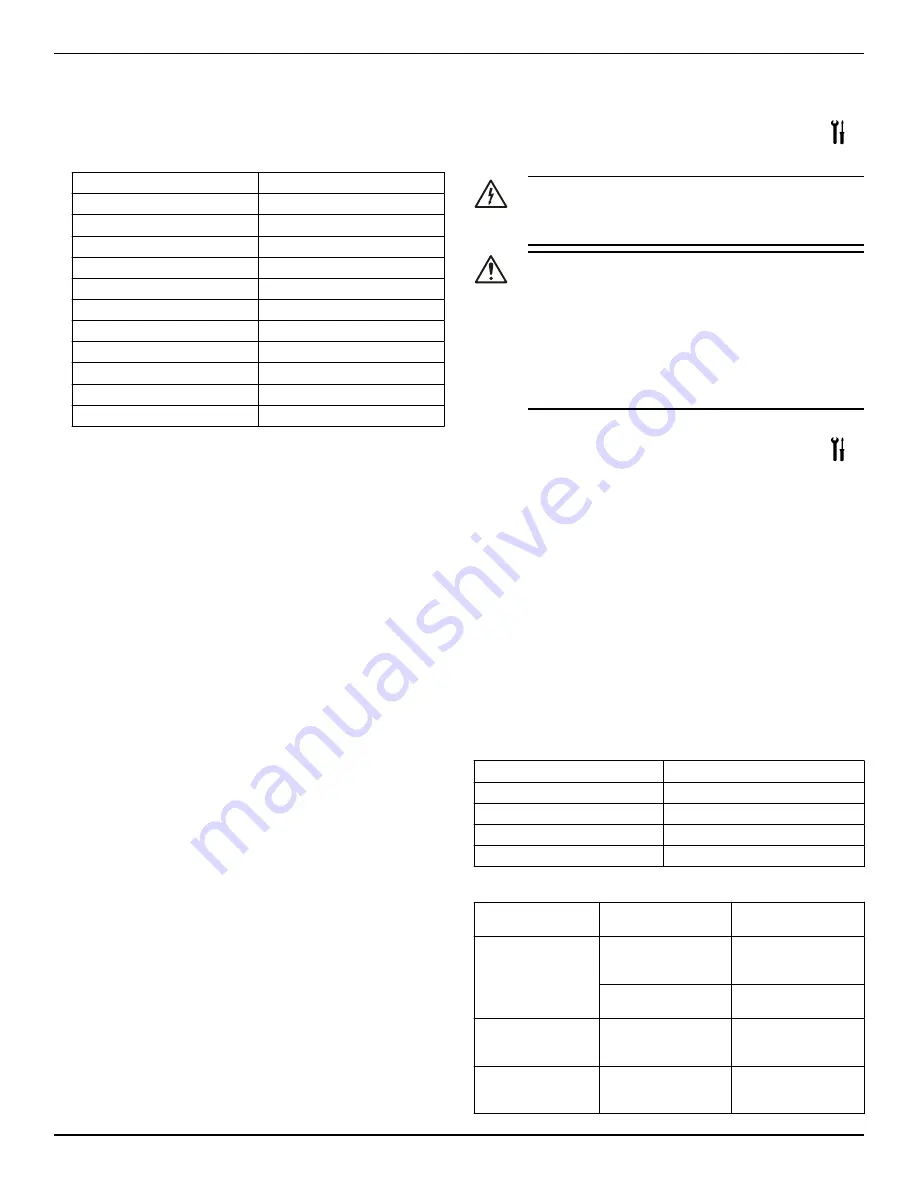
– Switch on power to supply the pump.
– Close the start/stop contact by jumpering terminals 11 and 12
on single phase pumps and terminals 13 and 14 for three phase
pumps, or through a remote dry contact..
– Send start command through the communication bus.
The pump starts pumping in constant pressure mode with the fol-
lowing default set points:
Default set points
Pump models
7.5 ft
15–XX (Max head 15 ft)
10 ft
20–XX (Max head 20 ft)
13.5 ft
27-XX (Max head 27 ft)
18 ft
36–XX (Max head 36 ft)
20 ft
40–XX (Max head 40 ft)
22.5 ft
45-XX (Max head 45 ft)
27.5 ft
55–XX (Max head 55 ft)
32.5 ft
65–XX (Max head 65 ft)
35 ft
70-XX (Max head 70 ft)
47.5 ft
95–XX (Max head 95 ft)
55 ft
110–XX (Max head 110 ft)
For more information about how to change setting, see
Configure
the pump settings
on page 12.
