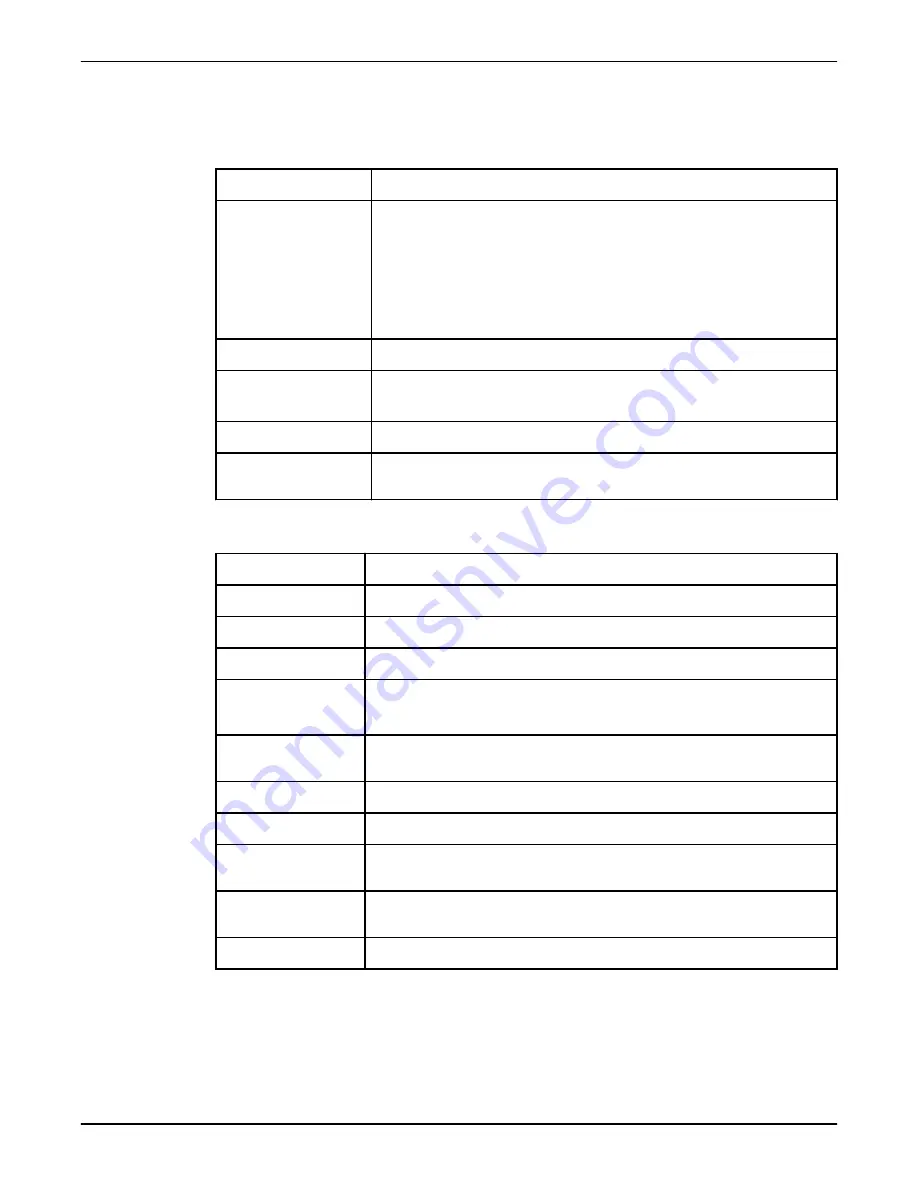
Technical reference
Application limits
Data
Description
Liquid temperature
40°C (104°F) maximum
If the pump is not equipped with cooling jacket, the pump can be operated at full
load only if at least half the stator housing is submerged.
Warm-liquid version: 90°C (195°F) maximum
At increased temperatures, the pump must be completely submerged when
operating at full load.
Ex-approved pumps: 40°C (104°F) maximum
Liquid density
1100 kg/m³ (9.2 lb per US gal) maximum
pH of the pumped media
(liquid)
5.5–14 for cast iron pumps
3–14 for stainless steel pumps
Depth of immersion
20 m (65 ft) maximum
Other
For the specific weight, current, voltage, power ratings, and speed of the pump, see
the data plate of the pump.
Motor data
Feature
Description
Motor type
Squirrel-cage induction motor
Frequency
50 or 60 Hz
Supply
1-phase or 3-phase
Starting method
• Direct on-line
• Star-delta
Maximum starts per
hour
30 evenly spaced starts per hour
Code compliance
IEC 60034-1
Rated output variation
±5%
Voltage variation without
overheating
±10%, provided that it does not run continuously at full load.
Voltage imbalance
tolerance
2%
Stator insulation class
H (180°C [360°F]).
Technical reference
44
Flygt 3201 Installation, Operation, and Maintenance Manual
Summary of Contents for Flygt 3201
Page 1: ...Flygt 3201 Installation Operation and Maintenance Manual...
Page 2: ......
Page 47: ......