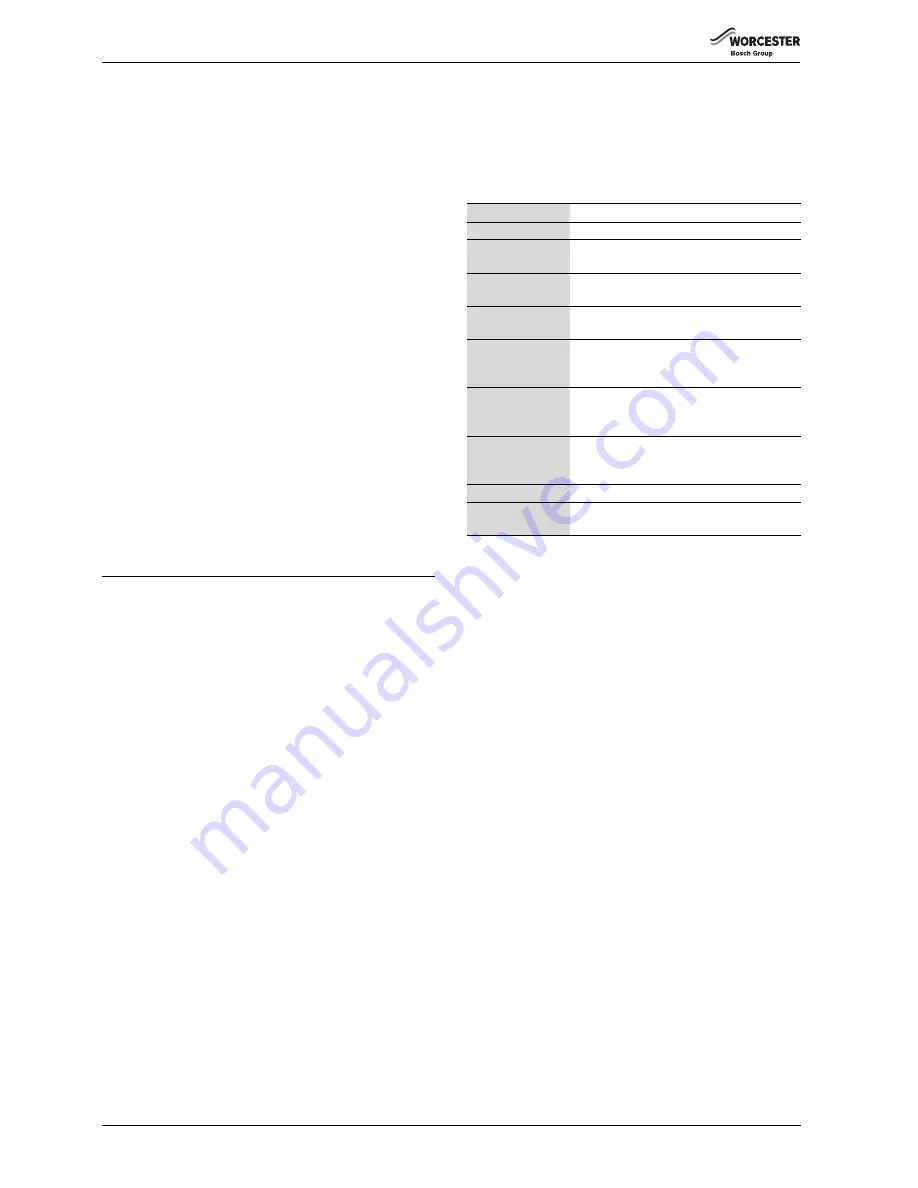
Installation regulations
Greenstar Heatslave II External
ErP -
6 720 813 345 (2014/09)
4
Fitting and Modification
Fitting the appliance and any controls to the appliance may only be
carried out by a competent engineer in accordance with these
instructions and the relevant Installation Regulations.
Flue systems must not be modified in any way other than as described in
the fitting instructions.
