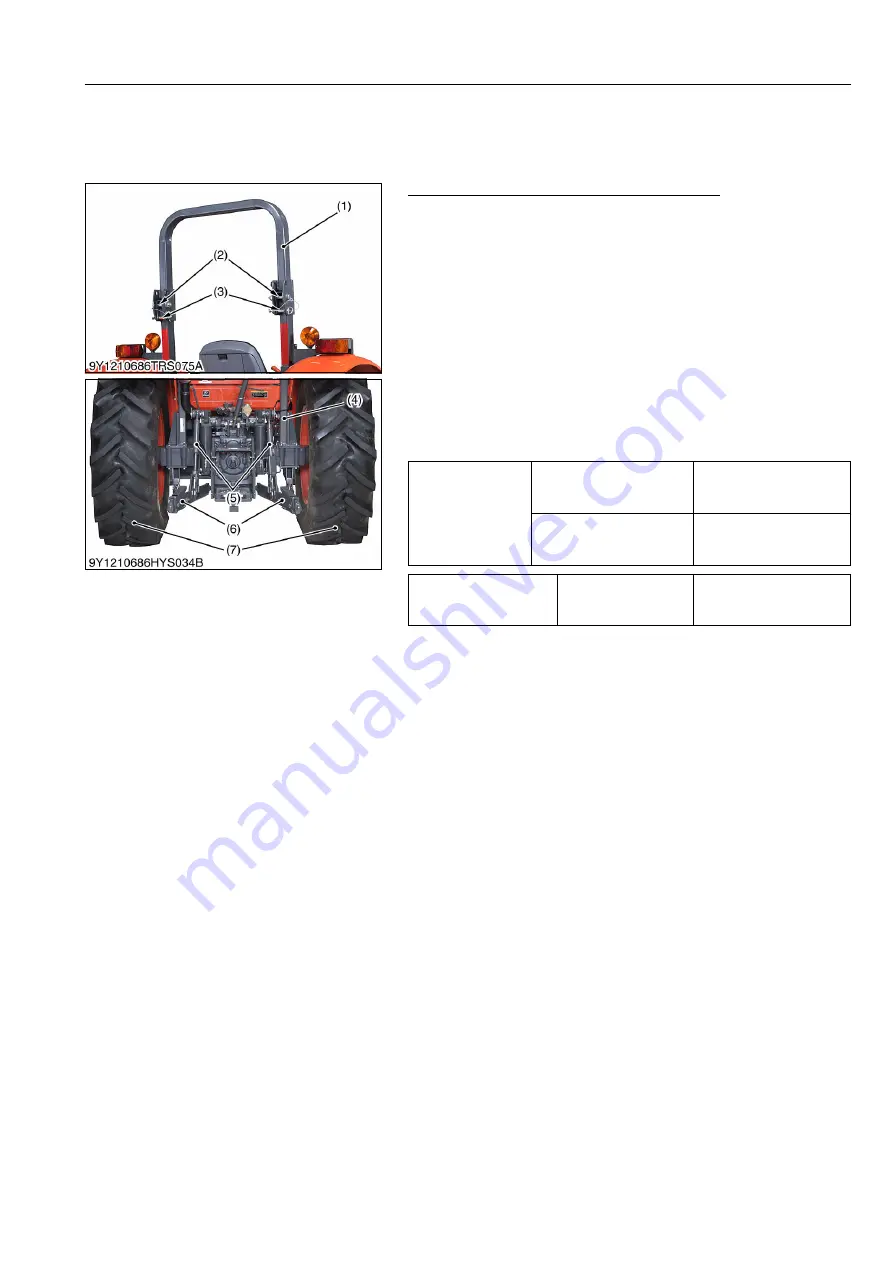
TRANSMISSION
M6060, M7060, WSM
2-S27
[4] SEPARATING CLUTCH HOUSING CASE FROM TRANSMISSION
CASE
(1) Preparation for ROPS Model
ROPS, Lower Link, Lift Rod and Rear Wheel
1. Loosen the ROPS under frame (4) mounting screws. (Do not
remove screws.)
2. Remove the ROPS upper frame (1).
3. Remove the lift rod (5) and lower link (6).
4. Chock the front wheels and place the disassembling stand
under the transmission case.