• Stop the pump in one of the following ways:
– Switch off power supply to the pump.
– Open the start/stop contact.
– Send stop command through the communication bus.
6.2.1 Automatic air venting procedure
At each power-on of the pump unit, an automatic air venting proce-
dure is executed. During this phase, the user interface displays "deg"
(degassing) and a count-down begins until the completion of the pro-
cedure.
The air venting procedure can be recalled or skipped:
• Manually by pressing simultaneously the two buttons (5). See
User
interface
on page 9. The feature will remain disabled until power to
pump is disconnected.
The procedure can be permanently enabled or disabled by:
• Manually by pressing simultaneously the two buttons (5) for at least
10 seconds. See
User interface
on page 9. Or
• Via communication bus. See the electronic drive manual on
www.bellgossett.com.
6.2.2 Two pumps in parallel configuration setup
The circulators are configured as single units by factory default. To acti-
vate the two pump parallel functions, follow the procedure below only
on one of the two pumps. The second pump will be automatically con-
figured. The working modes are described in
Automatic two pumps in
parallel operation
on page 11.
6.2.3 Set automatic operation mode on two pumps in
parallel
Once the communication cable is connected, configure only the “lead”
pump. The two pump submenu for this configuration is available at
each power-on. When the drive is displaying SING (which stands for
“Single Pump) short press one of the settings button (5) to display two
pumps in parallel menu.
The following procedure must be executed during the start-up phase
of the pump.
1. Enter the two-pump sub menu when the display is showing TWMA
(two-pump master) or TWSL (two-pump slave).
2. Select the applicable two-pump operation.
– bcup = backup operation
– alte = alternative operation
– para = automatic parallel operation
– forc = forced parallel operation
3. Push the parameter button (3) to accept the new setting.
The second pump is configured automatically by the lead pump. Refer
to Electronic Drive Manual for further details.
7 Maintenance
Precaution
Electrical Hazard:
Disconnect and lock out electrical power before installing or
servicing the unit.
Wait 2 minutes before opening the conduit box.
WARNING:
• Always wear protective gloves when handling the pumps
and motor. When pumping hot liquids, the pump and its
parts may exceed 40°C (104°F).
• Maintenance and service must be performed by skilled
and qualified personnel only.
• Observe accident prevention regulations in force.
• Use suitable equipment and apply personal protection.
• Risk of property damage, serious personal injury or death.
You must repair or replace the pump if corrosion or leak-
age is found.
8 Troubleshooting
8.1 Introduction
See
User interface
on page 9.
• In case of any alarm that allows the pump to continue running, the
display shows a blinking alarm code and the last quantity selected,
while the status indicator (8) becomes orange.
• In case of a failure that stops the pump, the display shows the error
code permanently lit and the status indicator (8) becomes red
8.2 Periodic inspection
Bell & Gossett ecocircXL circulators are designed to provide years of
trouble-free service. It is recommended that periodic inspections be
made to check for potential problems with the pump. If any leakage or
evidence of leakage is present, repair or replace the unit.
8.3 Display messages
Table 2: Default
Operating LEDs / Display
Cause
Power On
Pump powered
All LEDs and display On
Start-up of the pump
Status Green light
Pump is working properly
Remote On
Remote communication is activated
Table 3: Fault messages
Operating LEDs / Dis-
play
Cause
Solution
Power Off
Pump is not connected
or is incorrectly con-
nected
Check power connec-
tion
Power failure
Check power supply
and circuit breaker
Status light Orange
Alarm for system prob-
lem
Check the displayed
alarm code and find
cause from table 8.4.
Status light Red
Pump failure
Check the displayed
error code and find the
cause from table 8.3.
7 Maintenance
ecocirc
®
XL INSTRUCTION MANUAL
13
Summary of Contents for ecocirc XL
Page 1: ...INSTRUCTION MANUAL P2002548 Rev E Single Phase Pump Three Phase Pump ecocirc XL...
Page 2: ......
Page 19: ......