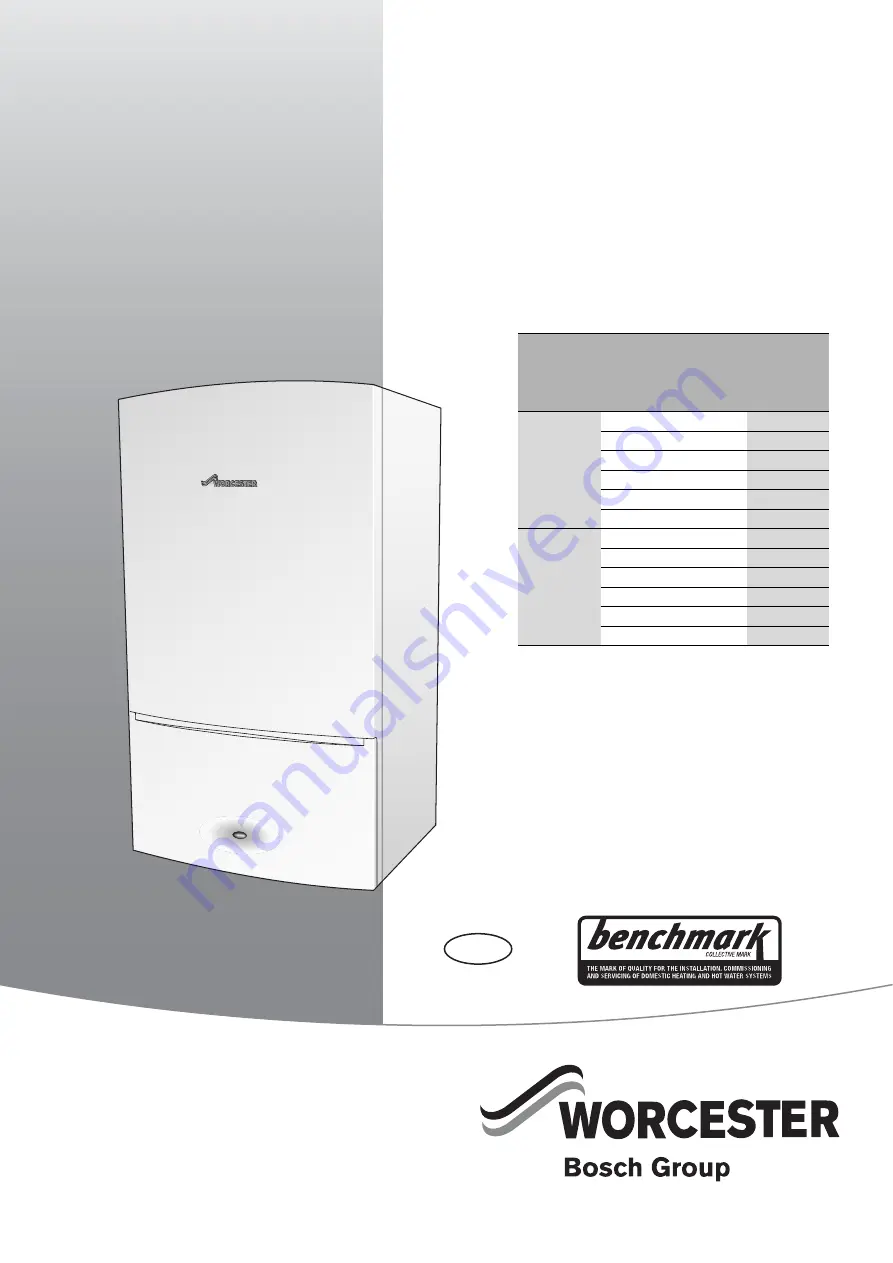
UK/IE
Installation commissioning and servicing instructions
Wall hung RSF gas fired condensing system boiler
Greenstar i System
ErP
6720806944-00.1W
o
For sealed central heating systems and indirect mains fed domestic hot water
6 72
0 806 945 (2015/07)
If you smell gas:
▶ Well away from the building: call the National Gas Emergency
Service on 0800 111 999.
▶ L.P.G. boilers: Call the supplier’s number on the side of the gas
tank.
These appliances are for use with:
Natural Gas or L.P.G.
(Cat. II 2H 3P type C13, C33 & C53)
Model
GC Number
Natural Gas
Greenstar 9i System
ErP
41-406-21
Greenstar12i System
ErP
41-406-23
Greenstar 15i System
ErP
41-406-25
Greenstar 18i System
ErP
41-406-27
Greenstar 21i System
ErP
41-406-29
Greenstar 24i System
ErP
41-406-31
L.P.G.
Greenstar 9i System
ErP
41-406-22
Greenstar12i System
ErP
41-406-24
Greenstar 15i System
ErP
41-406-26
Greenstar 18i System
ErP
41-406-28
Greenstar 21i System
ErP
41-406-30
Greenstar 24i System
ErP
41-406-32