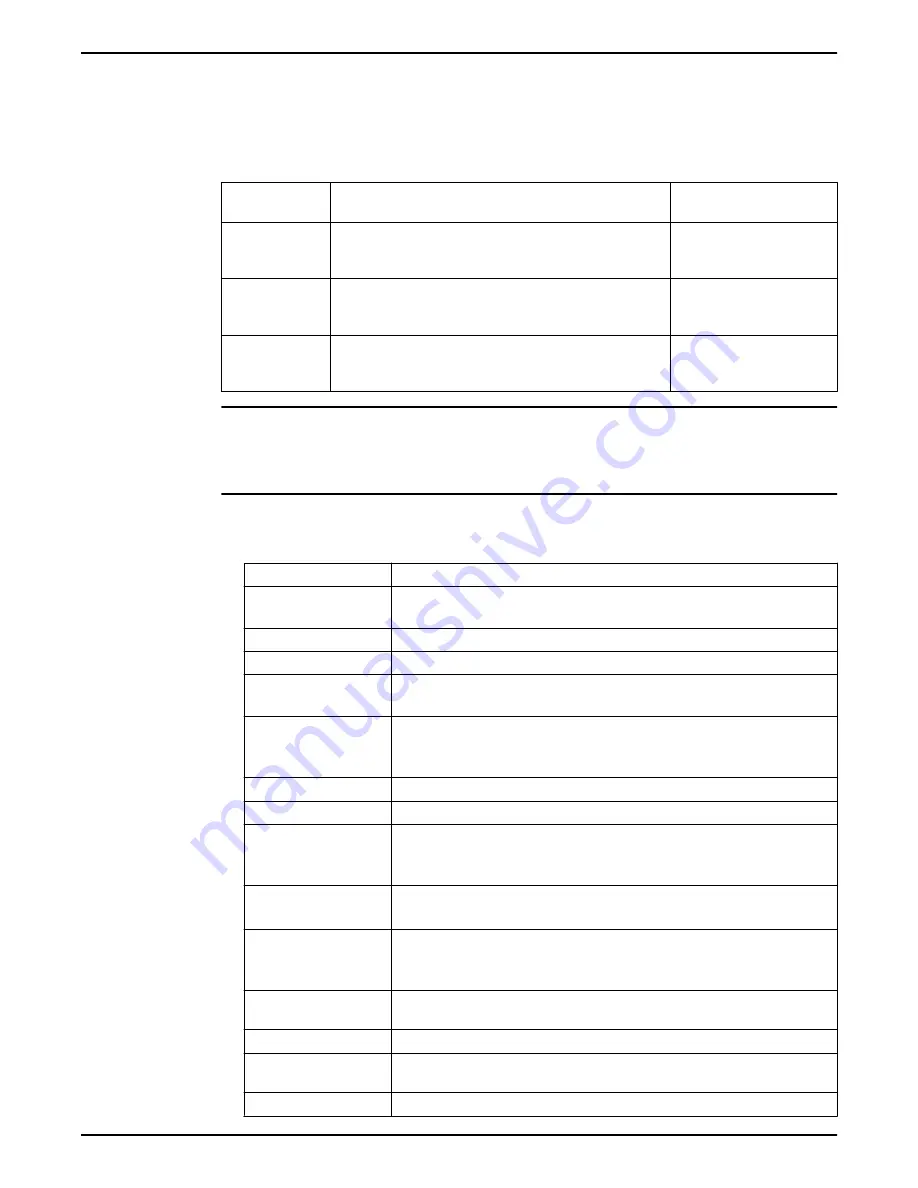
Hexagon screws with countersunk heads
For hexagon socket head screws with countersunk head, maximum torque for all property
classes must be 80% of the values for property class 8.8 above.
7.2 Maintenance intervals
Type of
maintenance
Purpose
Inspection interval
Initial inspection
A Xylem-authorized personnel checks the pump condition.
From the results, the personnel recommends the intervals for
the periodical inspection and overhaul for the installation.
Within the first year of
operation.
Periodical
inspection
The inspection prevents operational interruptions and machine
breakdowns. The measures to increase performance and pump
efficiency are decided for each application.
Up to 12,000 hours or three
years, whichever comes first.
Overhaul
The overhaul lengthens the operating lifetime of the product. It
includes the replacement of key components and the measures
that are taken during an inspection.
Up to 24,000 hours or six
years, whichever comes first.
NOTICE:
Shorter intervals may be required when the operating conditions are extreme, for
example with very abrasive or corrosive applications or when the liquid temperatures
exceed 40°C (104°F).
7.2.1 Inspection
The list is valid for initial inspection and periodical inspection.
Service item
Action
Cable
1. If the outer jacket is damaged, replace the cable.
2. Check that the cables do not have any sharp bends and are not pinched.
Electrical connections
Check that the connections are properly secured.
Electrical cabinets
Check that they are clean and dry.
Impeller
1. Check the clearance.
2. If necessary, adjust.
Stator housing
Drain any liquid.
For more information, see
Drain the liquid from the stator housing
page 38.
Level regulators
Check the condition and functionality.
Lifting device
Check that the local safety regulations are followed.
Lifting handle
1. Check the screws.
2. Check the condition of the lifting handle and the chain.
3. If necessary, replace.
Oil
If necessary, fill with new oil.
For more information, see
on page 39.
O-rings
1. Replace the O-rings of the oil plugs.
2. Replace the O-ring of the inspection plug.
3. Lubricate the new O-rings.
Overload protection and
other protections
Check the correct settings.
Personnel safety devices
Check the guard rails, covers, and other protections.
Thermal contacts, for Ex-
approved versions
Normally closed circuit; interval 0–1 ohm.
Voltage and amperage
Check the running values.
7 Maintenance
6020.180/090 Installation, Operation, and Maintenance Manual
37
Summary of Contents for FLYGT Concertor
Page 1: ...Installation Operation and Maintenance Manual 886211_9 0 6020 180 090 Concertor...
Page 2: ......
Page 58: ......
Page 59: ......