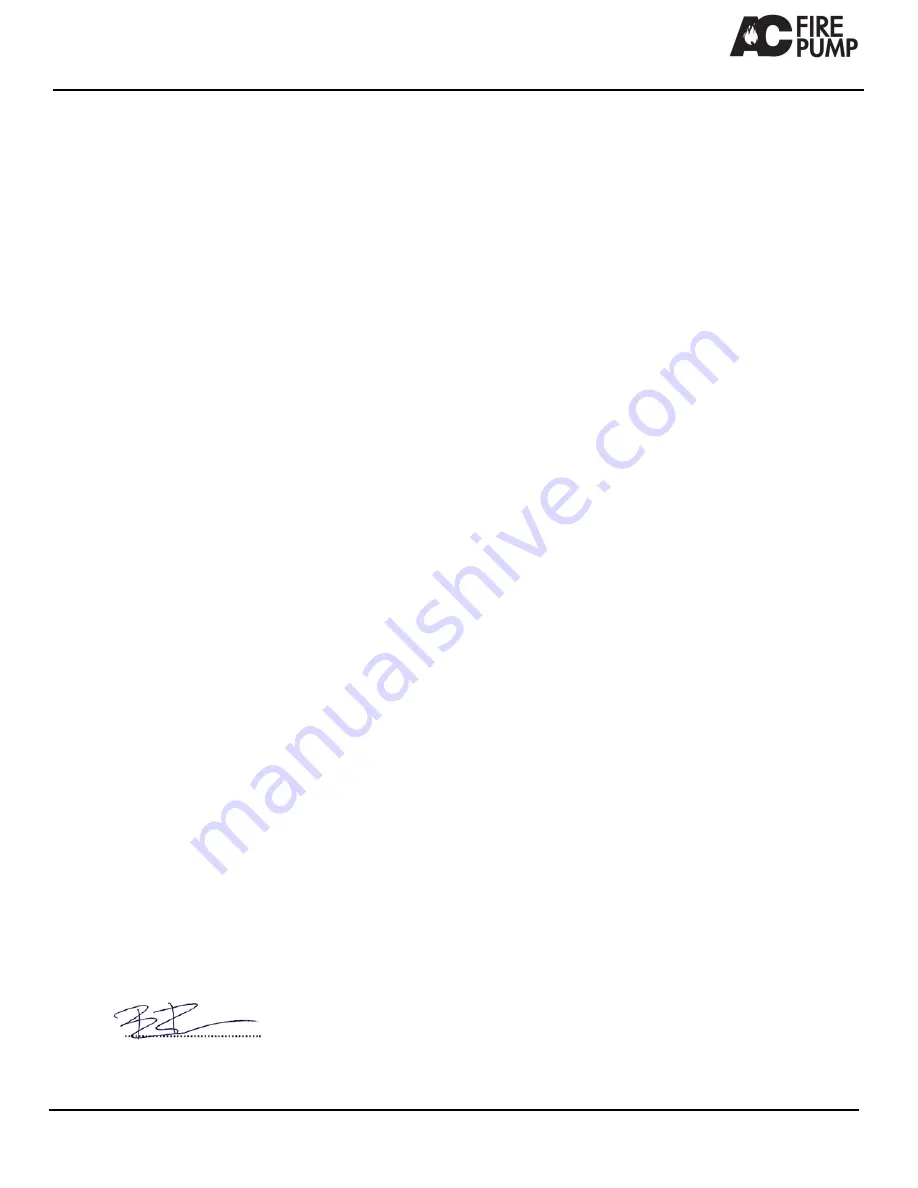
AC6102 Rev 0
5
2
EC Declaration of Conformity
Pump supplied complete with driver
We, the manufacturer:
A-C Fire Pump Systems
8200 N. Austin Ave.
Morton Grove, IL 60053,
USA,
declare under our sole responsibility that the product
Horizontal Split Case Centrifugal Fire Pump, Series 8100,
8150, 8200, and 9100; to which this declaration relates,
fulfills the relevant provisions of the following European
Directive(s), Standard(s) or other normative document(s):
Directives:
-
Machinery Directive (2006/42/EC).
-
Low Voltage Directive (2006/95/EC).
Standards used:
-
EN 809:1998+A1:2009.
-
EN ISO 12100:2010.
-
EN 60204-1:2006+A1:2009.
Pump supplied without driver
We, the manufacturer:
A-C Fire Pump Systems
8200 N. Austin Ave.
Morton Grove, IL 60053,
USA,
declare under our sole responsibility that the product
Horizontal Split Case Centrifugal Fire Pump, Series 8100,
8150, 8200, and 9100; to which this declaration relates,
fulfills the relevant provisions of the following European
Directive, Standard(s) or other normative document(s):
Directives:
-
Machinery Directive (2006/42/EC).
Standards used:
-
EN 809:1998+A1:2009.
-
EN ISO 12100:2010.
The pump covered by this declaration must not be put into
service until the equipment into which it is to be incorporated
has been declared in conformity with the provisions of the
Directive.
The technical file can be supplied, in response to a reasoned
request by the competent national authorities, through our
authorized representative established in the European
Community:
Mauro Caldarde,
CoE Engineering Manager,
Lowara S.r.l. Unipersonale,
Via Vittorio Lombardi 14,
36075 Montecchio Maggiore,
Vicenza, Italy.
Brian Buscher
Morton Grove, Illinois
Product Line Manager
October 7, 2015
Summary of Contents for AC Fire Pump 8100 Series
Page 2: ...Series 8100 8150 8200 9100 Fire Pump 1 AC6102 Rev 05...
Page 4: ...Series 8100 8150 8200 9100 Fire Pump 3 AC6102 Rev 05...
Page 8: ...Series 8100 8150 8200 9100 Fire Pump 7 AC6102 Rev 05...
Page 41: ...AC6102 Rev 05 40 Table 14 Troubleshooting List...
Page 50: ...Series 8100 8150 8200 9100 Fire Pump 49 AC6102 Rev 05 A Appendix...