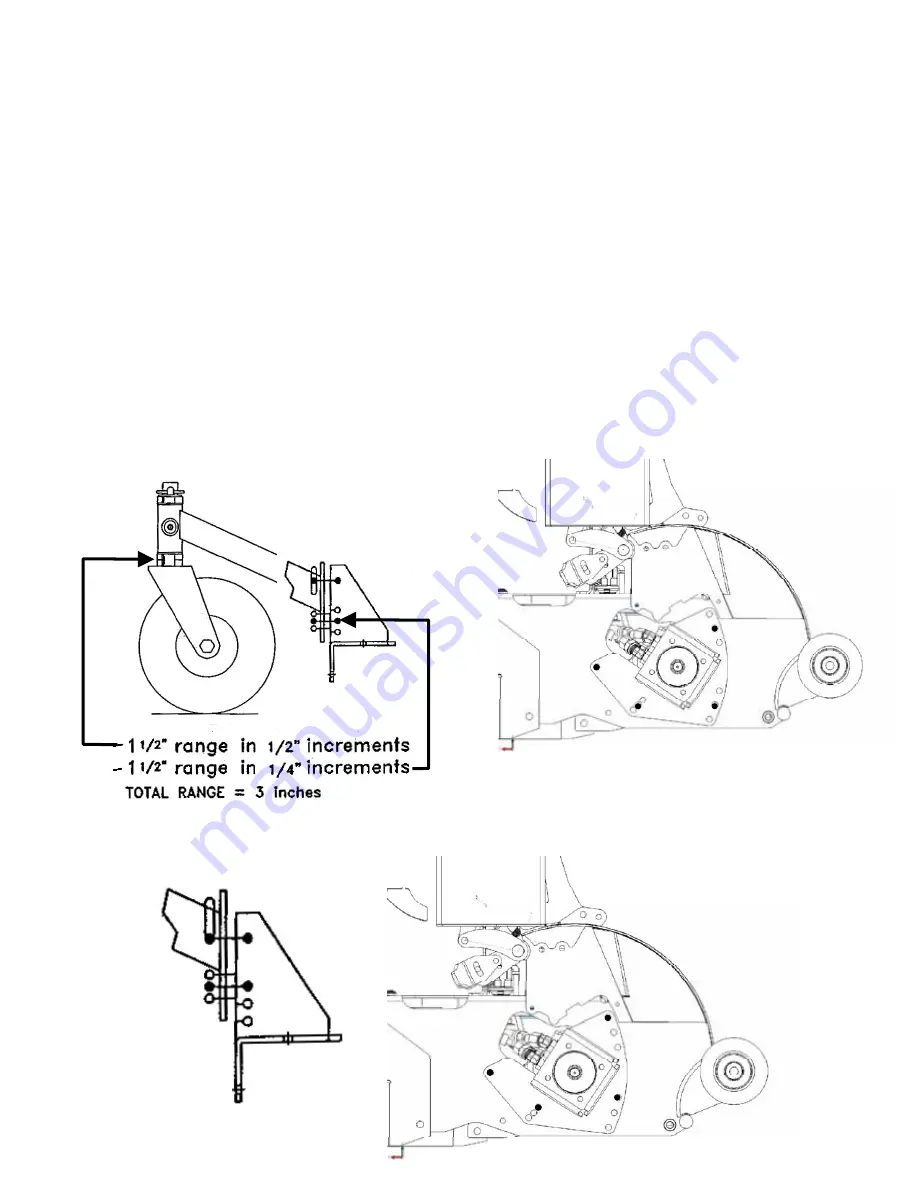
Deck Height Adjustments
WSS
Blade Adjustments and Height-of-Cut
Before Adjusting the Height-of-Cut be sure of proper air pressure in all four tires and check
for even tire wear. The height-of-cut can be adjusted the following ways:
¾
Coarse Adjustment
: For the coarse adjustment the rear motor support (
1
) and the front
caster arm (
2
) should be adjusted at the same time. Adjust the rear wheel motor
supports equally in one of the three settings up or down 0.75" each in a 1.5" total range.
¾
Fine Adjustment
: Adjust the blades equally in five settings up or down 0.25" each in a
1.25" total range. The shims on the blade bolts are moved from under the spindle to the
top of the spindle. If possible, leave at least one shim at the top and the bottom of the
spindle shaft.
Use the middle holes in tractor frame for cutting heights of 2.5" - 3.75", factory
setting 3”.
Use the highest holes in tractor frame for cutting heights of 1.75" - 3.0".
1
2
40
Summary of Contents for WSES36
Page 1: ...2007 Service Handbook WHAT IT MEANS TO RIDE WRIGHT ...
Page 2: ......
Page 4: ......
Page 5: ...2007 Service Handbook Forms 1 ...
Page 11: ...2007 Service Handbook Service Bulletins 7 ...
Page 30: ...Bulletin 058 3 Pages June 29 2006 Bottom view of new routing configuration Fig 3 26 ...
Page 37: ...2007 Service Handbook Service and Repair 33 ...
Page 46: ...Deck Height Adjustments WS WV Hydro 2 5 3 75 3 25 4 5 1 75 3 0 3 42 ...
Page 66: ......
Page 67: ......
Page 68: ...4600X Wedgewood Blvd Frederick MD 21703 www wrightmfg com ...