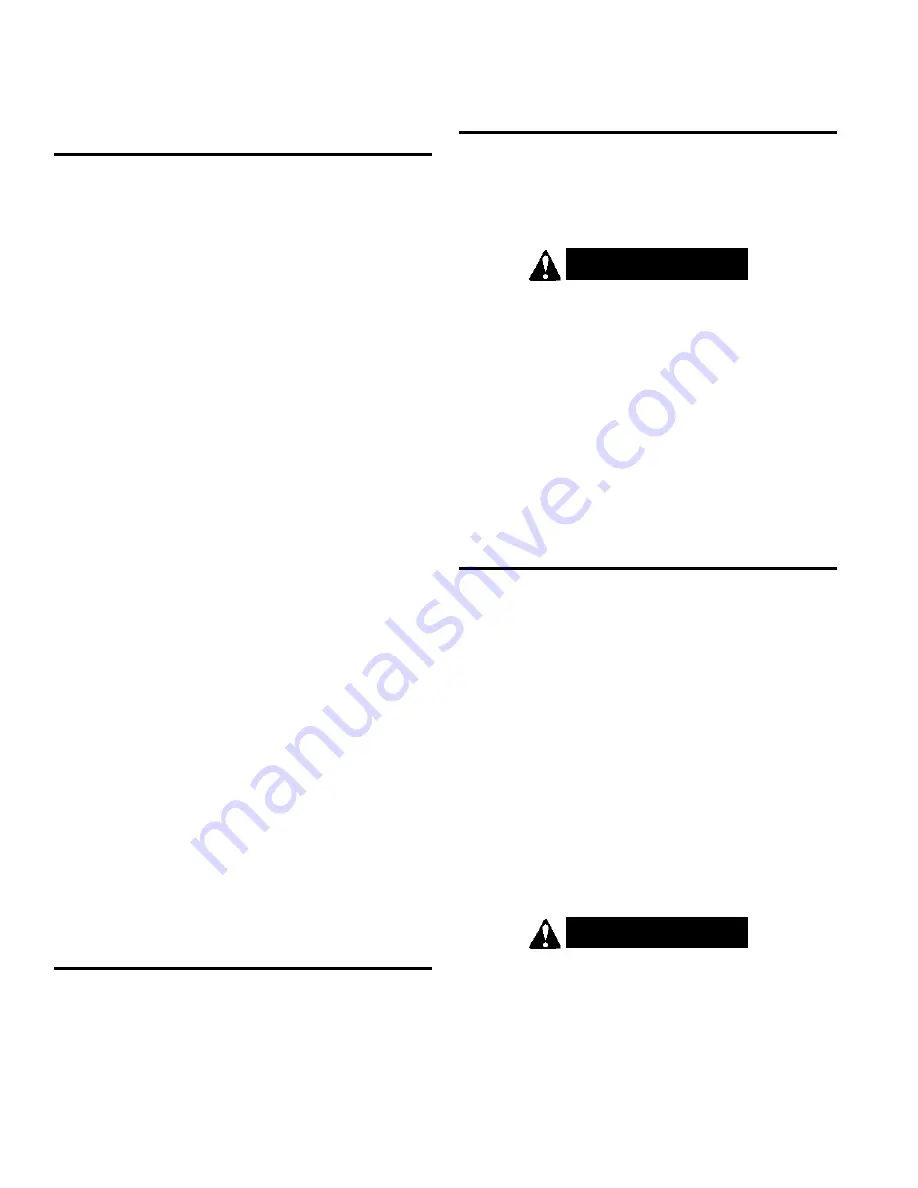
13
INSTRUCTIONS
(continued)
NOTE:
The lift channel brackets are supplied with 1”
diameter pins to fit your loader. If your loader requires
1
1
/
8
” pins, it will be necessary for the hole diameter in the
channel brackets to be drilled out to 1
5
/
32
” (1.156”) and
ask your dealer to order 1
1
/
8
” diameter pins. The 1
1
/
8
” pins
are part #830318. Be sure to indicate if two or four 1
1
/
8
”
pins are required.
If your loader requires 1
1
/
4
” diameter pins, please ask
your dealer to order adapter bushings (part #830319). Be
sure to indicate how many adapter bushings are
required.