5. Remove the both rear wheels (7) and then place the
disassembling stand under the rear axle case.
6. Remove the fuel tank.
(When reassembling)
• To assemble the ROPS, fix the upper frame with screw (2) and
pin (3) temporarily, then tighten the under frame screws evenly
with specified torque.
• Adjust the upper frame does not fall down with screw (2).
9Y1210828TRS0034US0
Tightening torque
Rear wheel mounting nut
260 to 304 N·m
26.5 to 31.0 kgf·m
191.8 to 224.2 lbf·ft
ROPS under frame
mounting screw (M16, 9T)
260 to 304 N·m
26.5 to 31.0 kgf·m
192 to 224 lbf·ft
ROPS upper frame lift up
force at center of upper
frame
Reference value
246 to 284 N
25.0 to 29.0 kgf
55.2 to 63.9 lbf
(1) ROPS Upper Frame
(2) Screw
(3) Pin
(4) ROPS Under Frame
(5) Lift Rod
(6) Lower Link
(7) Rear Wheel
KiSC issued 08, 2013 A
Summary of Contents for M6060
Page 1: ...M6060 M7060 WORKSHOP MANUAL TRACTOR KiSC issued 08 2013 A...
Page 3: ...I INFORMATION KiSC issued 08 2013 A...
Page 9: ...INFORMATION M6060 M7060 WSM I 5 9Y1210828INI0002US0 KiSC issued 08 2013 A...
Page 10: ...INFORMATION M6060 M7060 WSM I 6 9Y1210828INI0003US0 KiSC issued 08 2013 A...
Page 11: ...INFORMATION M6060 M7060 WSM I 7 CABIN Model 9Y1210828INI0004US0 KiSC issued 08 2013 A...
Page 12: ...INFORMATION M6060 M7060 WSM I 8 9Y1210828INI0005US0 KiSC issued 08 2013 A...
Page 20: ...INFORMATION M6060 M7060 WSM I 16 CABIN Model 9Y1210828INI0012US0 KiSC issued 08 2013 A...
Page 21: ...G GENERAL KiSC issued 08 2013 A...
Page 132: ...1 ENGINE KiSC issued 08 2013 A...
Page 239: ...2 TRANSMISSION KiSC issued 08 2013 A...
Page 332: ...3 REAR AXLE KiSC issued 08 2013 A...
Page 333: ...CONTENTS 1 FEATURES 3 M1 MECHANISM KiSC issued 08 2013 A...
Page 350: ...4 BRAKES KiSC issued 08 2013 A...
Page 383: ...5 FRONT AXLE KiSC issued 08 2013 A...
Page 410: ...6 STEERING KiSC issued 08 2013 A...
Page 411: ...CONTENTS 1 STEERING MECHANISM 6 M1 2 STEERING CYLINDER 6 M2 MECHANISM KiSC issued 08 2013 A...
Page 428: ...7 HYDRAULIC SYSTEM KiSC issued 08 2013 A...
Page 474: ...8 ELECTRICAL SYSTEM KiSC issued 08 2013 A...
Page 477: ...ELECTRICAL SYSTEM M6060 M7060 WSM 8 M2 2 Lighting System KiSC issued 08 2013 A...
Page 479: ...ELECTRICAL SYSTEM M6060 M7060 WSM 8 M4 4 Main Control System Tractor ECU KiSC issued 08 2013 A...
Page 483: ...ELECTRICAL SYSTEM M6060 M7060 WSM 8 M8 2 Lighting System KiSC issued 08 2013 A...
Page 484: ...ELECTRICAL SYSTEM M6060 M7060 WSM 8 M9 3 4WD Transmission Control System KiSC issued 08 2013 A...
Page 486: ...ELECTRICAL SYSTEM M6060 M7060 WSM 8 M11 5 Working Light and Radio KiSC issued 08 2013 A...
Page 487: ...ELECTRICAL SYSTEM M6060 M7060 WSM 8 M12 6 Air Conditioner KiSC issued 08 2013 A...
Page 488: ...ELECTRICAL SYSTEM M6060 M7060 WSM 8 M13 7 Wiper System KiSC issued 08 2013 A...
Page 509: ...2 ALTERNATOR 8 S61 KiSC issued 08 2013 A...
Page 572: ...9 CABIN KiSC issued 08 2013 A...