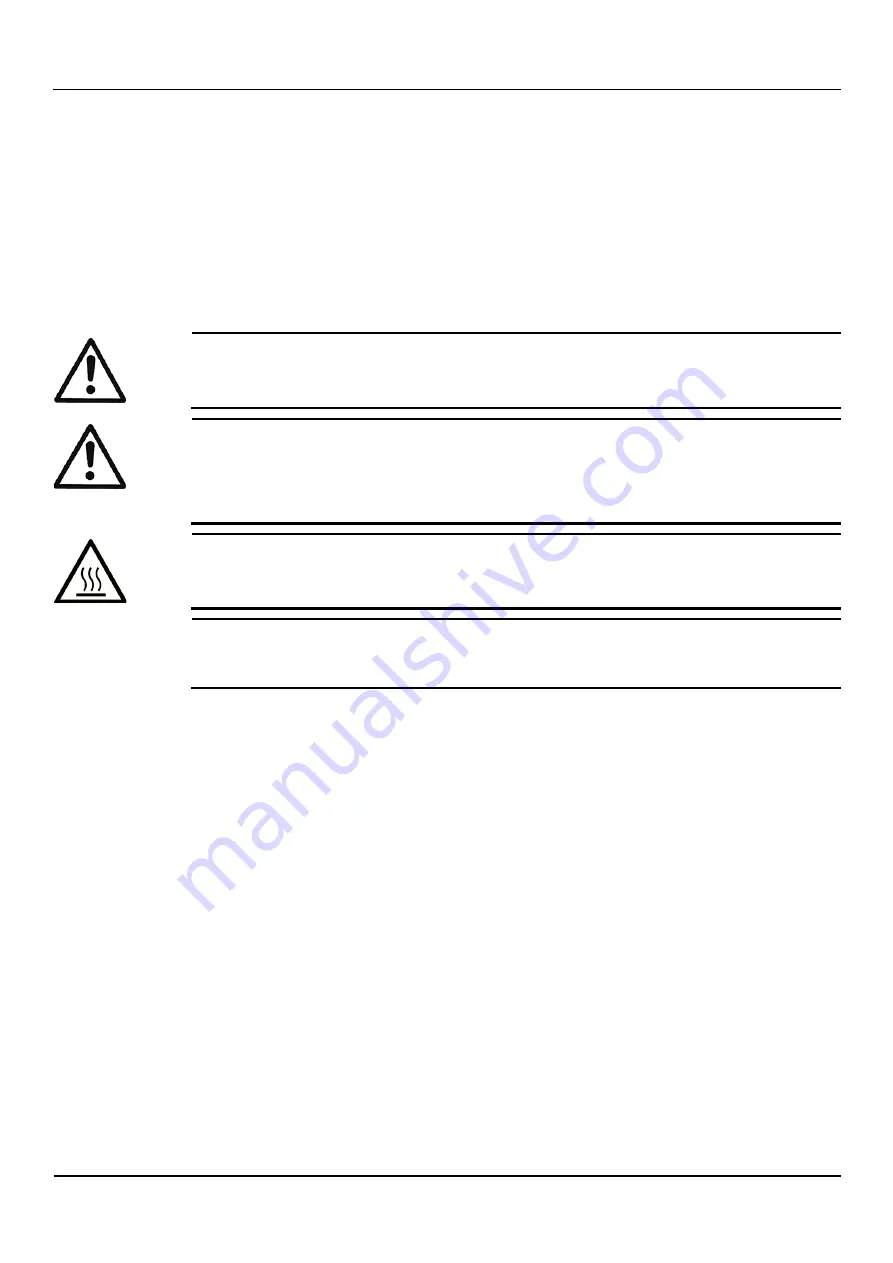
en – Original Instructions
e-IXP, e-IXPC, e-IXPF series – Additional Installation, Operation and Maintenance Instructions
17
4.2.4
Frame installation
•
The frame must be rigid and must not vibrate during operation
•
The pump and motor feet support bases must be as level as possible
•
Position the pump and the motor at a distance that allows the coupling to be fitted
•
Ensure a gap of 4-6 mm (0.16-0.24 in) between the frame and the motor to allow for vertical
adjustment in case of replacement.
•
Make sure that pump and motor are securely attached to the frame.
4.3
Hydraulic connection
4.3.1
Precautions
WARNING:
Piping must be sized to ensure safety at the maximum operating pressure.
WARNING: Danger of hot and/or toxic liquid escaping from non-sealed piping system
connections
Support the piping system independently to prevent them from weighing on the unit. Secure
the piping system to the unit ports making sure to comply with the permitted forces and
torques. Install appropriate gaskets between the unit and the piping system.
WARNING: Hot surface hazard
If the temperature exceeds 60°C (140°F), isolate the unit before touching it.
NOTE:
When carrying out welding activities never use the unit for grounding: risk of pitting damage
to the bearings.
4.3.2
Guidelines for the hydraulic system
1.
Support the piping system independently to prevent them from weighing on the unit.
2.
Remove any welding residues, deposits and impurities in the pipes that could damage the
unit; install a filter if necessary.
3.
To reduce the transmission of vibrations between the unit and the system and vice versa,
install:
•
anti-vibration joints on the suction and discharge sides of the unit
•
dampers between the unit and the surface on which it is installed.
4.
In order to reduce flow resistance, the pipe on the suction side must be:
•
As short and as straight as possible
•
For the section connected to the unit, straight and without bottlenecks, covering a
length equal to at least six times the diameter of the suction port
•
Wider than the suction port; if necessary, install an eccentric reducer that is horizontal on
top
•
Without bends; if this cannot be avoided, bends of a radius as wide as possible
•
Without traps and 'goosenecks'
•
With valves with a low specific flow resistance.
5.
Install a check valve on the discharge side to prevent the liquid from flowing back into the
pump unit when this is at standstill.
6.
Install a pressure gauge (or a vacuum pressure gauge, in case of suction lift installation) on
the suction side, and a pressure gauge on the discharge side, for checking the actual
operating pressure of the pump unit.