NOTE:
The Ford (New Holland) models 7109, 7209,
7210, 7309, 7310 and 7410 Pin Type Loaders require
special brackets. Also, Rhino (Alamo) models 2410 and
2491. Order #830330 bracket kit.
NOTE:
For loaders that require brackets that provide
additional roll back, order #830335 (1” pins).
Connect the assembly to the loader arms using the bot-
tom hole in the channel and attach the upper control
cylinder to the top hole in the lift channels. Center the
main frame (side to side) with your loader arms and
tighten the four (4)
5
/
8
” x 3” U-Bolts.
The lower hole positions in the lift channels can be used
to obtain more angle movement. However, if the frame
becomes too parallel with the loader lift arms, the loader
may not have enough power (mechanical advantage) to
bring the frame back.
NOTE:
Generally, it is not recommended to have the tilt
cylinders located any closer than 10-12 inches to the
main loader lift arms.
Check the spacing of mounting
pins on your loader bucket and use this as a guide.
If tilt cylinders are located too close to the loader arms,
they may go “over center” when fully extended. If this
happens, damage may occur to the cylinders and/or
mounting brackets.
Remove the bucket from your skid steer unit and
connect the main frame of the Grapple Rake to the
universal quick-attach coupler.
The model SSGR-262, SSGR-277, and SSGR-84 have
a universal quick-attach bracket welded on the frame. No
special brackets are required. Make sure latch pins
engage slots to lock the frame in place.
Route the hoses (not supplied) back to your
tractor/loader remote hydraulic couplers. Be sure to allow
a loop of hose just behind the attachment to allow for the
tilt angles that will be encountered. Make sure that the
hoses are routed so they will not be pinched or snagged
by attachment pivot arms, loader, or tractor parts. Fasten
the hoses securely so they will remain in the correct
position and not drop down where they could be pinched
or sheared.
Use a good thread sealant. (
DO NOT USE TEFLON
TAPE
as this could cause hydraulic system problems in
your tractor or power unit.)
After making the hose connection between the
tractor/skid remote outlets and the grapple cylinders,
operate the grapple several times to work the air out of
the system.
ASSEMBLY – TRACTOR LOADERS
PIN ON ATTACHMENT
(continued)
To help prevent personal injury, stand clear of frame
and loader. Keep feet away from underside of main
frame.
Escaping hydraulic fluid under pressure can pene-
trate the skin, causing serious injury.
DO NOT use your hand to check for leaks. Use a
piece of cardboard or paper to search for leaks.
Stop engine and relieve pressure before connecting
or disconnecting lines.
Tighten all connections before starting engine or
pressurizing lines.
If any fluid is injected into the skin, obtain medical
attention immediately, or gangrene may result.
ASSEMBLY – SKID STEER AND
TRACTOR LOADERS
ASSEMBLY – QUICK ATTACH
SKID STEER MOUNTING
If your tractor loader has a bucket Quick Attach feature,
check with your dealer on the availability of adapter
brackets for your brand and model loader.
Measure the width of the front adapter on your loader
and locate the Quick Attach brackets on the main frame.
Locate these brackets so the main frame will be centered
on your loader.
Tighten the U-bolts that connect the brackets to the
main frame.
CAUTION
DANGER
Summary of Contents for FLGR-262
Page 21: ...20 OPTIONAL STAND KIT 811395...
Page 22: ...21 FRONT LOADER GRAPPLE PARTS DRAWING MODELS FLGR 262 FLGR 277...
Page 23: ...22 FRONT LOADER GRAPPLE PARTS LIST MODELS FLGR 262 FLGR 277...
Page 24: ...23 SKID STEER GRAPPLE PARTS DRAWING MODELS SSGR 262 SSGR 277...
Page 25: ...24 SKID STEER GRAPPLE PARTS LIST MODELS SSGR 262 SSGR 277...
Page 26: ...25 SKID STEER GRAPPLE PARTS DRAWING MODEL SSGR 84...
Page 27: ...26 SKID STEER GRAPPLE SSGR 84 HYDRAULIC DIAGRAM PARTS LIST...