Any misuse or unauthorised modifications to the appliance, flue or
associated components and systems could invalidate the warranty.
The manufacturer accepts no liability arising from any such actions,
excluding statutory rights.
Electrical work
Electrical work must only be carried out by a qualified electrician.
▶ Before starting electrical work:
– Isolate the mains electrical supply and secure against
unintentional re-connection.
– Check for zero potential.
▶ Also observe connection diagrams of other system components.
Handover to the user
When handing over, instruct the user how to operate the heating system
and inform him about its operating conditions.
▶ Explain how to operate the heating system and draw the user's
attention to any safety-relevant action.
▶ Explain that modifications and repairs must only be carried out by an
authorised contractor.
▶ Advise the user to have the system serviced annually by a competent,
qualified engineer, such as an OFTEC registered engineer.
▶ Leave the installation instructions with the completed
commissioning form with the homeowner.
2
Installation regulations
2.1
Complying with the building regulations
This heating appliance forms part of the controlled services for the
building. It is law that all controlled services for buildings must comply
with building regulations. You must be able to satisfy your Local
Authority Building Control Body (LABC) that the work carried out
concerning the installation and commissioning of this heating appliance
has been carried out to a satisfactory standard.
OFTEC operate a competent persons scheme and registered installers
are able to certify that their work complies with building regulations.
Under the scheme;
• OFTEC must be informed about every installation.
• OFTEC will issue a building regulations compliance certificate to the
householder and will notify the LABC.
OFTEC provide controlled document forms CD10 and CD11 for use
during installation and commissioning respectively.
Other organisations operate self-certification schemes e.g. NAPIT and
BESCA Ltd. and it may be possible for installers who are members of
these organisations to self certify their work.
Alternatively you must submit a building control notice to the LABC
before installing any boiler. The LABC will then arrange regular
inspection visits during the work to ensure that the installation complies
with the regulations.
Installation
Failure to install appliances correctly could lead to prosecution.
The appliance should be installed by a competent person. The person
installing the appliance should be aware of the Health and Safety at Work
Act and take appropriate action to ensure that the regulations are
adhered to. In order to give optimum efficiency and trouble free
operation the appliance must be commissioned by a qualified OFTEC
engineer.
The compliance with a British Standard does not, in itself, confer
immunity from legal obligations. In particular the installation of this
appliance must be in accordance with the relevant requirements of the
following British Standards and regulations in respect of the safe
installation of equipment:
The Building Regulations Part G, Part J and L1 England and Wales;
Part F, Part G and Part J Section III Scotland; Part L and Part F Northern
Ireland.
Local water company bye-laws.
The Control of Pollution (Oil) Regulations.
OFTEC Standards.
Where no specific instruction is given, reference should be made to the
relevant codes of practice.
Installations in Eire (Republic of Ireland)
The Installation must be performed by a competent and suitably trained
person in accordance with the following Eire regulations.
Current Building Regulations - Republic of Ireland
ETCI rules for electrical installation
For further guidance see
OFTEC Technical book three - Regional requirements: Republic of
Ireland
BS 5410: part 1:
Code of practice for Oil Fired Boilers.
BS 799: part 5:
Specification for Oil Storage Tanks
BS 7593:
Code of Practice for treatment of water in
domestic hot water central heating systems.
BS 5449: part 1:
Specification for forced circulation hot water
central heating for domestic premises.
BS EN 12828: 2012
+A1: 2014
Heating systems in buildings.
Design for water-based heating systems
BS 7291:
Thermoplastic pipes and associated fittings for
hot and cold water for domestic purposes and
heating installations in buildings
BS 7074: part 1:
Application, selection and installation of
expansion vessels and ancillary equipment for
sealed water systems.
BS 1254-2:
Copper and copper alloys plumbing fittings part
2: Fittings with compression ends for use with
copper tubes.
BS 7671:
IET Wiring Regulations, current edition.
BS 1362:
Specification for general purpose fuse links for
domestic and similar purposes.